Precautions for Sensor Installation
FAQ|Precautions for Sensor InstallationProper installation of vibration sensors can improve measurement accuracy and ensure reliable results. If a vibration sensor is not installed correctly, measurement deviations or failures may occur.
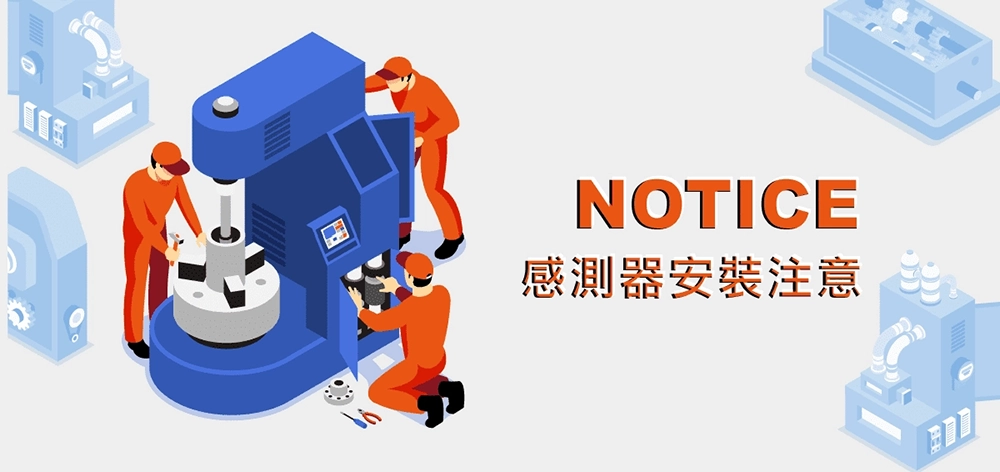
Sensor Installation
Ensuring Measurement Accuracy with Proper Sensor Installation
Maintain Consistency in Measurement Points
Proper installation of vibration sensors can enhance measurement accuracy and ensure reliable results. If not installed correctly, measurement errors may occur. Therefore, when performing vibration measurements, it is crucial to carefully consider factors such as installation position, method, and direction to ensure accuracy. Additionally, for periodic inspections, measurement points should remain consistent to avoid excessive data deviations.
Key Considerations When Installing a Vibration Sensor
Installation Position: The vibration sensor should be installed at the optimal vibration detection point of the equipment. A thorough analysis of the mechanical structure is necessary to select the best location.
Installation Method: Typically, sensors can be installed using contact or non-contact methods. Non-contact vibration sensors can be fixed externally or attached to the equipment surface using a magnetic mount.
Cable Protection: Sensor cables must be well-protected to prevent damage during operation. Using cable sleeves or fixing clamps can help secure the cables effectively.
System Noise: When installing the sensor, environmental factors must be considered. If system noise interferes with vibration signals, the sensor should not be placed near the noise source.
Precision Requirements: Sensor accuracy is critical. Before installation, ensure that the required precision level is met and choose the appropriate sensor accordingly.
Testing and Verification: After installation, testing and verification should be conducted to confirm that the sensor is installed correctly and functioning properly.
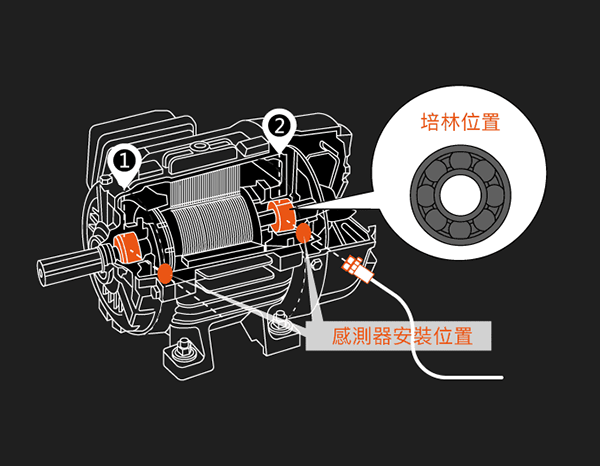
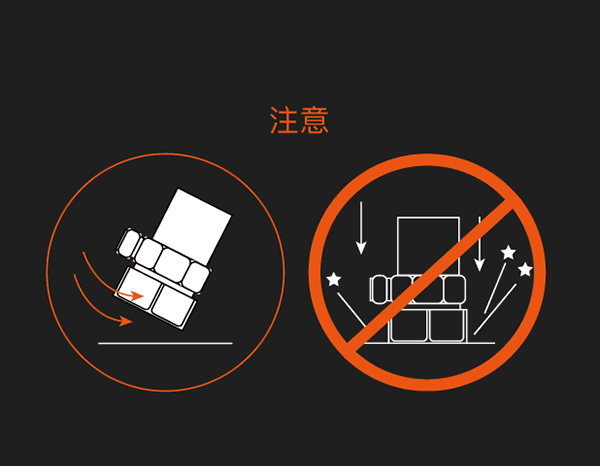
Attach the vibration sensor to the motor housing using a magnetic base (closest to the bearing).
Sensor usage precautions: Attach one side at an angle to the test object, then fully adhere the other side. Avoid direct impact on the sensor to prevent damage.
Precautions
Magnetic Mount Sensor Installation Precautions
Proper installation ensures accurate measurements
Magnetic Strength: The magnetic mount installation method typically uses a strong magnet. Ensure that the magnetic force is strong enough to securely fix the vibration sensor and prevent it from detaching during operation.
Surface Flatness: The vibration sensor must be mounted on a flat surface to ensure proper adhesion and accurate measurements.
Magnetic Interference: Strong magnetic fields may interfere with the vibration sensor. Avoid using the magnetic mount installation near strong magnetic sources.
Installation Position: Similar to contact-type installation methods, the best installation position should be chosen to accurately detect the vibration state of the equipment.
Cable Protection: The magnetic base used for installation often has a socket at the bottom for connecting the vibration sensor cable. Take care to protect the cable from damage.
Horizontal vs. Vertical Installation of Vibration Sensors
When installing a vibration sensor, it is important to choose the appropriate installation position and fixing method based on the actual conditions of the test object to ensure that the sensor is securely attached and does not shift or detach due to vibration. Common fixing methods include bolt fixing, magnetic mount fixing, and adhesive fixing.
1. Measurement directions are categorized into radial and axial, with radial measurements being the primary evaluation method.
2. Radial measurement data and trends are the main criteria for assessing machine health.
3. Axial measurements serve as supplementary verification.
4. Both radial and axial measurements follow the same ISO vibration standards.
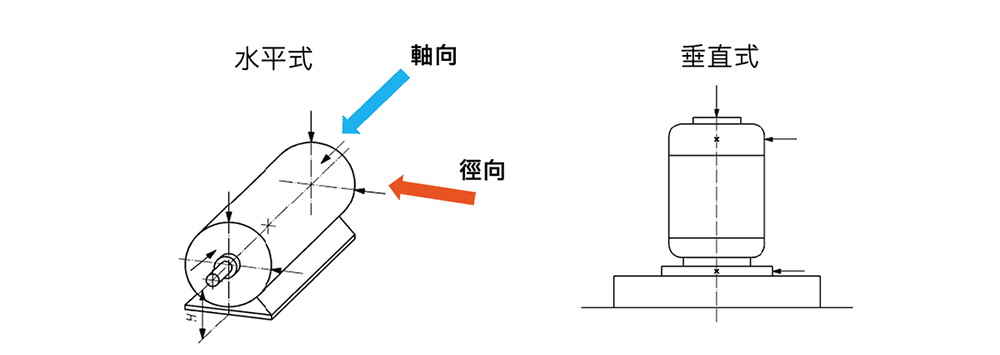
Spindle Measurement Method?
Place the sensor on the bearing or bearing housing of the machine casing to be measured.
The complete measurement directions include two radial points on the front side, two radial points on the rear side, and one axial point on the front side (as shown in the figure). Radial measurement points should be as orthogonal as possible. Each measurement should be taken at the same points, and the results should be recorded. All vibration standards should refer to the same ISO vibration standard.
The principle of sensor installation is to place it as close to the bearing as possible. The background vibration of the environment should not exceed 10% of the machine's stable operating vibration level.
Solution
How to Monitor the Status of a Robotic Arm?
Vibration Measurement Service
In laboratories or factories, vibrations can have direct or indirect effects on instruments and equipment. Minor vibrations may cause issues with experimental data, while severe cases can lead to equipment damage and significant losses.
Good Technology offers vibration measurement services that help identify the sources of vibrations in environments and equipment, minimizing their impact on experiments or manufacturing processes. Additionally, by measuring the vibrations of motor rotors and other machinery, we assist in evaluating equipment quality, enabling predictive maintenance. Optimize your costs and enhance productivity and operational efficiency!