AIoT Smart Industrial IoT
Technical Concept|AIoT Smart Industrial IoTBy using various sensors, real-time equipment data is collected and analyzed. Combined with AI training algorithms, it effectively predicts potential equipment failure points, helping users make the most accurate decisions.
Why Industrial IoT? Reasons for Implementation
Machines cannot speak; to understand their status, data must be received, transmitted, and communicated with other devices.
Industrial IoT serves as the medium for this communication, even enabling machine control to reduce manpower. In short, Industrial IoT is the means of interaction between machines and users.
In the industrial sector, Industrial IoT is widely used, covering physical data measurement for factory environments such as smart meters, temperature control, humidity, production line planning, and inventory management. It also includes monitoring machine signals such as production line counting, machine abnormal logs, and various built-in sensors, as well as dynamic edge computing signals for robotic arms, stamping equipment, and automated welding.
Industrial IoT primarily focuses on machine-to-machine communication, collecting big data from production processes, and finally analyzing it using edge computing, machine learning, and AI.
This process aims to enable machines to achieve self-perception, learning, decision-making, execution, and adaptation, ultimately leading to production line automation, improved process efficiency, and optimized factory management and control. The widespread adoption of Industrial IoT drives smart manufacturing and determines whether a factory's transformation into a smart factory is successful.
Common IoT communication environments include Ethernet, Wi-Fi, 3G, 4G, Bluetooth, ZigBee, RFID, and NFC.
Labor Saving
Equipment Understanding
Factory Management
Process Optimization
Decision Control
Industry Transformation
Feature Overview
GoodTech's Industrial IoT?
Based on monitoring and transmission methods, IIoT (Industrial IoT) is classified into two major categories: dynamic edge physical machine data (Edge IIoT) and steady-state physical machine signal data (IIoT).
Edge IIoT - Dynamic Edge Signal Processing:
Edge IoT processes dynamic signals through complex computing methods compared to traditional IoT systems. It involves more than just data interfacing and filtering. The goal is to convert physical quantities into meaningful monitoring indicators. For example, instead of just capturing temperature values, users are more interested in temperature differences and cooling rates. Edge signal processing simplifies massive data sets and, through AI and machine learning algorithms, converts them into actionable insights. These insights can be used to set threshold values, further optimizing equipment or production lines.
Edge IIoT :
It's not just about collecting large amounts of data; our special algorithms simplify complex signals, eliminating the need for users to configure complex settings or conduct secondary calculations. We present only the data that users need to see.
IIoT - Steady-State Physical/Machine Signal Classification & Transmission:
Handles steady-state physical signals such as temperature, humidity, and pressure, or machine signals such as counters, sensors, and anomaly logs. It supports various signal types such as 0-5V, 0-10V, 4-20mA, and Modbus RTU. Sensors collect physical data from machines, which is then analyzed, classified, and displayed on monitoring systems or HMIs.
IIoT - Steady-State Industrial IoT
Various environmental factors that may affect equipment quality, production processes, and even workplace safety are monitored using appropriate sensors. Data is presented in the simplest form, adaptable for small and medium enterprises and newly established factories. The system offers a flexible architecture tailored to the user's needs.
Feature Introduction
EDGE IIoT
The Best Tool for Monitoring Edge Devices - EDGE IIoT
Automated production line equipment comes in various types, each with different monitoring needs, requiring different sensors or methods for monitoring. Although precision equipment often comes with built-in monitoring for parameters such as temperature and pressure, users frequently need engineers to manually extract and compare the data, which is time-consuming and labor-intensive. With EDGE IIoT Edge Industrial IoT, engineers can free up their hands to make better and more precise decisions. In the semiconductor industry, network security is a major concern, and EDGE IIoT offers local network transmission and storage, computing on local servers without the need for cloud computing, effectively preventing security risks.
What is Edge Computing?Custom Monitoring
Based on monitoring needs
Customizable Thresholds
Incorporate human expertise
Local Processing
No security concerns
Unlimited Expansion
Infinite monitoring points
Critical Data
View only what matters
Alerts for Anomalies
Via email and LINE
Dynamic Edge Signal Processing - Edge IIoT
Edge Computing with Firmware & IPC for Machinery Dynamics
Convert physical quantities into meaningful monitoring parameters via edge computing.
Examples:
Temperature + Time Factor → Cooling/Heating Rate (Users see temperature difference)
Pressure + Time Factor → Pressure Drop/Increase Rate (Users see pressure change rate)
Vibration Signals → 'During operation' and 'Specific action' vibration signals
Displacement Signals × N → Horizontal level / Tilt angle (Users see inclination angle)
Objective:
1. Convert physical quantities into practical monitoring parameters through edge computing.
2. Manage and set threshold values for the required monitoring data autonomously.
3. Extract dynamic (raw data) feature values to optimize equipment production lines.
EDGE IIoT Application Cases
Firmware-Level Edge Computing
Utilizing Chips to Monitor Mechanical Dynamics: Application in Wafer Robot Arm Motion Quality Monitoring
Semiconductor manufacturing processes are highly complex and precise. Since wafer production has a high value, even minor equipment malfunctions can result in significant losses, such as defective products and wafer scratches. Therefore, maintaining stability and reliability across all processes is crucial. By leveraging EDGE IIoT Edge IoT to monitor critical process equipment and track equipment status, manufacturers can ensure production line stability and effectively maintain process quality.
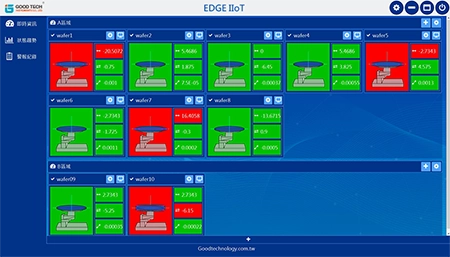
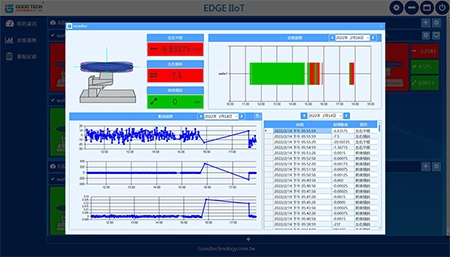
Utilizing Chips to Monitor Mechanical Dynamics: Application in Servo Motor Current Quality Monitoring
The servo motor is a critical component of industrial equipment. High-reliability power supplies often incorporate short-circuit or overload protection mechanisms. However, in many cases, important motors cannot be shut down during production. By using EDGE IIoT Edge IoT to monitor current values, it becomes possible to assess whether the motor load is excessive. Users can set threshold values, enabling real-time alerts in the event of abnormalities, facilitating prompt decision-making for optimal operational efficiency.
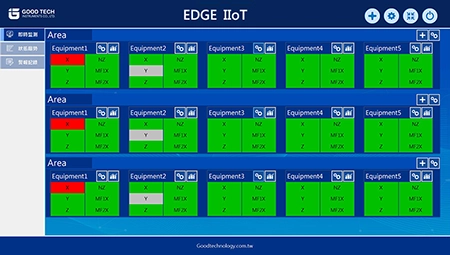
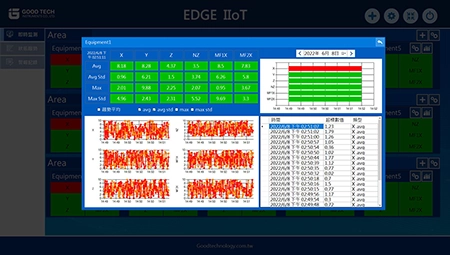
EDGE IIoT Application Cases
System-Level Edge Computing
Utilizing IPC to Monitor Mechanical Dynamics: Application in Long-Term Rotor Equipment Quality Monitoring
Factories contain a large number of rotor motor devices from various brands, distributed across different locations. If a critical rotor system supporting key equipment experiences a malfunction, it may lead to production line delays or defective products. By leveraging EDGE IIoT Edge IoT, unified monitoring of rotor equipment across different factory zones and configurations can be achieved. By measuring vibration signals from non-rotational parts of rotor machinery, it is possible to assess rotor health status, enabling predictive maintenance, early intervention, and the prevention of unexpected shutdowns. Additionally, by integrating the IMS-PR Motor Rotor Inspection Analyzer, an inspection map can be created to precisely monitor the health of rotor equipment.
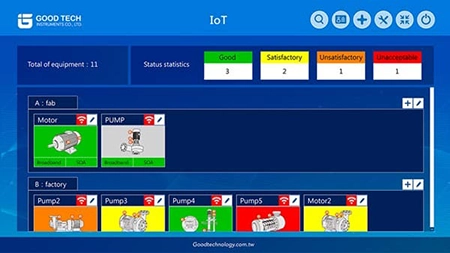
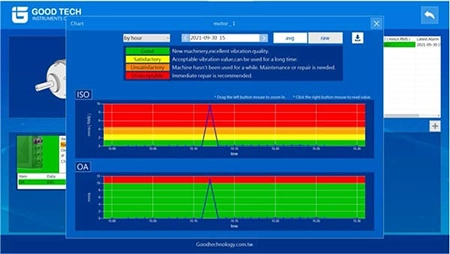
Utilizing IPC to Monitor Mechanical Dynamics: Application in Periodic Production Equipment Quality Monitoring
For crucial periodic equipment that significantly impacts the production line, various repetitive motion machines, such as robotic arms and stamping machines, can be individually monitored. The collected data is displayed in a centralized interface within EDGE IIoT Edge IoT, creating a small-scale operations center. This setup effectively enhances AIoT intelligence competitiveness, maintains production capacity, prevents product defects, and improves yield rates. In-depth analysis can be carried out using the VMS®-ML Machine Learning Intelligent Monitoring System for continuous monitoring and optimization.
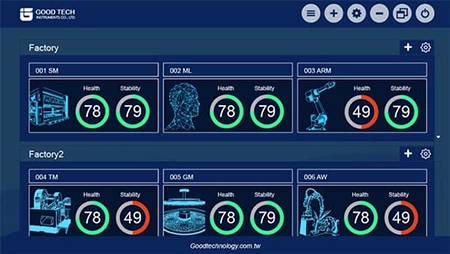
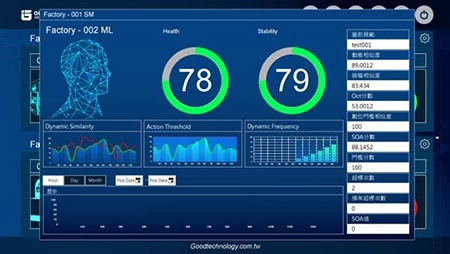
Feature Introduction
IIoT Stable IoT
The Best Tool for Monitoring Environmental Stability: IIoT
The impact of environmental factors on equipment requires long-term monitoring and observation. However, factory automation equipment is costly, and users often seek ways to cut costs while maintaining the same level of efficiency. The IIoT Industrial Internet of Things developed by GoodTech effectively enhances measurement efficiency, allowing users to detect and correct issues in real time. This not only saves time and money but also helps optimize budget allocation.
IIoT and Predictive Maintenance for Equipment
Higher Flexibility
Compatible with various sensors
Custom Thresholds
Incorporates human expertise
Wireless Transmission
Reduces excessive wiring costs
Unlimited Architecture
Expand monitoring points infinitely
Adaptable to All Sizes
Compatible with various screens
Abnormal Alerts
Notifications via mail & LINE
IIoT for Monitoring Steady-State Physical and Machine Signals
With the advancement of automation technology, sensors continue to be optimized and upgraded. More and more sensors integrating advanced computing technology are emerging, offering factories enhanced measurement solutions. GoodTech designs **comprehensive measurement processes** tailored to the **long-term operation of equipment in different factory areas and the specific values that need to be monitored**. By selecting appropriate sensor types based on environmental and equipment needs, and configuring data transmission methods to the factory's main system, real-time alerts can be sent, ensuring complete monitoring of the factory's stable-state system.
Physical Measurements: Temperature, humidity, pressure, particle detection, light detection, pressure sensors, photometers, water detection, liquid level, electrostatics, etc.
Machine Signals: Counting, sensors, anomaly records, logs, acceleration, motion detection, positioning, magnetism, current, voltage, etc.
Objective: Once sensor data is collected, it is categorized so that users can set threshold management.
Key Features:
1. Edge nodes directly analyze and transmit physical quantities (processing is done at the edge, not sent back to the system).
2. Continuous connectivity design (dual protection against disconnection).
3. Disconnection alerts/warnings.
4. Flexible expansion of monitoring points.
5. Supports multiple signal types: 0-5V, 0-10V, 4-20mA, Modbus RTU, Modbus TCP, I²C (Inter-Integrated Circuit), RS485, etc.
Temperature
Humidity
Pressure
Photometer
Light Detection
Water Detection
Liquid Level
Acceleration
Motion Detection
Flexibility
Behavior
Pulse Count
Magnetism
Resistance
AC Current
Current
Voltage
Particles
IIoT Application Cases
Industrial Safety
Industrial plants continuously emphasize safety, yet many deficiencies remain. Ensuring personnel safety is the most critical aspect.
In addition to using proper tools and safety equipment, implementing an automated monitoring system that provides timely alerts
can significantly reduce the occurrence of safety incidents.
Industrial safety is closely linked to environmental monitoring,
with standardized inspection processes and scheduled maintenance plans contributing to enhanced plant safety
and reduced unexpected equipment failures.
Smart factory safety management focuses on systemization, real-time monitoring, and reliability.
IIoT (Industrial Internet of Things) can be equipped with various sensors,
collecting a wide range of sensor data and visualizing it on monitoring dashboards.
Warning signals help in anomaly detection, providing instant insights and enabling remote monitoring with automated data logging.
Immediate alerts are sent when environmental anomalies are detected in the plant,
notifying operators in the most intuitive way to effectively prevent potential safety hazards.
For systems requiring long-term monitoring, IIoT allows real-time assessment of equipment conditions and trend analysis,
helping maintenance teams plan their schedules, identify issues early, and optimize manpower allocation.
Wireless Leak Detection System
The wireless leak detection system is designed to monitor environmental variables in plant leak rooms. With a fully customized design process and various sensors and buzzers, it enables real-time monitoring and alert notifications, allowing users to take corrective actions immediately. In industrial safety applications, it helps prevent accidents and ensures real-time safety monitoring.
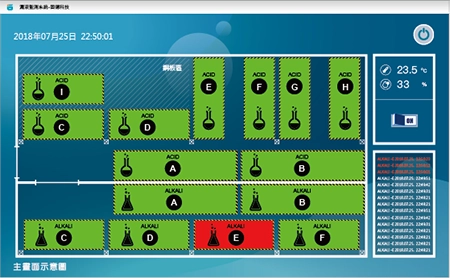
IIoT Application Cases
Process Impact
In the manufacturing process, IIoT provides real-time data monitoring, allowing operators to stay informed about production status. This helps to adjust operations in real time, ensure process stability, and quickly respond to any issues. IIoT not only collects production data but also performs in-depth analysis to identify potential problems and optimization opportunities. Through machine learning and artificial intelligence, it can predict process trends, optimize production workflows, and enhance productivity and quality.
Environmental Particle Monitoring System
In some production processes, the concentration of airborne particles can significantly impact product quality. For example, in semiconductor manufacturing, particles adhering to wafers can interfere with electronic component functionality. Therefore, maintaining low particle concentrations in cleanrooms is critical.
Environmental Factor Monitoring IoT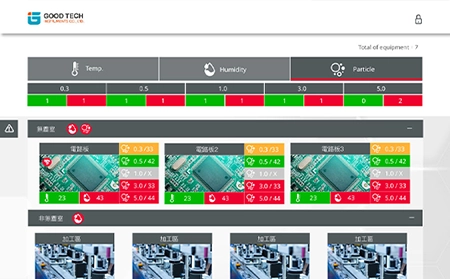
Equipment Power Monitoring System
Automated guided vehicles (AGVs) play a crucial role in transporting essential materials within the factory. If they remain in a low power or power-off state for extended periods, it may lead to material supply interruptions or delays, causing production disruptions, reduced operational efficiency, and increased labor and time costs.
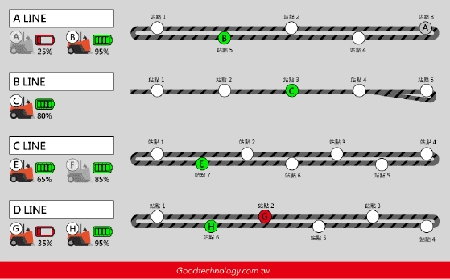
IIoT Application Cases
Environmental Sustainability
Applying Industrial IoT (IIoT) in the ESG (Environmental, Social, and Corporate Governance) sustainability sector helps companies achieve more sustainable environmental goals and business operations. IIoT technology provides enterprises with more opportunities to achieve sustainability objectives while improving operational efficiency and cost-effectiveness. However, when implementing IIoT technology, it is essential to carefully manage data privacy and security to ensure confidentiality and integrity.
Smart Energy Management System
The first step for enterprises to implement ESG initiatives usually starts with energy management. The Smart Energy Management System helps factories manage peak, off-peak, and mid-peak electricity usage, and even calculate carbon emissions, effectively assisting enterprises in quickly executing ESG plans.
Smart Energy Management System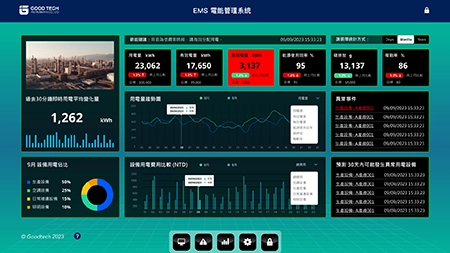
Smart Power Management System
The Smart Power Management System complies with the ISO50001 energy management standard, enabling precise energy management, cost reduction, and improved efficiency. It helps businesses meet government energy-saving and carbon reduction regulations, achieving an annual energy-saving rate of approximately 3-5% in the factory.
Smart Power Management Solution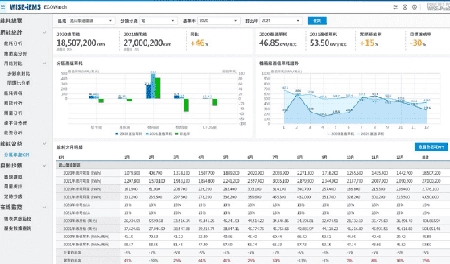
Process Optimization
AI Optimize
ISO Standards + AI Prediction
For continuous rotor equipment monitoring systems, this AI prediction model is optimized based on the initially established rule-based management principles, integrating traditional ISO10816/20816 standards and Remaining Useful Life (RUL) elements. Data cleansing and classification are fully automated, allowing users to select the specifications of rotating equipment and the desired prediction time at the start.
1. Equipment Risk Hierarchical Management
Equipment is managed by different levels of importance using different monitoring
methods such as inspections and online monitoring.
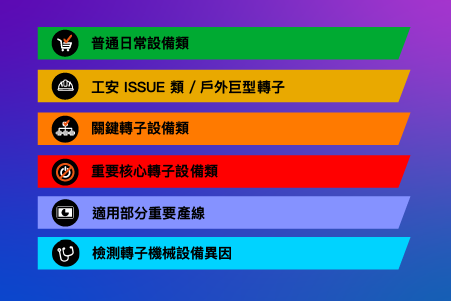
2. ISO Rotor Standards & Custom Thresholds
Easily apply expert standards to classify rotor quality by color, or set thresholds based on human experience.
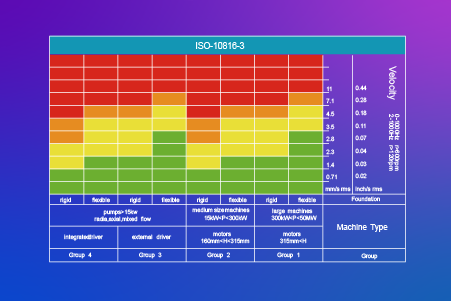
3. Feature Collection & Trend Analysis
Identify possible anomalies through spectrum analysis, accumulate feature data, and cross-analyze VRMS vibration signal data using AI.

4. AI Degradation Prediction
Based on rule-based management principles and built-in specifications, AI predictions forecast equipment aging and degradation.
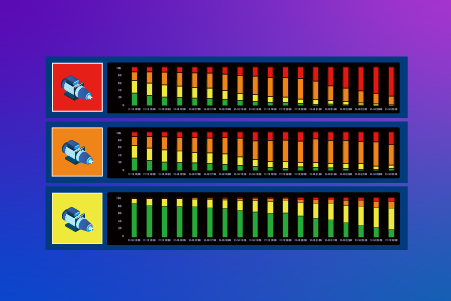
Machine Learning + AI Training
For periodic equipment monitoring systems, the weighting factors are derived from the collection of a large volume of feature data and extensive historical records of machine performance. Based on machine type characteristics, the AI training engine extracts feature values and optimizes weight distribution, normalizing it to a score ratio. Subsequent AI training predicts potential anomalies and helps monitor equipment conditions effectively.
1. Signal Tracking & Target Identification
The system establishes standards based on correct processes, automatically tracking and identifying signals.
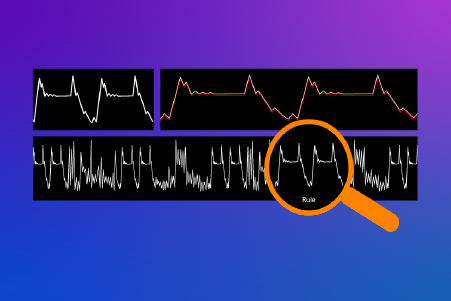
2. Model Scoring, Data Cleansing, Online Monitoring
Evaluate equipment performance, collect data, extract features, and perform real-time online monitoring.
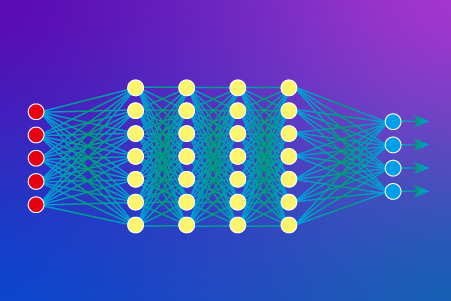
3. Feature Trend Accumulation & Management
Monitor feature value accumulation over time to anticipate equipment aging and adjust thresholds accordingly.
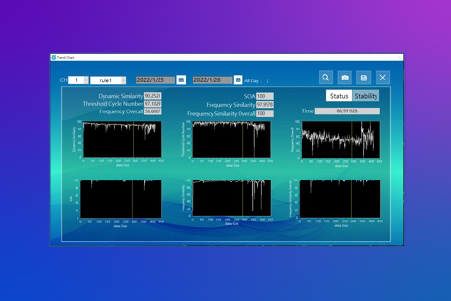
4. AI Retraining & Field Optimization
Continuous AI training to predict potential anomalies, monitor machine health, and optimize processes.
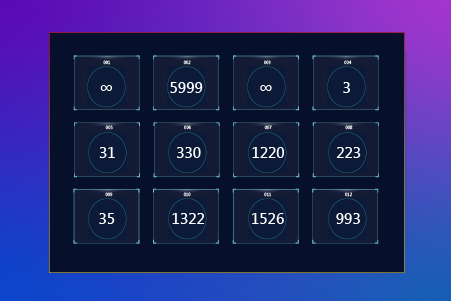