Manage Equipment Health with Vibration Measurement
FAQ|Manage Equipment Health with Vibration MeasurementMachines inevitably produce vibrations, but do you know whether they are normal or abnormal? Use measurement services to understand your equipment's health data.
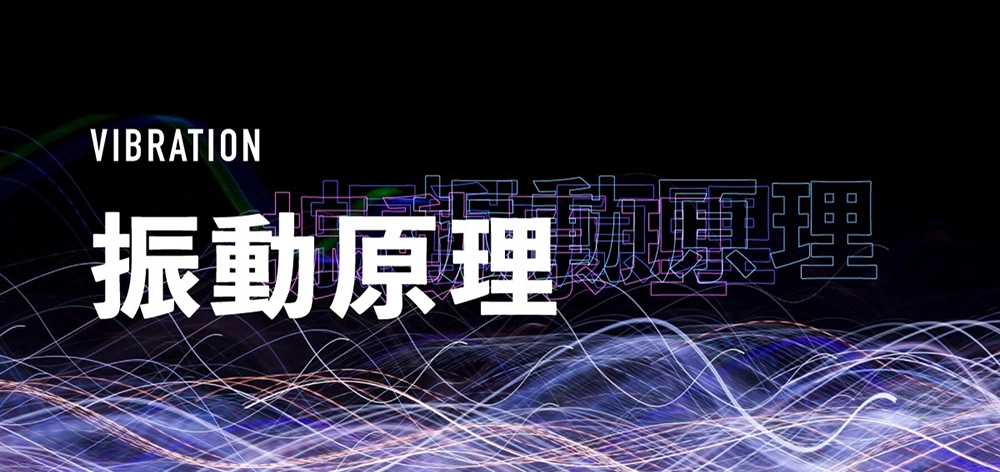
Why Use Vibration Measurement?
Vibration Data – A Key Indicator of Equipment Health
Machines inevitably produce vibrations, but do you know whether they are normal or abnormal?
Use measurement services to understand your equipment's health data.
Is your equipment experiencing abnormal vibrations? Did you know that environmental resonance can also affect
the operational quality of your machinery? To monitor the health status of equipment, it must have sensing capabilities.
By leveraging sensor technology and analyzing recorded signal data for deviations, we can determine whether the machine
is operating normally. These vibration signals help in early detection and prediction of potential machine failures,
aging, misalignment, and other complex dynamic behaviors. It serves as a crucial indicator for improving production
yield and research efficiency.
What is Vibration?
Sources of Vibration
Vibration refers to the back-and-forth motion of an object relative to a stationary reference or its equilibrium state. It can consist of a single frequency, a few frequencies, or a combination of many frequencies and can be either periodic or non-periodic (random). The causes of vibration include static and dynamic imbalance in rotating bodies, inertial forces in reciprocating motion, and impact load variations.
What is Vibration?
Composition of Vibration Signals
Vibration signals are generated by multiple components, and by applying Fast Fourier Transform (FFT), the frequency domain signals and their frequency composition can be obtained.
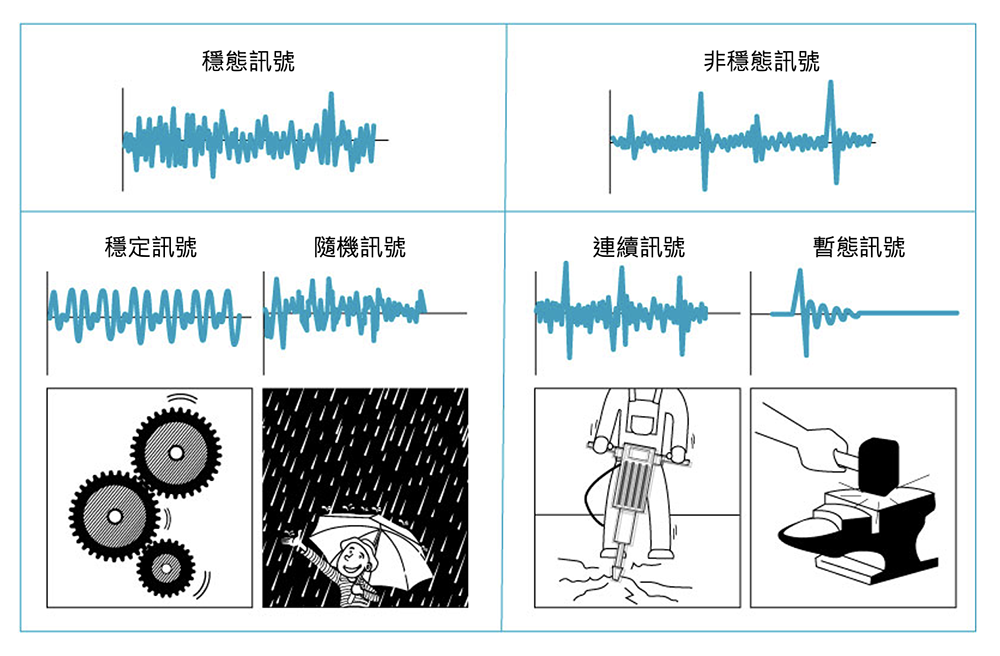
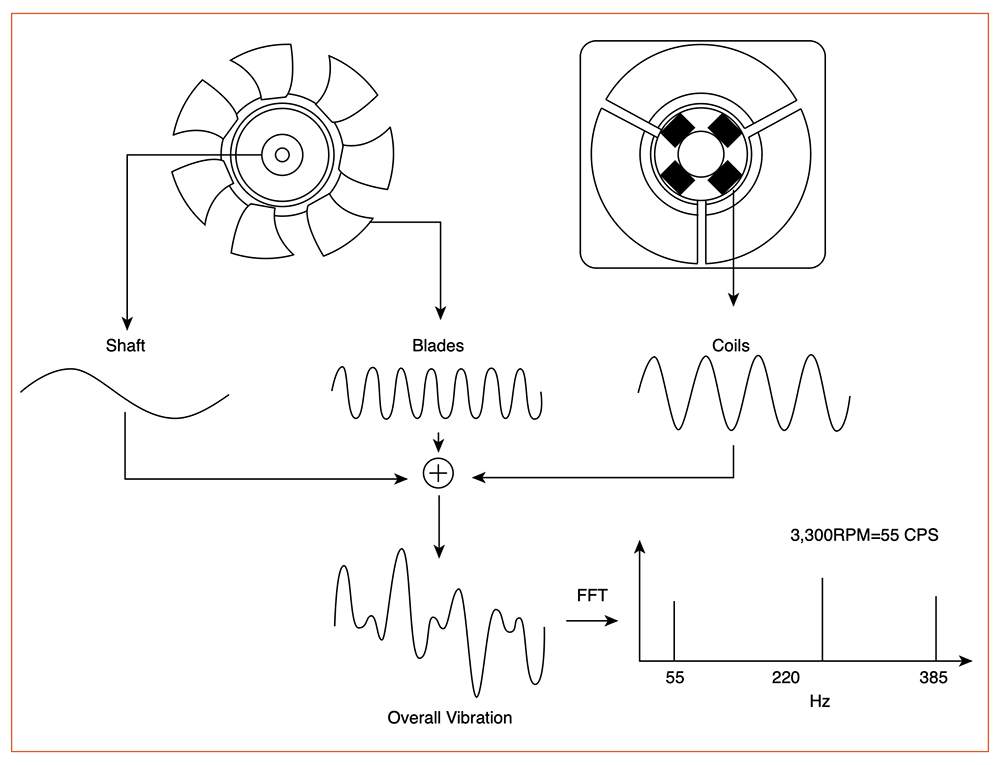
What is Vibration?
How Vibration is Generated in Rotating Equipment
Any equipment that rotates around a central axis is considered rotating equipment. Common examples in factories include fans, motors, pumps, and compressors. Other typical industrial equipment structures include moving screws, belt-driven mechanisms, robotic arms, rotating tools, cutting machines, and joining equipment. However, no rotating machinery is perfectly balanced, and as a result, reciprocating forces act on the machine during operation, generating vibration. The vibration of machinery has the following essential meanings.
Sensor (Accelerometer) Detection Principle
F = m.A
Centrifugal Force and Vibration: Rotating machinery with an unbalanced mass generates centrifugal force (external force - INPUT) during rotation. This centrifugal force causes repeated deformation in the structure (structural response), which results in vibration (OUTPUT).
What is Vibration?
Units of Vibration
Amplitude represents the magnitude or intensity of vibration and can be expressed in three physical quantities: displacement, velocity, and acceleration. Common ways to express amplitude include Peak-to-Peak value (P-P value), Peak value (P value), and RMS value.
When expressed as a sine wave, the conversion relationships are as follows:
P-P Value = 2 × P Value
P Value = 1.414 × RMS Value
F = m.A
Amplitude Physical Quantity | Symbol | Unit | Amplitude Representation | Application Scope |
---|---|---|---|---|
Frequency | F | rpm, cps, Hz, rad/s | ||
Displacement | D | μm, m, mm, mil | Peak-to-Peak (P-P) Value or Peak (P) Value | Used for low-speed equipment and low-frequency vibration measurement |
Velocity | V | m/s, mm/s, kine | Root Mean Square (RMS) Value or Peak (P) Value | ISO standard, most commonly used unit |
Acceleration | a | m/s2, g, gal | Root Mean Square (RMS) Value | Used for bearings and high-frequency vibration measurement |
What is Vibration?
Three Key Elements of Vibration
Three key elements of vibration: Amplitude, Frequency, Phase
Item | Unit | Meaning | |
---|---|---|---|
Amplitude | Displacement | m, mm, µm | Magnitude of vibration |
Velocity | m/s, mm/s | Speed of vibration | |
Acceleration | m/s2, g | Rate of change in vibration speed | |
Frequency | Hz or RPM (CPM) | Number of vibrations per unit time, helps identify vibration sources | |
Phase (Phase Angle) | degree | Relative position of two vibrating bodies, can be analyzed to determine vibration patterns |
Vibration Measurement
Preventing Severe Losses with Vibration Measurement Technology
Minor vibrations can cause noise, making the environment uncomfortable for workers
and leading to measurement errors in precision instruments.
More severe vibrations can cause harm to human health and damage machinery or instruments.
Most machines, equipment, and structures experience vibration issues,
such as automobile engines, aircraft turbines, machine motors,
spindle shafts in machine tools, and building floors.
Traditionally, maintenance was performed only after problems arose,
but abnormal vibrations are often difficult to detect
while simultaneously causing wear on other components, leading to even greater losses.
By utilizing Goodtech's specialized algorithms
and integrating them with a standard database,
accumulated measurement data can be analyzed to define threshold values,
helping inspectors determine whether equipment is operating normally.
Vibration measurement technology is no longer just about detecting vibrations;
it can also be used proactively for predictive maintenance.
By using vibration measurement data to monitor machine conditions,
early repairs can be performed to prevent unexpected downtime,
thereby significantly reducing operational costs for enterprises.
Vibration Measurement
Forces Generated During Operation and Resulting Vibrations
Changes in vibration reflect changes in machine operation.
When vibration increases, it usually indicates an issue with the machine.
Vibration itself is merely a symptom of mechanical conditions,
and reducing vibration effectively means reducing the forces that cause it.
These forces may stem from mechanical issues such as imbalance or misalignment.
While vibration cannot be entirely eliminated, it can be reduced to acceptable levels.
Evaluating Rotor Health by Measuring Vibration at Non-Rotating Parts
Any machine that rotates around a central axis is considered "rotating equipment" (rotor machinery),
commonly found in factories as fans, motors, pumps, and compressors.
No rotor machinery is perfectly balanced, and as a result, reciprocating forces act upon it during operation, generating vibrations.
Furthermore, robotic arms and conveyor systems involve motor operations and screw guide movements,
where actions such as movement, rotation, reciprocation, and stopping create certain levels of vibration.
By monitoring these vibration behaviors, machine performance can be evaluated,
and variations in the manufacturing process can be assessed to ensure production quality.
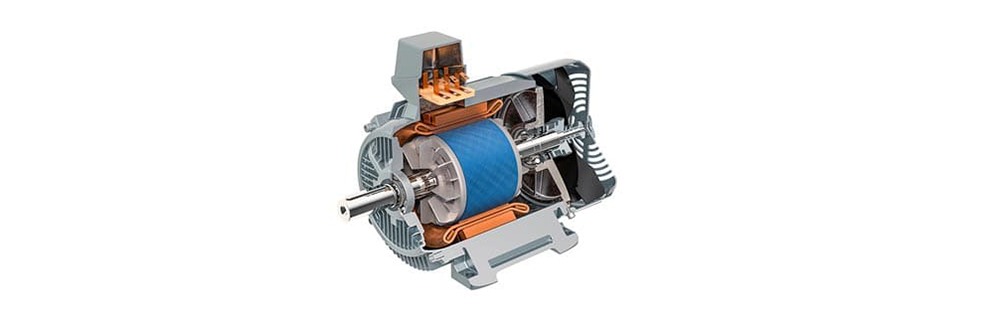