設備効率管理指標
質問集|設備効率管理指標設備管理は企業にとって非常に重要であり、各指標は工場設備のさまざまな状態を示しています。設備効率管理指標には多くの種類があり、例えば設備の健全率、総合効率、故障率、平均故障間隔時間など、異なる指標が異なる管理方向を表します。
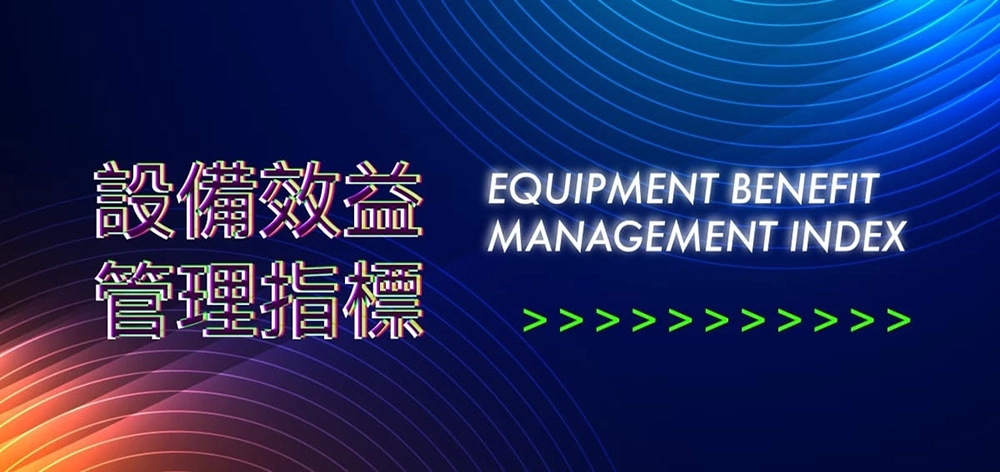
管理指標
用語の説明と計算式
設備健全率(Equipment perfectness / Availability of equipment)
または設備可用率とも呼ばれ、設備が正常に機能し、製造ラインの基準を満たしているかを示します。これは、工場設備の正常運転率を表す重要な指標であり、設備の状態と品質を反映します。
計算式:正常稼働設備数 ÷ 設備総数
設備故障率(Rate of Equipment failure)
故障率とは、エンジニアリングシステムや部品が故障する頻度を示す指標であり、通常、時間あたりの故障回数として表されます。設備の機能が低下したり、正常に動作しなくなる場合を指します。
計算式:故障発生回数 ÷ 実際の稼働設備台数
故障停止率(Equipment failure downtime)
設備の故障による停止時間が、設備が稼働すべき時間に占める割合を示します。設備が起動できず、完全に停止している状態を指します。
計算式:故障停止時間 ÷(実際の稼働時間+故障停止時間)
設備使用率(Rate of Equipment utilization)
設備の利用効率を示し、計画時間利用率(稼働時間を基準)とカレンダー時間利用率(24時間基準)の2種類があります。
計算式 1. 1時間あたりの実際の生産量 ÷ 1時間あたりの理論的生産量
計算式 2. 1シフトあたりの実際の生産数 ÷ 1シフトあたりの予定生産数
計算式 3. サンプリング時点での稼働設備台数 ÷ 設備総数
負荷時間率(Loading Time)
作業時間と実際の稼働可能時間の比率を示し、単純に時間計画の効率を表します。ダウンタイム損失を除外した指標です。
計算式:作業時間 ÷ 実際の稼働可能時間
設備総合効率(OEE,Overall Equipment Effectiveness)
設備の総合的な効率を示す指標です。例えば、時間稼働率は出勤率を、性能稼働率は勤務中の作業効率を、良品率は作業の有効性を表します。
計算式 1. 時間稼働率 × 性能稼働率 × 良品率
計算式 2. 可用率 × パフォーマンス指数 × 品質指数
計算式 3. 良品数 ÷ 計画作業時間の理論生産量
生産能力効率(Performance)
OEE 指標の一部であり、実際の生産速度と設計生産速度の比率を示します。純粋に製造速度を示す指標であり、品質は考慮しません。
計算式:標準総工数 ÷ 実際の総投入工数
良品率(Quality / Yield / FPY,First Pass Yield)
OEE 指標の一部であり、有効な良品数と実際の生産数の比率を示します。これは純利益と同等の指標となります。
計算式 1. 良品数 ÷ 実際の生産数
計算式 2. 投入数 - 不良品数 ÷ 投入数
設備総合生産力(TEEP,Total Effective Equipment Performance)
カレンダー時間(1日24時間、年間365日)を基準に測定される OEE で、設備の総生産能力(24時間基準)を示します。これは、設備のシステム管理の欠陥、上下流の影響、市場や注文の影響、設備能力の不均衡、生産ラインのスケジューリング問題などを反映する最も包括的な指標です。
計算式:負荷時間率 × OEE
平均修理時間(MTTR,Mean Time to Recovery)
平均復旧時間、平均修理時間とも呼ばれ、修理可能な対象のメンテナンス性を評価する基本指標です。
計算式:統計期間内の修理消費総時間 ÷ 修理回数
設備平均故障間隔時間(MTBF,Mean Time Between Failures)
平均無故障時間とも呼ばれ、製品の信頼性を示す指標です。単位は時間であり、製品が正常に機能し続ける時間の平均値を示します。
計算式:無故障稼働総時間 ÷ 故障回数
稼働率(Activation / Utilization rate)
生産ラインの停止時間には、バッチ切替えや工程異常、設備故障の修復時間などが含まれます。稼働率は、設備が提供可能な時間内で価値を創出するために実際に使用された時間の割合を示します。
時間稼働率:計算式 1. 実際の作業時間 ÷ 計画作業時間
計算式 2. 負荷時間 - 停止時間
計算式 3. 稼働時間 ÷ 負荷時間
性能稼働率:速度稼働率 × 実質稼働率
速度稼働率:基準サイクル時間 ÷ 実際のサイクル時間
性能稼働率:速度稼働率 × 実質稼働率
実質稼働率:計算式 1. 生産数 × 実際のサイクル時間 ÷ 稼働時間
計算式 2. 稼働時間 ÷ 実際の生産時間
導入の理由
なぜ生産ラインの設備効率を管理する必要があるのか?
工場で生産ラインの設備効率を適切に管理できていない場合、さまざまな不利な状況が発生し、生産効率、品質、および企業の経済的利益に影響を与える可能性があります。
低い生産効率:ダウンタイムの増加や設備の不安定な動作は、生産速度の低下を招き、生産量が減少します。
生産の遅延:設備の故障や適切なメンテナンスが行われないと、生産の遅延が発生し、納期や顧客満足度に影響を与えます。
品質問題:設備の不安定な運転は、不良品の増加につながり、製品の一貫性や品質に悪影響を及ぼします。
エネルギーの無駄遣い:不安定な設備は余分なエネルギーを消費し、適切な省エネ対策が取られていない場合、エネルギーコストが増加する可能性があります。
メンテナンスコスト:定期的な保守・点検が行われていないと、突発的な故障や緊急修理が増加し、生産にも悪影響を及ぼします。
人的資源の浪費:従業員が設備の故障対応、調整、緊急修理に時間を費やすことで、人材の無駄遣いにつながります。
生産コストの増加:非効率な設備管理は、生産コストを増加させ、企業の経済的利益や競争力に直接影響を及ぼします。
つまり、効果的な生産ラインの設備効率管理が実施されないと、生産や経営に関するさまざまな問題が発生する可能性があります。そのため、企業は設備効率管理を重視し、適切な技術、プロセス、管理手法を活用することで、生産ラインの安定稼働を確保し、生産効率と品質を向上させ、より良い経済的および業務上の成果を実現する必要があります。
導入のメリット
設備の効果を迅速に管理する方法
工業製造の分野では、多くの生産設備に三色灯(パトライト)が標準装備されています。これらのランプは、設備の稼働状態を示すために使用され、通常、正常稼働、停止、故障などの状態を表します。三色灯を活用して設備の効果を管理することは、直感的で効果的な方法であり、製造や生産環境においてリアルタイムで機械の動作状況を監視し、効率と生産性を向上させるのに役立ちます。
三色灯をデータ監視システムに接続することで、リアルタイムのモニタリングが可能となり、機械の稼働状態や効率指標を収集・分析できます。
設定された閾値(しきい値)に基づいて、設備の稼働効率を評価できます。例えば、機械の効率が設定基準に達すると緑のランプが点灯し、効率が著しく低下したり、故障が発生した場合は赤のランプが点灯します。ランプの色が異常を示した際には、即座に対応することが可能です。例えば、赤のランプが点灯した際には、メンテナンススタッフを派遣して点検を行ったり、停止の原因や停止時間を把握し、作業の調整やメンテナンスを行うことで、問題の悪化を防ぐことができます。
機械の稼働状態と効率指標を収集・分析
三色灯をデータ監視システムに接続し、定期的にランプの変化や機械の稼働効率のトレンドを分析 することで、データに基づいた管理を実施できます。分析結果に基づき、閾値の最適化や管理プロセスの改善を行い、機械の効果的な管理を実現します。
OEE 設備稼働率管理システム