Die Bonder Screw Abnormalities Causing Poor Product Quality?
Case|Die Bonder Screw Abnormalities Causing Poor Product Quality?If the screw quality in the Die Bonder is poor, it may cause the chip to be inaccurately positioned or bonded to the substrate, leading to misalignment or weak adhesion.
The Relationship Between Die Bonder Screws and Product Quality
In semiconductor manufacturing, the die bonder plays a role similar to decorating a cake. When making a cake, you first bake the cake base (chip), then place it on a cake plate (substrate). The die bonder acts as a tool that accurately places the chip onto the substrate. Next, layers are connected, just like adding cream and fruit to ensure a tight bond. In simple terms, the die bonder places the chip in the correct position and ensures a solid connection between the chip and the substrate, creating a complete semiconductor device.
The screws in the die bonder are used to control the movement of the robotic arm and adjust the positions of other components. They control the movement of the robotic arm in three-dimensional space to precisely position the chip from storage to bonding. These screws manage horizontal, vertical, and rotational movements with high-precision positioning systems. If the screw quality is poor, it may lead to misalignment or weak bonding. This is similar to sticking a postage stamp incorrectly due to shaky hands, resulting in an unstable product or failure.
Additionally, damaged or faulty screws may interrupt or halt the production process, significantly affecting production schedules.
Causes of Screw Damage
Possible reasons for screw damage or abnormalities include:
Wear and Tear: Long-term or improper use can lead to surface wear, especially under high loads or speeds. This can cause dimensional changes or deformation, affecting movement accuracy.
Overloading: If screws endure excessive pressure beyond their design limit, deformation or breakage may occur. This could be due to operational errors, incorrect process settings, or unexpected incidents.
Environmental Factors: Humidity, corrosive gases, extreme temperatures, etc., may lead to material degradation or surface corrosion, impacting motion characteristics and durability.
Improper Use: Mishandling or inadequate maintenance, such as incorrect parameter adjustments, excessive force application, and infrequent cleaning, can also damage screws.
Monitoring Overview
VMS-ML Machine Learning Intelligent Monitoring System
To ensure the stability of screws, the ML intelligent monitoring system can monitor precision and stability by tracking screw positioning and movements to enhance process reliability and efficiency.
Measurement Status
Screw Motion Vibration Signal Description
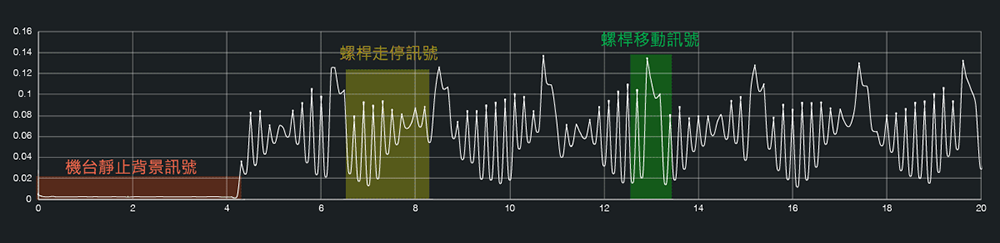
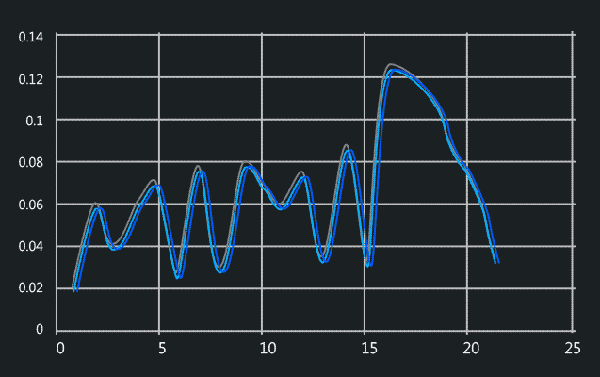
Screw Operation Before Maintenance
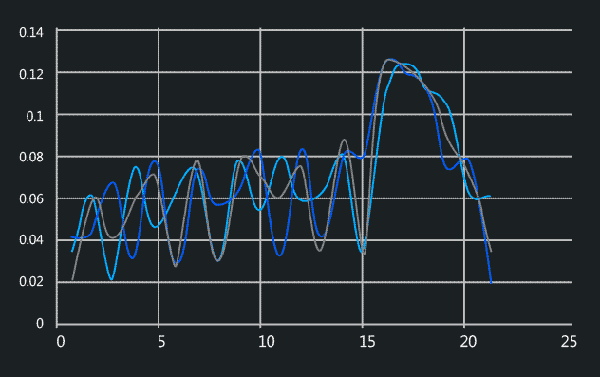
Screw Operation After Maintenance
Measurement Conclusions
The VMS-ML system can learn the correct process dynamic signals in real time, provide assessments, and compare results to evaluate equipment performance. Trend analysis helps identify potential equipment failures and predict maintenance needs, ensuring stable operations and reducing defective products.
VMS-ML Machine Learning Intelligent Monitoring System