Does the Cutting Stability of Drilling and Tapping Machines Affect Product Quality?
Case|Does the Cutting Stability of Drilling and Tapping Machines Affect Product Quality?Drilling is a cutting process. What are the main factors affecting the machining quality of drilling and tapping machines? How can we quickly troubleshoot abnormal issues?
Drilling Machine Processing Characteristics
Drilling is a cutting process that uses a drill bit to cut or enlarge a circular cross-section hole in solid materials. The drill bit is a rotary cutting tool with multiple cutting edges, which is pressed against the workpiece during drilling. The rotational speed ranges from a few hundred to thousands of RPM. The pressure and speed force the drill bit through the workpiece, leaving a circular hole, and swarf is expelled. Special drill bits can create non-circular holes, such as square holes. Source: Wikipedia
Tool Wear Leading to Poor Product Quality
Cutting tools are consumables in the process. As usage time increases, tools experience wear, leading to vibrations that affect product quality. By monitoring the spindle's continuous dynamic signals, we can analyze the relationship between the workpiece and product.
Monitoring Explanation
VMS-ML Machine Learning Intelligent Monitoring System
How the Target Machine is Monitored:
Non-invasive measurement that does not require integration with machine signals; instead, it learns from the machining dynamic signals to monitor machine conditions.
Identifying Tool Quality Through Dynamic Signals:
Signal score differences are used as a basis for determining tool replacement needs.
AI Trend Analysis for Predictive Maintenance:
By analyzing spectrum similarity and cumulative signals, tool replacement can be planned in advance to prevent defective products.
Measurement Conditions
Measurement Project Overview
# Dynamic Signal Measurement:
Using external sensors without connecting to the machine's internal signals.
# Learning Actions:
The system learns machining behavior through the intelligent monitoring system to assess machining quality.
Visualization of Drilling Behavior:
1. Spindle downforce signals indicate pneumatic cylinder conditions.
2. Dynamic signals reflecting the spindle's acceleration, drilling, and deceleration can directly reveal part relationships and machining quality.
Utilizing Machine Learning for Standardized Learning
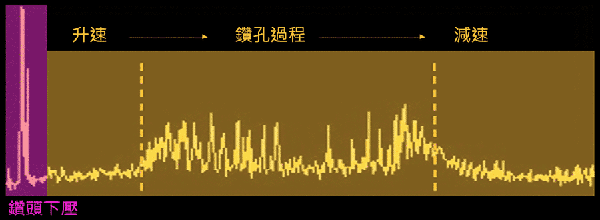
Comparing dynamic signals of different cutting tools.
New Tool Processing Signal Comparison Using Machine Learning
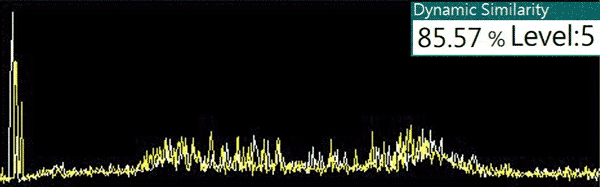
The new tool engages with the workpiece, accelerating and drilling before decelerating. Its processing behavior shows minimal deviation from the learned PATTERN.
Usable Tool Processing Signal Comparison Using Machine Learning

The usable tool, upon contact with the workpiece, starts accelerating and drilling, but vibrations begin to occur. Differences from the learned PATTERN are detected, indicating potential burr formation during drilling!
Worn Tool Processing Signal Comparison Using Machine Learning
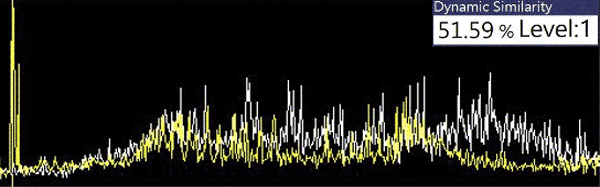
The worn tool exhibits the greatest vibration deviation during drilling, showing a significant difference from the learned PATTERN. Abnormal product processing detected!
Conclusion
Results
Benefits of AI Monitoring Management:
1. Better control over production component conditions.
2. User-defined tool replacement schedules.
3. Proactive defect prevention.
The VMS-ML Machine Learning Intelligent Monitoring System can provide early alerts of potential defects and predict the optimal time for maintenance, ensuring production stability and reducing defective products.
VMS-ML Machine Learning Monitoring System