Does Swarf Jamming Affect Swiss-Type Lathe Processing Quality?
Case|Does Swarf Jamming Affect Swiss-Type Lathe Processing Quality?Swiss-type lathes operate by rotating and moving the workpiece material via the spindle while the cutting tool remains fixed. What are the main factors affecting the processing quality of Swiss-type lathes, and how can abnormalities be quickly identified and resolved?
Swiss-Type Lathe Processing Principles
Lathe turning and milling processes are classified based on movement direction into "Sliding Head - Swiss-Type" and "Fixed Head - Traditional Lathe." Traditional lathes mostly use the fixed head method, where the spindle rotates while the cutting tool moves along the XYZ axes to process the workpiece. These lathes are mainly used for heavy cutting of large components, such as automotive wheels and automotive parts.
Swiss-type lathes, on the other hand, hold and rotate the workpiece via the spindle while the cutting tool remains fixed. This allows for higher precision and lighter cuts, making them suitable for machining components with a diameter of 35mm or smaller, such as watch components and small internal crankshaft drive shafts. This type of machining demands high precision for the linearity of the material.
Monitoring Explanation
VMS-ML Machine Learning Intelligent Monitoring System
Identifying Machine Issues Through Similarity Trend Analysis
Machine issues such as spindle instability, tool wear, aging, damage, or unexpected swarf clamping can be detected by monitoring decreasing similarity in dynamic signals, which helps identify subtle changes in the machine’s condition.
Measurement Status
Measurement Description
# Machine Learning Dynamic Signal Measurement:
Utilizing external sensors without the need to interface with machine signals.
# Learning Actions:
Using an intelligent monitoring system to learn processing behavior and understand machining quality.
Sensor Installation Location Diagram
Spindle Clamping Workpiece Condition Monitoring
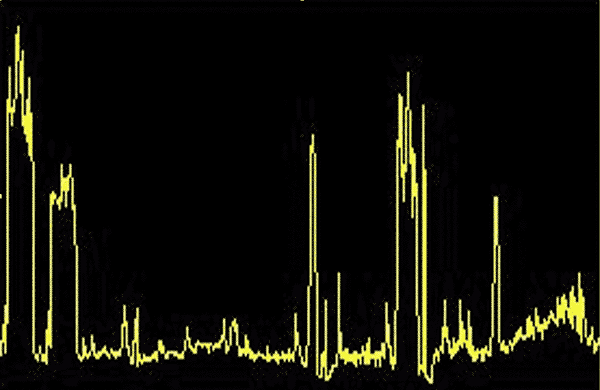
Swiss-Type Lathe Spindle Conditions
Normal Spindle Operation

Dynamic action signals and machine learning processing patterns are nearly identical, with a precision margin within 2 lines.
Spindle Clamping Anomaly

A drop in signal similarity (below 70%) results in misalignment, with precision deviation exceeding 10 lines!
Measurement Conclusion
Unexpected swarf jamming can cause machining misalignment. By utilizing the VMS-ML Machine Learning Monitoring System, changes in similarity can be used to control machining conditions, preventing prolonged unnoticed issues, reducing scrap material losses, and improving equipment utilization. Dynamic analysis using machine learning can be employed to assess spindle movement quality, tool replacement, and workpiece clamping conditions.
Only through proactive and effective machine condition management, addressing anomalies in advance (implementing predictive maintenance), can machine lifespan be extended, achieving optimal productivity while minimizing unnecessary material waste.
VMS-ML Machine Learning Monitoring System