Understanding the Operational Quality of Multi-Axis Robotic Arms Through Current Analysis?
Case|Understanding the Operational Quality of Multi-Axis Robotic Arms Through Current Analysis?Multi-axis robotic arms, with their multiple joints, require higher torque, which demands greater motor current to achieve movement.
Multi-Axis Robotic Arms
Multi-axis robotic arms are like dancers in the industrial world, capable of moving flexibly in three-dimensional space. Each joint functions like a dance step, powered by motors or servo motors, akin to a dancer's muscles. These motors work in conjunction with reducers to provide greater torque and precise motion control. By controlling the rotation of these motors, movement across different joints of the robotic arm is achieved.
There is a close relationship between the motor drive and current in multi-axis robotic arms because motors are driven by electrical current. When the robotic arm moves, each joint’s motor consumes energy to generate torque. Thus, motor current fluctuates according to the robotic arm's motion.
Specifically, when the robotic arm needs to generate greater torque, the motor requires higher current. This usually occurs when the robotic arm handles increased loads or overcomes resistance, such as lifting heavy objects or countering external forces. Conversely, when the robotic arm operates under lighter loads or remains stationary, the required motor current is lower.
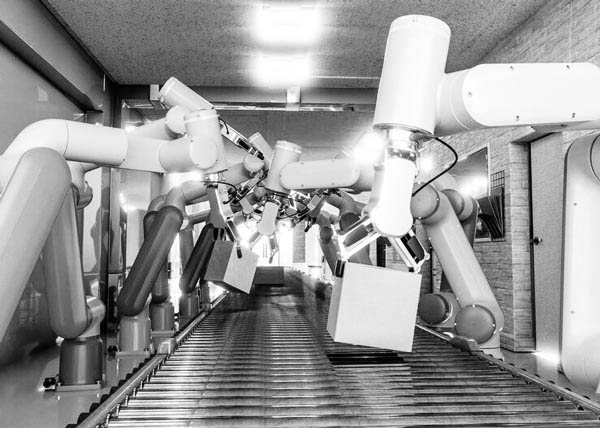
Backlash
Backlash refers to a small dead zone in mechanical systems, similar to a tiny gap between gear teeth. You can think of it as a delay phenomenon—when you start turning a gear, there might be a slight delay before it fully engages, due to the presence of backlash. In applications requiring precise control, backlash can be undesirable, but in some cases, a certain degree of backlash is necessary to ensure flexibility and prevent jamming.
The presence of backlash can result from several factors, including lubrication, manufacturing tolerances, elasticity under load, and thermal expansion caused by temperature changes. In mechanical systems, backlash may be necessary, acceptable, or something that needs to be minimized as much as possible.
Monitoring Description
VMS-ML Machine Learning Intelligent Monitoring System
The VMS-ML Machine Learning Intelligent Monitoring System is capable of learning correct operational standards and comparing them to assess operational quality. In this measurement project, we used CT sensors inside the electrical control cabinet to monitor current. Since the current changes in a multi-axis robotic arm result from the sum of all axes, the signals are blended together. Therefore, for current-based monitoring, we use single-axis or small-axis combinations as the measurement targets, and by analyzing the monitoring results, we can determine the stability of the robotic arm's operation.
Measurement Status
Standard Establishment

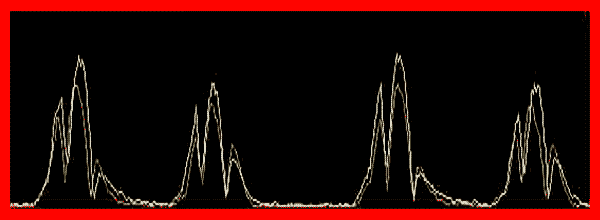
Abnormal Noise Part Comparison
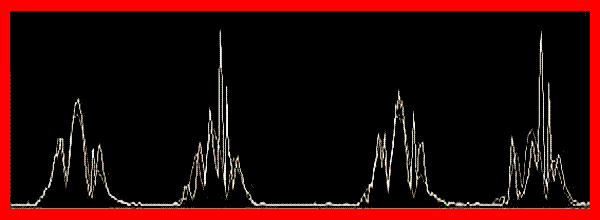
Vibration Part Comparison
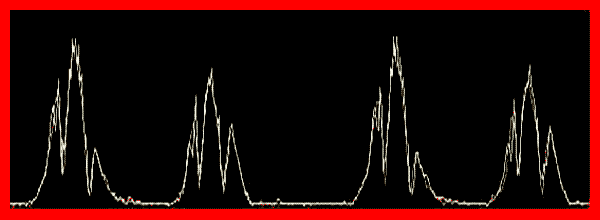
Backlash Part Comparison
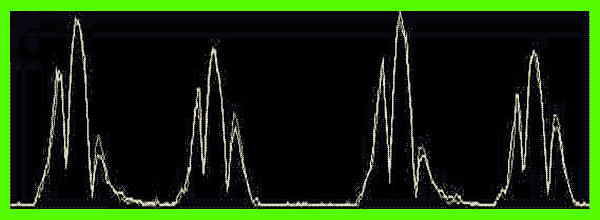
Normal (Slight Noise) Part Comparison
Measurement Conclusion
According to feedback from the sensors, system signal comparisons allow us to determine that the motor's current state significantly impacts the robotic arm's operational quality. A stable motor current ensures precise motion control, allowing the robotic arm to operate steadily under various working conditions while minimizing energy consumption and motor wear.
VMS-ML Machine Learning Intelligent Monitoring System