Does Excessive Particle Concentration Affect Wafer Quality?
Case | Does Excessive Particle Concentration Affect Wafer Quality?In semiconductor manufacturing processes, excessive particle concentration can cause process instability, leading to uneven material removal or deposition. How can such issues be mitigated?
Impact of Excessive Particle Concentration
Causes of Particle Formation:
In semiconductor processes, particles refer to tiny solid or liquid particles, usually in the micrometer or nanometer scale.
Excessive particle concentration can lead to process instability in etching, deposition, or photomask processes.
This may result in uneven material removal or deposition, affecting component quality, increasing defects, and raising the likelihood of production failures.
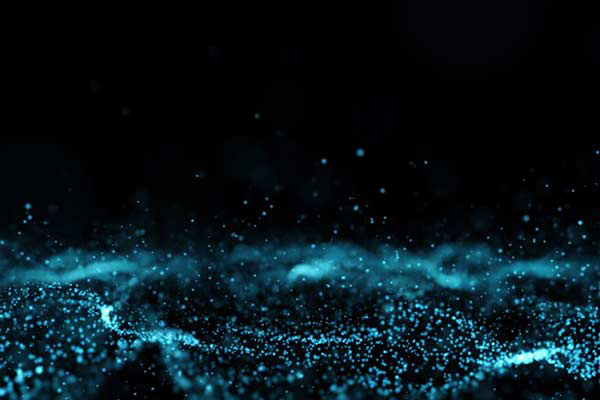
Causes of Particle Formation:
The sources of particle formation are diverse and can originate from both internal and external environments.
Internal sources include component wear within the equipment, such as transport systems, bearings, and seals.
Long-term operation and usage of equipment can result in the release of tiny particles.
During processing, chemical reactions may break down materials or generate by-products in the form of particles.
For instance, certain chemical processes may produce fine solid residues as a result of gas or liquid reactions.
External environmental factors such as airborne dust and humidity changes can influence particle levels within the equipment.
This underscores the importance of cleanroom environment control in semiconductor processes.
Operators' clothing, shoes, and tools can also introduce particles, making stringent cleanroom protocols essential.
In addition, machine design can contribute to particle generation.
Friction during operation may release particles, and the quality of process materials can also be a factor.
Low-quality raw materials might contain impurities, which could lead to particle generation during the manufacturing process.
How to Reduce Particle Formation:
To minimize particle generation within equipment, users should perform regular maintenance and cleaning, use high-quality materials,
and implement strict cleanroom standards and operating procedures.
Periodic measurement of cleanroom particle concentration helps detect increases early and allows timely corrective actions.
Protective measures such as equipment covers and dust shields should be employed to prevent particle entry or dispersion in critical areas.
Monitoring Overview
IIoT Unlimited: Industrial IoT
The wireless industrial IoT particle monitoring system covers particle sizes ranging from 0.3 microns (µm) to 10 microns (µm).
It transmits wireless signals below the 1GHz frequency band, which does not interfere with in-plant wireless systems and provides excellent low-frequency penetration capabilities.
The system does not require extensive wiring, significantly reducing installation and monitoring costs.
The main system can support up to 300 monitoring points, ensuring cost-effectiveness and reducing the need for manual inspections.
It provides real-time monitoring of particle concentration and instant alerts when thresholds are exceeded.
Measurement Status

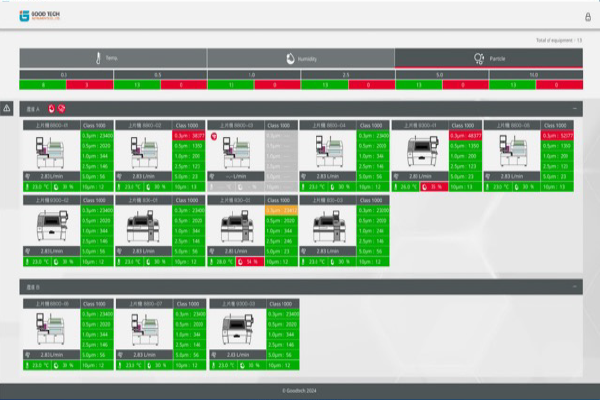
Main Monitoring Interface
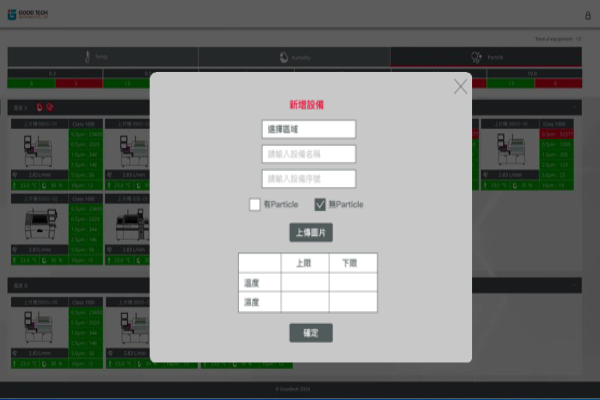
Set Threshold for Excessive Particle Concentration
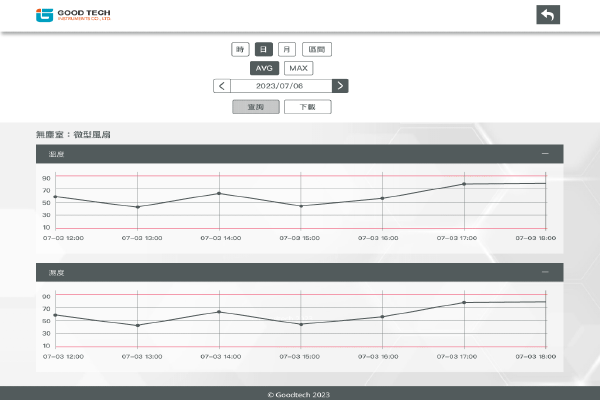
Long-Term Particle Monitoring Trend
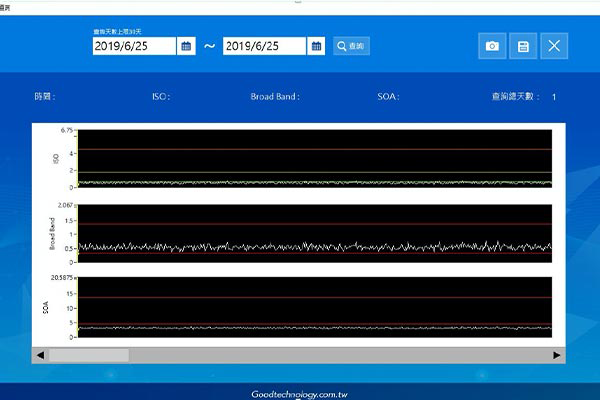
Query Periodic Changes in Single Sensor Particle Concentration
Measurement Conclusion
The Particles-IoT system for industrial particle monitoring can simultaneously track particles of different sizes.
Each sensor can be customized with alert thresholds based on area-specific requirements.
When the threshold is exceeded, alerts are issued to notify users for corrective actions.
Users can analyze trend changes to design preventive measures and trace pollution sources through the distribution of particle sensors.
Tracking periodic changes helps identify whether product anomalies are caused by particle contamination and pinpoint the exact time of abnormal particle concentrations,
thereby establishing a robust defense mechanism.