How to Monitor and Measure Equipment Status in the PVD Process?
Case|How to Monitor and Measure Equipment Status in the PVD Process?PVD, or Physical Vapor Deposition, is a coating technology used in industrial manufacturing. Establishing an optimal process environment is essential to effectively improve production yield. How can the equipment status in the PVD process be monitored and measured?
Physical Vapor Deposition (PVD)
PVD, or Physical Vapor Deposition, is a coating technology used in industrial manufacturing.
It primarily utilizes physical methods to heat or excite materials to deposit thin films through phase transition phenomena.
In semiconductor processes, it falls under surface treatment processes and is typically carried out in a vacuum environment.
For example, the evaporation source transitions from solid to gas, then condenses onto the wafer surface.
PVD methods are categorized into Evaporative PVD, Sputtering PVD, and Ion Plating (PAPVD).
The production processes for display panels and touch panels also widely employ PVD coating methods.
Since PVD thin film deposition requires a perfect vacuum environment,
detailed inspection and monitoring of various equipment components are crucial.
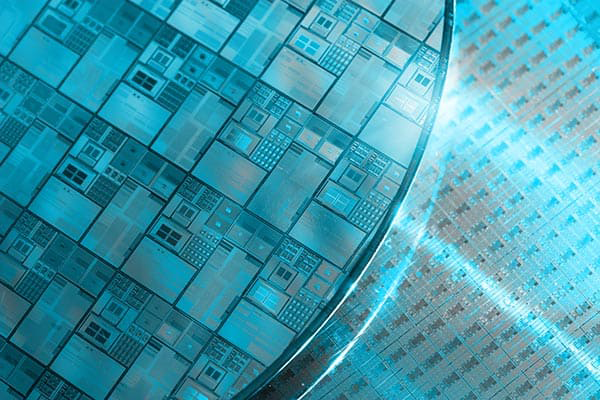
Solutions and Monitoring Explanation
VMS-PH Portable Measurement Analyzer
Creating an optimal process environment is essential to improve production yield.
So how can the equipment status in the PVD process be monitored and measured?
By measuring components such as magnetic seals, reducers, vacuum chambers, and motors within the PVD process,
we can compare results to better understand the equipment status.
The measured values are directly converted into intuitive graphical representations,
uncovering hidden process insights that can be used as a basis for future online monitoring.
Regular equipment inspections and predictive maintenance help prevent unexpected downtime or anomalies in the process.
Measurement Conditions
PVD Magnetic Oil Seal Measurement
The magnetic oil seal consists of a combination of a stationary ring and a rotating ring, utilizing magnetic force technology and mechanical seal concepts with a fully floating sealing surface structure.
Dynamic Analysis Comparison of Forward and Reverse Rotation for PVD Magnetic Oil Seal Equipment A/B/C
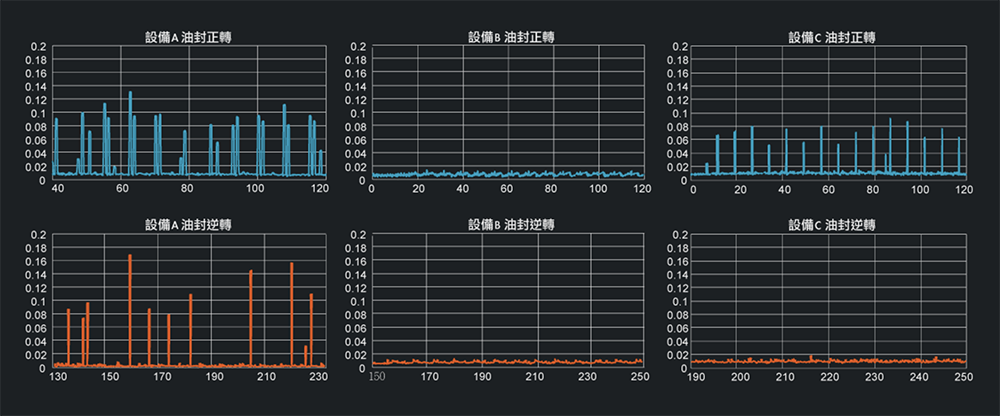
Magnetic oil seal equipment B/C driven by the same motor shows higher vibration levels in forward rotation for equipment C.
Equipment A exhibits vibration and wear signals in both forward and reverse rotations and requires further observation.
Common causes of oil leakage anomalies:
Defective Oil Seal: Poor manufacturing quality, cracks, or loose springs. Maintenance actions: Replace the oil seal or adjust the spring tension.
Poor Installation: Severe operational wear, lack of shine, or dust accumulation. Maintenance actions: Replace the oil seal, lubricate, and clean.
PVD Gear Reducer Measurement
The gear reducer is a critical drive component in equipment, composed of gears, transmission parts, bearings, shafts, housings, and other accessories.
Dynamic Analysis Comparison of Forward and Reverse Rotation for Gear Reducer Equipment A/B/C
Idle Operation State
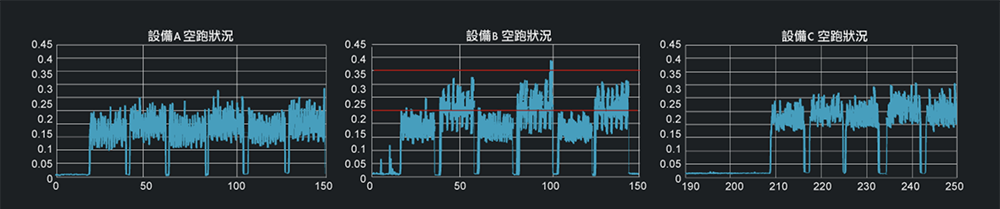
Process Operation State
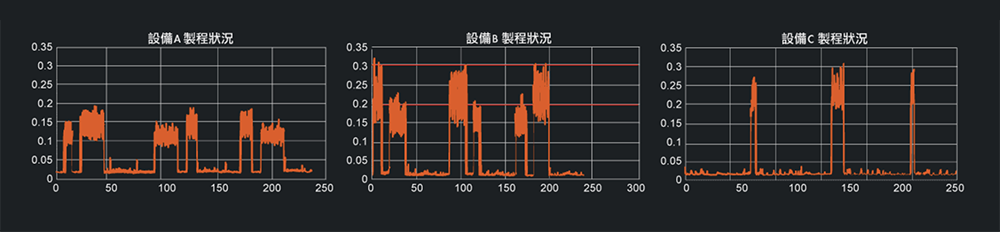
Significant differences in forward and reverse rotation for equipment B require further monitoring.
PVD Vacuum Chamber Measurement
The vacuum chamber, used in PVD processes, maintains a vacuum state via a vacuum pump for physical experiments or coating applications.
Sensors placed at the bottom of Chamber 4, measuring points A and B for comparison
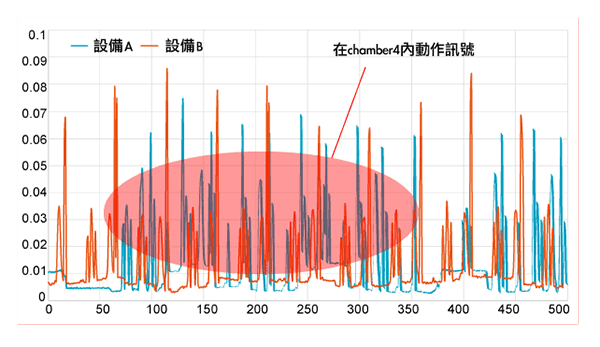
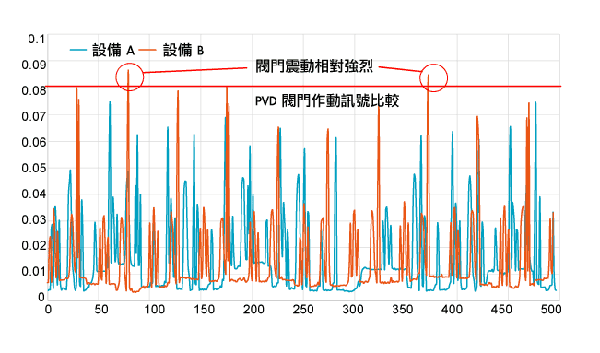
Equipment A shows more irregular dynamic signals compared to equipment B.
→ The recorded signals confirm that internal mechanical issues in equipment A are causing abnormal vibrations.
Equipment B exhibits greater vibration due to PVD valve operations compared to equipment A.
→ Despite the regular pattern in equipment B, the valve operations generate more vibration than equipment A, suggesting long-term monitoring is necessary.
OIL PUMP Measurement
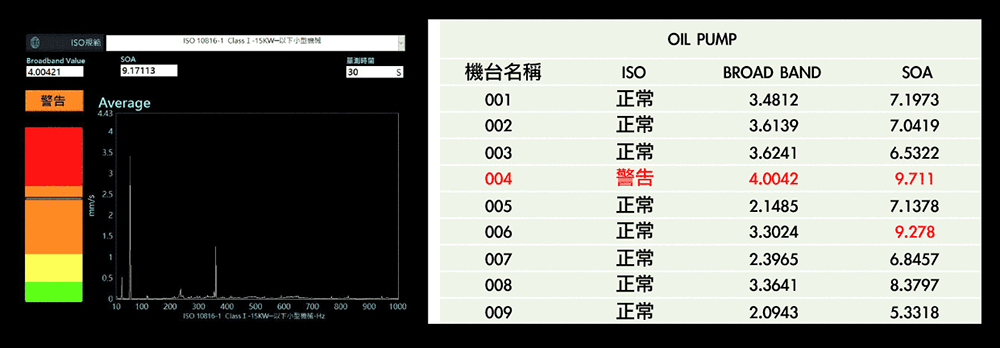
Measurement Conclusion
To create an optimal process environment and effectively improve production yield, it is crucial to monitor equipment status. The VMS-PH Portable Measurement Analyzer enables rapid detection of various equipment issues, and its collected anomaly data can serve as a reference for future online monitoring.
VMS-PH Portable Measurement Analyzer