Abnormalities in Stamping Dies Causing Mass Defects?
Case | Abnormalities in Stamping Dies Causing Mass Defects?High-speed stamping machines produce a large number of products in a short time. If die wear or abnormalities occur, it can result in a massive number of defective products.
High-Speed Stamping Machines
High-speed stamping machines are mechanical devices used in metal processing, mainly for rapidly stamping sheet metal to manufacture various parts and products. Stamping is a metal forming manufacturing process that typically uses presses or stamping machines to place metal sheets or strips between dies, applying strong pressure to cause plastic deformation in the material, ultimately forming the desired shape or structure.
This process can be used to produce a wide range of metal components and products, from simple flat plates to complex three-dimensional shapes. These machines are widely used in the manufacturing industry, especially in automotive production, electronics, and other metal processing fields. They feature high-speed impact and rapid reset capabilities, enabling efficient production rates, large-scale mass production, and short-cycle manufacturing.
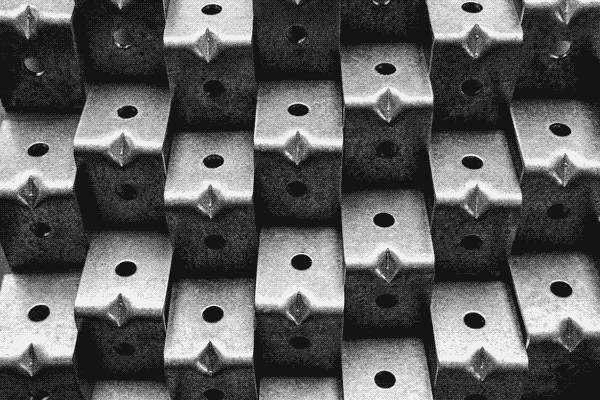
The Relationship Between Stamping Machines and Dies
Different products require different dies. For instance, consumer goods with lower prices often use cheaper dies. Dies are consumables that inevitably wear out during the stamping process. Over time, this wear leads to die failure.
Die failure in stamping machines can impact the manufacturing process and product quality in multiple ways, affecting production efficiency, precision, and consistency. When a die is damaged, the manufacturing process is interrupted, requiring downtime for repair or replacement, which negatively impacts production schedules and reduces efficiency. Additionally, replacing damaged dies requires recalibration and testing, increasing production time and costs. Prolonged downtime can severely disrupt the entire manufacturing workflow. Damaged dies may also pose safety risks, such as sudden breakage or loss of control, potentially endangering operators and the surrounding environment.
A damaged die can affect an entire batch of products, leading to inconsistencies in appearance or dimensions. Common defects include misalignment, cracks, sharp edges, or incorrect shapes. Defective batches may require rework or additional inspections, significantly increasing production costs.
Therefore, to ensure efficient and stable production while facilitating timely repairs or replacements, a monitoring system capable of providing early warnings about die conditions is essential. Such a system enables proactive die replacements or adjustments, reducing the risk of failure and preventing the mass production of defective products.
Monitoring Explanation
VMS-ML Machine Learning Intelligent Monitoring System
Using a non-intrusive measurement method, the system does not require integration with machine signals, eliminating the need for a complex pre-setup process.
It is ready for use upon installation. By learning the correct dynamic processing signals, the system determines when a die needs replacement. During the stamping process, it monitors die quality in real-time, enabling early replacement or adjustment to prevent the production of a large number of defective products.
Measurement Status
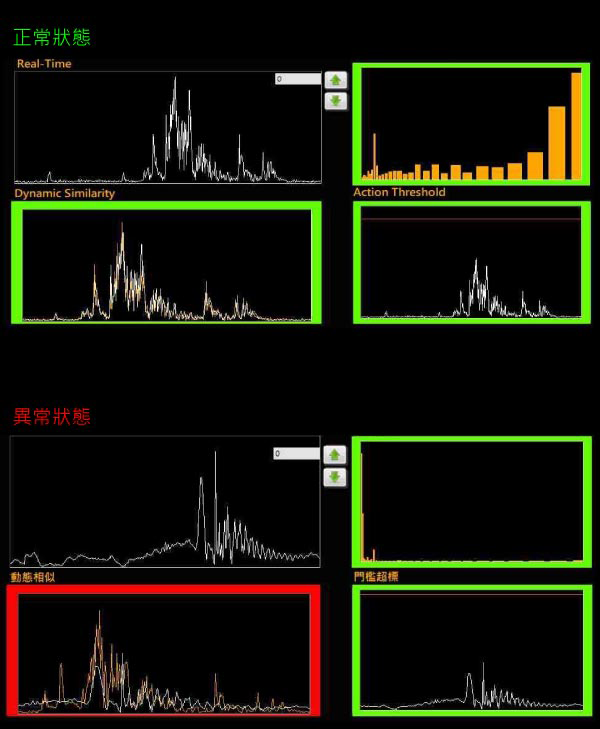
Dynamic Signal Measurement Status of Stamping Machine
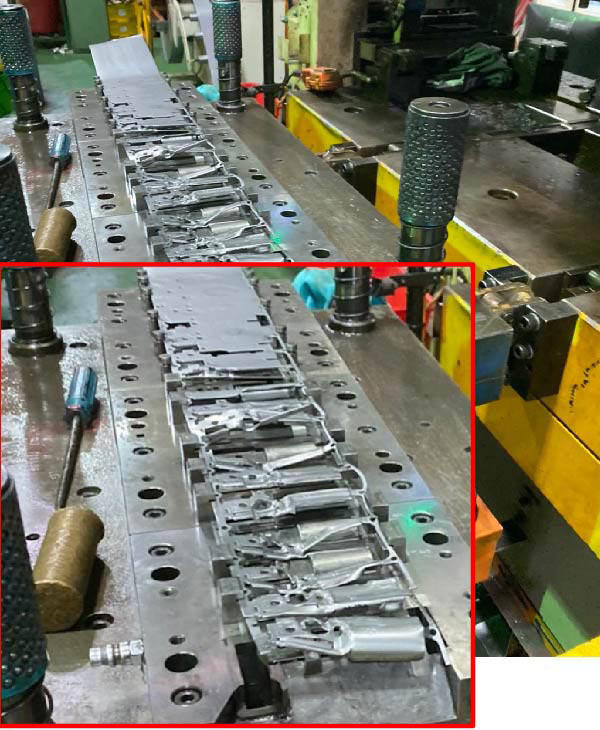
Result: Workpiece Jam, Machine Shutdown Required for Die Repair
Result Verification

Die Condition Two Hours Before Failure
Measurement Conclusion
The VMS-ML system can learn the correct dynamic signals during the stamping process, providing real-time assessments and results. From the above data, it is evident that the system issued an alert two hours before die failure, indicating die deterioration or abnormalities. If the machine had been temporarily stopped for die adjustment or replacement at the time of the alert, it would have prevented workpiece jamming, machine downtime for die repair, and defective product production.
The VMS-ML Machine Learning Intelligent Monitoring System also provides trend graphs to predict potential die failures, allowing users to perform predictive maintenance in real-time. This helps maintain optimal die performance on the production line and prevents large-scale defective product generation.
VMS-ML Machine Learning Monitoring System