How to Measure Stocker (STK) Storage Equipment?
Case | How to Measure Stocker (STK) Storage Equipment?In the era of Industry 4.0, many automated devices replace manual labor, accelerating processes and simplifying heavy workloads and complex procedures. Stocker storage equipment has taken over critical material transportation tasks. How can measurements be performed to ensure stability during the transportation process?
Stocker Features
In the era of Industry 4.0, automation has increasingly replaced manual labor, enhancing efficiency and simplifying complex workflows.
With the advancements in semiconductor and digital technology, silicon wafers are becoming larger for economic benefits, making transportation more challenging.
To address this, automated transportation systems have been implemented within factories, such as the AMHS (Automatic Material Handling System), OHT overhead transportation system,
and Stocker storage equipment. These systems reduce operator workload and prevent human errors or accidents. Stockers come in different types and operational models depending on factory needs,
including ZIP Stocker, Foup Stocker, Tower Stocker, and Linear Stocker. Most of these designs follow a modular architecture to maximize space efficiency and optimize usage.
Solutions and Monitoring Overview
VMS-ML Machine Learning Intelligent Monitoring System
Stockers are responsible for storing glass substrates in panel factories and storing semi-finished or finished semiconductor products in semiconductor plants.
Gude Technology focuses on monitoring and diagnosing the movement behaviors of Crane STK when handling cassettes and assessing the quality of brake servo motors.
By utilizing the OLVMS-ML machine learning intelligent monitoring system to learn correct movement behaviors as a benchmark, each action is monitored and diagnosed.
The system identifies abnormal or unstable actions in the equipment, enabling predictive maintenance and preventing unexpected failures.
Measurement Status
Crane STK Cassette Handling Process
Learning the sequential movements of the Crane STK Cassette handling process:
Take: Crane picks up the cassette
Put: Crane places the cassette
Go: Crane moves to the innermost position
Come: Crane returns to the starting position
Establishing a management pattern for Take, Put, Go, and Come actions.
Crane STK Cassette Handling Action Recognition
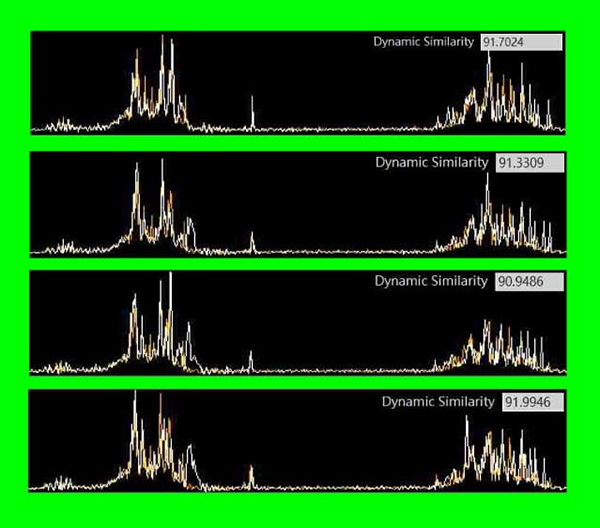
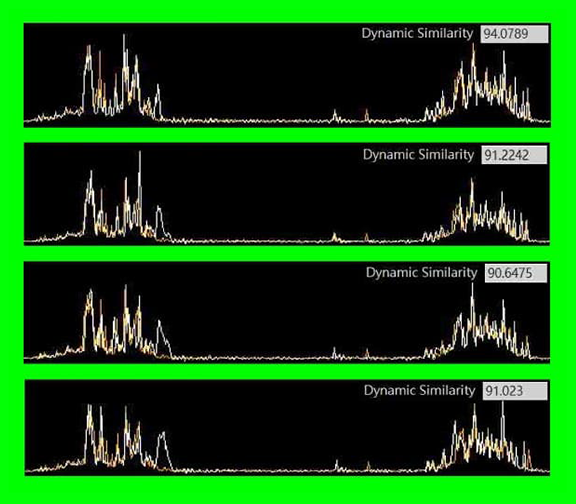
Yellow line: Machine learning movement standard, White line: Real-time signal
The system automatically tracks arm movements, managing both pick and place actions without misidentification.
Normal machine operation average dynamic similarity: Put - 91%, Take - 92%
When the arm operates normally, the machine learning motion (yellow line) aligns with the real-time signal (white line).
Crane STK Empty Run Movement (Without Cassette)
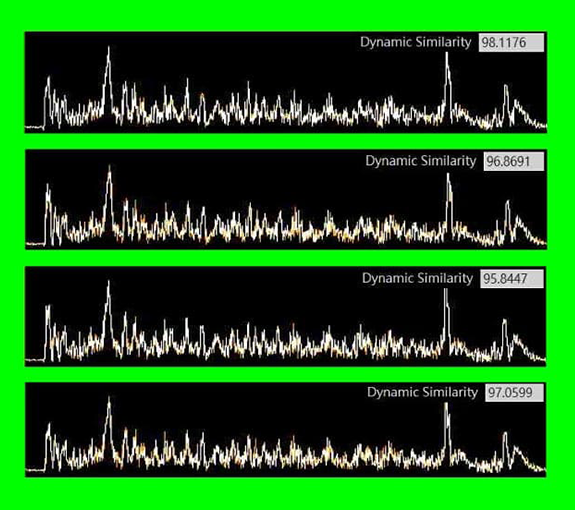
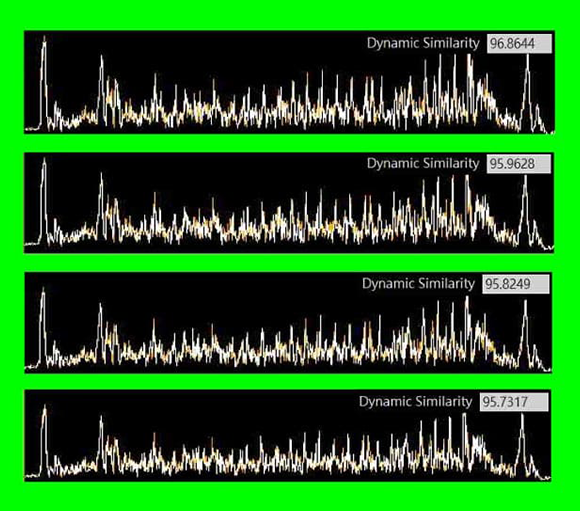
Yellow line: Machine learning movement standard, White line: Real-time signal
High stability in dynamic similarity scores during empty runs!
Crane STK Loaded vs. Unloaded Movement Comparison
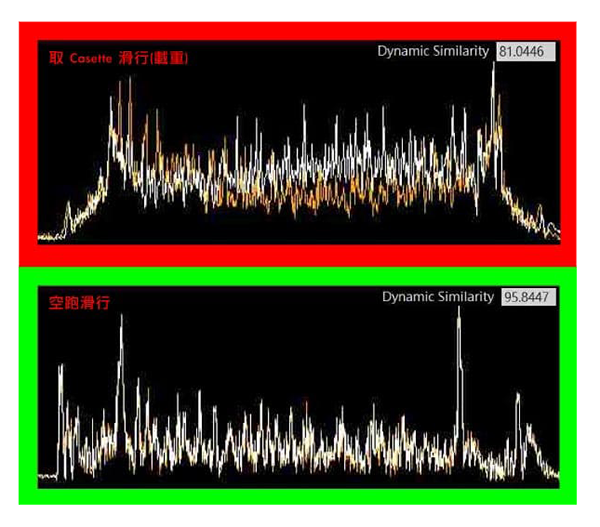
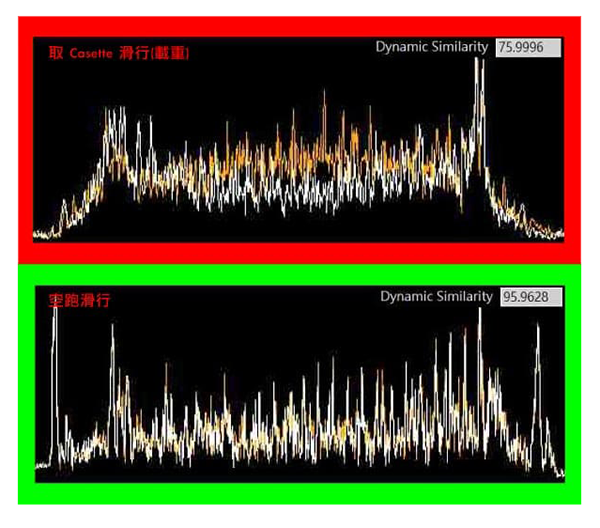
Yellow line: Machine learning movement standard, White line: Real-time signal
Inconsistent motion after loading causes a drop in dynamic similarity scores!
When the arm operates under load, the machine learning motion and real-time signal become misaligned.
Crane Empty Run Motor Timing Vibration Comparison
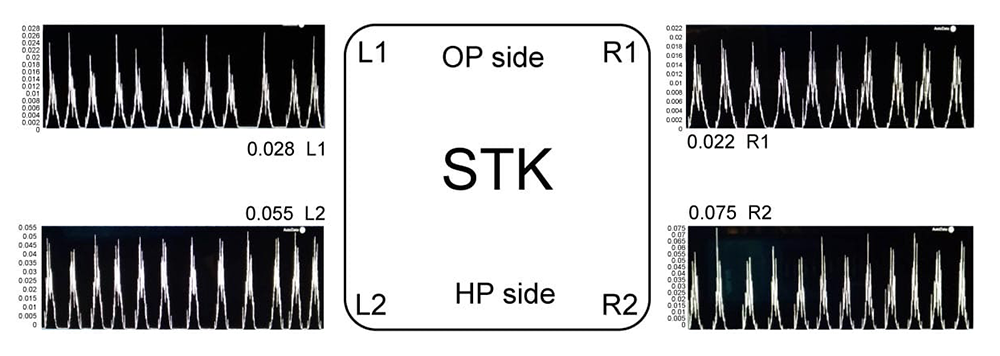
Motor Operation Visualization
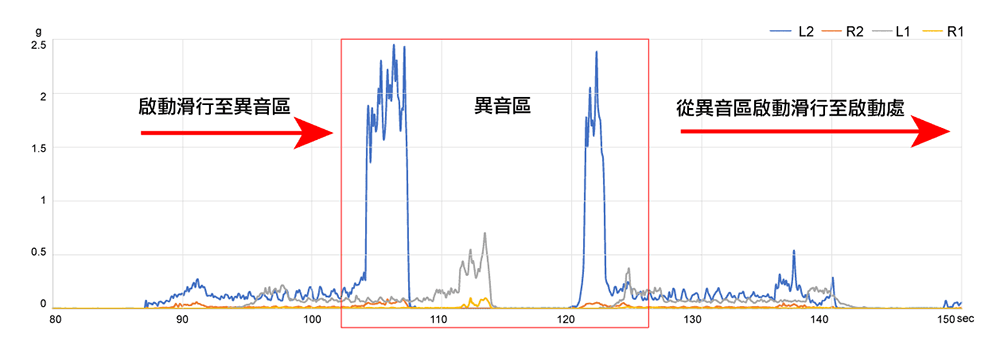
Crane STK Load Motor L1 and L2 Machine Learning Comparison
Crane STK Load Motor L1
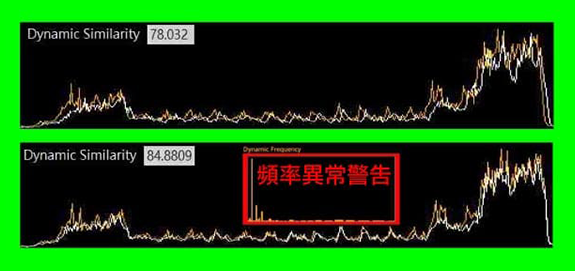
Crane STK Load Motor L2
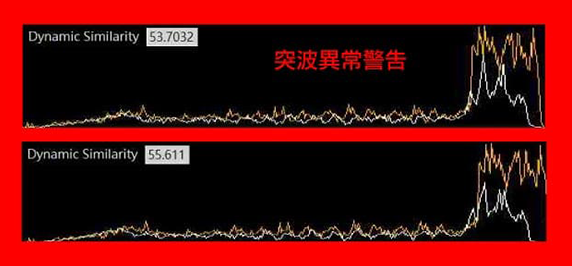
Measurement Conclusion
Using the in-factory OLVMS-ML monitoring system, it was found that STK L2 exhibits sudden surges,
with a significant deviation in similarity scores when compared to a healthy motor pattern.
L1 is affected by L2, showing fluctuations and abnormal frequency. R2 is slightly impacted by L2,
showing minor fluctuations compared to R1. Only R1, which is furthest from L2, remains relatively stable.
The VMS-ML Machine Learning Intelligent Monitoring System can analyze the movement conditions of each axis with a single sensor, then use the VMS-PH Dynamic Analyzer to identify the root cause of anomalies.
VMS-ML Machine Learning Monitoring System