How to Prevent Wafer Scratching During Transport?
Case | How to Prevent Wafer Scratching During Transport?The wafer handling robotic arm (Wafer Robot) may cause wafer scratching or collisions if abnormal vibrations occur during transport. How can we proactively prevent and avoid wafer damage and scrapping?
Robotic Arm for Wafer Handling
Wafer handling robotic arms are widely used in the front-end semiconductor manufacturing process, replacing manual labor in wafer transportation.
Given the high cost of wafers, users place great importance on the stability of robotic arms during transportation.
Most wafer handling arms are designed with multi-axis joints, allowing precise and stable movement in confined spaces.
If abnormal vibrations occur during wafer transport, they can significantly impact wafer quality, leading to scratching or collisions.
Since wafer handling arms operate in multiple axes and directions, how can their movements be effectively monitored?
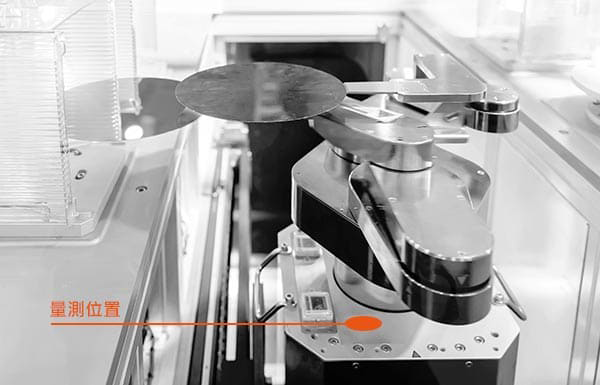
Solution and Monitoring Explanation
VMS-ML Machine Learning Intelligent Monitoring System
Using the VMS-ML machine learning intelligent monitoring system, we analyze the dynamic signals of wafer transport.
This system does not require integration with the equipment’s control system—only a single sensor installation is needed to begin learning movement signals.
Through real-time measurements, it detects variations across different movement phases.
Measurement Status
Wafer Robot Arm Motion Visualization and Monitoring
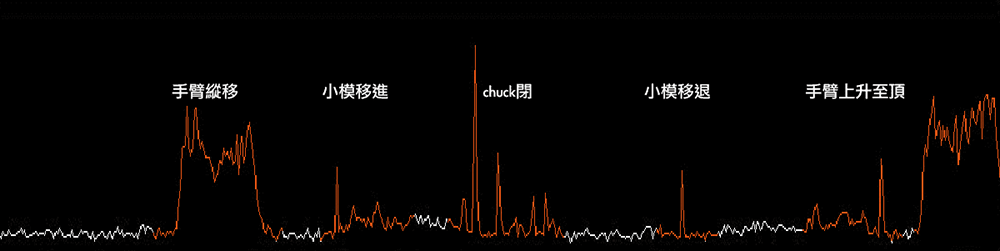
Machine Learning Monitoring Measurement Display
Monitoring Status: Normal Pass
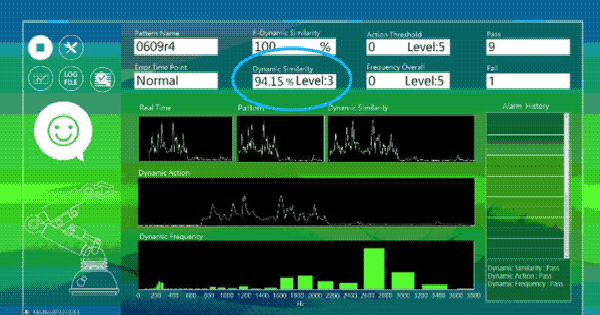
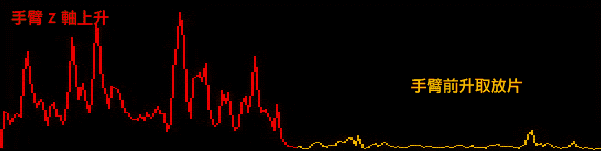
Arm motion is stable, with monitored movements closely matching expected behavior.
Similarity Score: 94%
Monitoring Status: Abnormal Alarm Fail
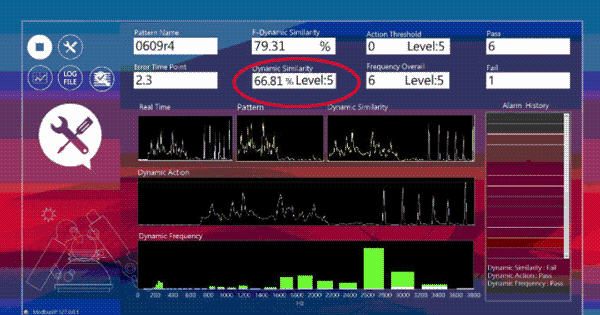
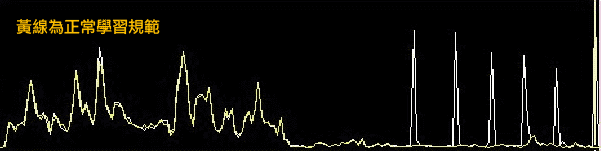
Simulated abnormal scenario - slight knock on the fork. Dynamic signal and frequency domain changes cause a decrease in similarity score.
Similarity Score: 66%
Measurement Conclusion
Using the VMS-ML Machine Learning Intelligent Monitoring System, the correct motion behaviors are learned as benchmarks for monitoring and diagnosis. The system detects anomalies or instability in the robotic arm’s movements in real-time, enabling predictive maintenance and preventing unexpected failures.
Benefits of using VMS-ML for robotic arm health monitoring: Preventing wafer damage due to abnormal arm movements, monitoring the wafer transfer process, and detecting issues such as wafer scratching and misalignment. By collecting historical health trends, it serves as a data-driven reference for maintenance planning. It can also be used for stability testing before and after repairs to ensure maintenance quality and effectiveness.
VMS-ML Machine Learning Intelligent Monitoring System