Equipment Efficiency Management Metrics
FAQ | Equipment Efficiency Management Metrics#OEE
#PDM
Equipment management has a significant impact on enterprises, with various metrics representing the status of factory equipment. Equipment efficiency management includes many key indicators, such as availability, overall efficiency, failure rate, and mean time between failures (MTBF). Different metrics reflect different management focuses.
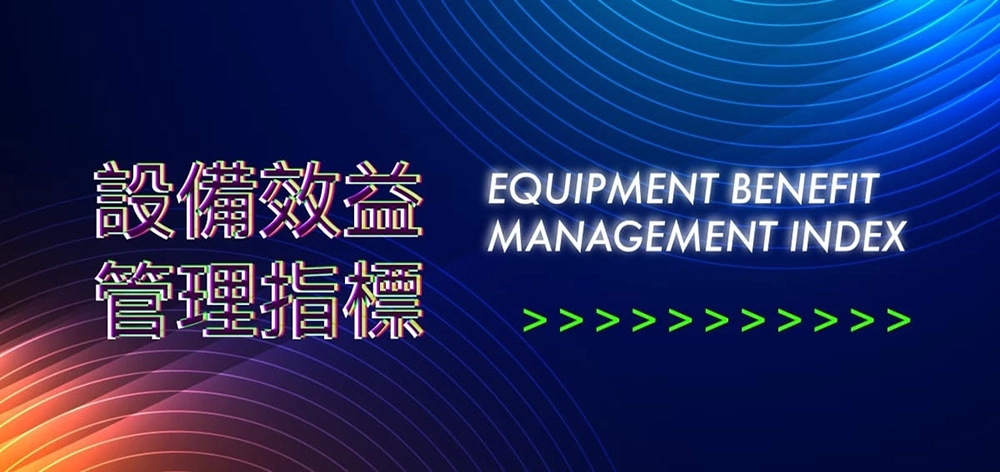
Management Metrics
Terminology and Formulas
Equipment Availability (Equipment Perfectness / Availability of Equipment)
Also known as equipment uptime, this metric measures whether equipment meets manufacturing standards and operates normally.
It is an important indicator of equipment health and factory efficiency.
Formula: Number of Available Machines ÷ Total Number of Machines
Equipment Failure Rate
Also known as the failure rate, this measures how frequently an engineering system or component fails, typically expressed in failures per hour.
It reflects the loss or reduction of equipment functionality, leading to operational downtime.
Formula: Number of Failures ÷ Number of Active Machines
Failure Downtime Rate
Measures the proportion of time a machine is down due to failure compared to the total available operating time.
Formula: Failure Downtime ÷ (Total Operating Time + Failure Downtime)
Equipment Utilization Rate
Also known as utilization efficiency, this can be measured based on scheduled work hours or total available time (calendar time).
Formula 1: Actual Output per Hour ÷ Theoretical Output per Hour
Formula 2: Actual Output per Shift ÷ Expected Output per Shift
Formula 3: Number of Running Machines at a Given Time ÷ Total Number of Machines
Why Implement Equipment Efficiency Management?
If a factory does not effectively manage equipment efficiency, it can lead to various negative outcomes,
impacting production efficiency, product quality, and overall business profitability.
Low Production Efficiency: Increased downtime and unstable machine operation slow down production, reducing output.
Production Delays: Equipment failures or maintenance issues that are not addressed in time can cause delays, affecting delivery schedules and customer satisfaction.
Quality Issues: Unstable operations can lead to inconsistent product quality and higher defect rates.
Energy Waste: Poorly maintained machines may consume excessive energy, increasing operational costs.
High Maintenance Costs: Lack of regular maintenance can lead to unexpected breakdowns and expensive emergency repairs.
Inefficient Use of Manpower: Employees may spend excessive time troubleshooting and repairing machines instead of focusing on productive tasks.
Increased Production Costs: Inefficient equipment management leads to higher production costs, reducing profitability and competitiveness.
In summary, failing to implement effective equipment efficiency management can result in operational and financial challenges.
Companies should adopt appropriate technologies, processes, and management strategies to ensure smooth production, improve efficiency,
and achieve better business outcomes.
Implementation Benefits
How to Efficiently Manage Equipment Performance
In the field of industrial manufacturing, many production machines are equipped with three-color indicator lights as standard.
These lights indicate the operational status of the equipment, such as normal operation, downtime, or failure.
Utilizing these indicator lights to manage equipment performance is an intuitive and effective method that helps monitor
machine operations in real-time, thereby improving efficiency and productivity.
Connecting three-color lights to a data monitoring system enables real-time monitoring,
allowing the collection and analysis of machine operational status and performance indicators.
By setting predefined thresholds, the system can assess equipment efficiency. For example, when machine efficiency reaches
or exceeds the set standard, a green light is displayed; when efficiency drops significantly or a failure occurs, a red light is shown.
If an abnormal status is detected, immediate action can be taken. For instance, when the red light turns on,
maintenance personnel can be dispatched for inspection, downtime reasons can be analyzed, and adjustments can be made
to prevent further deterioration.
Collect and Analyze Machine Operational Status and Performance Indicators
By integrating three-color lights with a data monitoring system, regular analysis of light signal variations and machine efficiency trends can be conducted. Based on the analyzed data, threshold settings and management processes can be optimized continuously, improving the efficiency and effectiveness of equipment performance management.
OEE Equipment Utilization Management System