How to Implement Industry 4.0?
FAQ | How to Implement Industry 4.0?Industry 4.0 represents the vision of the fourth industrial revolution in human history. The key to factory optimization strategies lies in intelligent processes. These smart processes are achieved through the full automation (unmanned operations) of machinery, integration with various databases, and the use of algorithms. Gude Technology plays a crucial role in helping industries transition to intelligent processes.
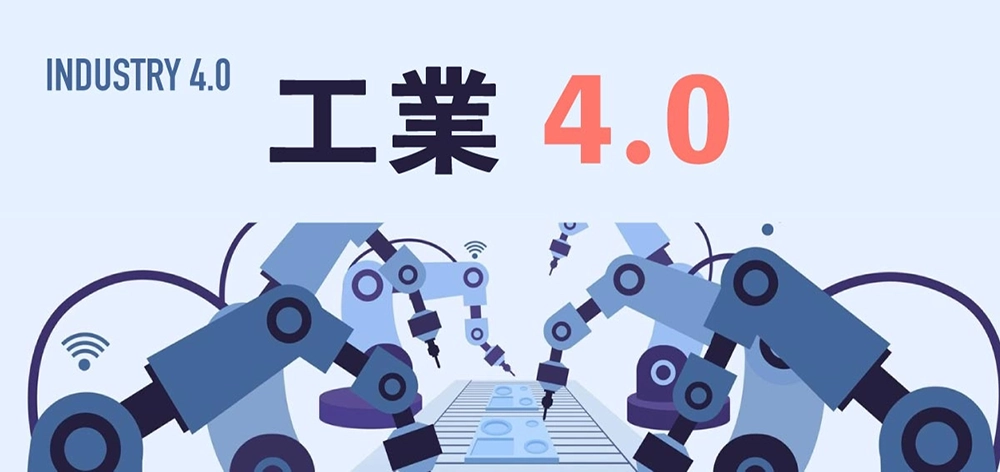
Definition & Background
What is Industry 4.0?
Precision Machinery Combined with Smart Technology
Industry 4.0 is a concept of digital transformation in manufacturing and related industries. Originating in Germany, it was first introduced at the Hannover Messe in 2011. It is regarded as the fourth industrial revolution, aiming to upgrade traditional industries into smart, digitalized, and highly automated manufacturing models through the integration of IoT, Artificial Intelligence (AI), Big Data Analytics, Cloud Computing, and Automation Technologies. By merging the physical and digital worlds, Industry 4.0 enables intelligent manufacturing and full-process integration of supply chains.
Core Technologies of Industry 4.0
1. Internet of Things (IoT): Connects devices, sensors, and systems to form an intelligent network capable of automatically transmitting and exchanging data.
2. Big Data & Analytics: Collects and analyzes large amounts of production data, providing real-time insights to optimize decision-making and efficiency.
3. Artificial Intelligence (AI) & Machine Learning: Enables automated diagnostics, predictions, and decision-making, such as predictive maintenance and production process optimization.
4. Cloud & Edge Computing: Cloud computing offers vast data storage and processing capabilities, while edge computing allows real-time data processing at the local level.
5. Digital Twin: Creates a virtual model of equipment or products to simulate actual operating conditions for testing, monitoring, and optimization.
6. Collaborative Robots: Robots that work alongside humans, providing flexibility in various production demands.
7. Additive Manufacturing: Supports customization and rapid prototyping, reducing production costs and material waste.
Key Applications of Industry 4.0
1. Smart Manufacturing: Integrates automation and data to achieve high-performance, cost-effective production while supporting diverse, small-batch customization.
2. Smart Factories: Uses networked technology and automation to create highly efficient production environments, reducing labor dependency and increasing flexibility.
3. Supply Chain 4.0: Enables real-time monitoring and data sharing for a fully transparent and intelligent supply chain from raw materials to product delivery.
4. Predictive Maintenance: Uses IoT and data analytics to conduct maintenance before equipment failure occurs, reducing downtime and repair costs.
5. Customized Production: Allows flexible production models that quickly respond to market demand, supporting large-scale customization.
Implementation
How to Implement Industry 4.0?
How Does Gude Assist in Industrial Smart Processes?
Industry 4.0 is the vision of the fourth industrial revolution. The key to factory optimization strategies lies in intelligent processes, achieved through unmanned automation, database integration, and algorithmic applications. Gude plays a crucial role in enabling industrial smart processes.
In 2017, global economic conditions stabilized, leading to a surge in demand for automation equipment essential for Industry 4.0. Taiwan’s overall machinery industry approached a production value of nearly one trillion NT dollars in 2017, with a growth rate of approximately 5.7%. Industries such as semiconductors, panel manufacturing, and mechanical transmission components experienced double-digit growth.
As high-tech equipment and machine tools move towards full automation, corresponding monitoring and measurement systems are essential to extend the lifespan of industrial machinery. Gude provides portable vibration measurement devices to manage frontline operations, while IIoT-based industrial monitoring systems handle long-term steady-state operations to ensure quality control.
Inspection Management
Portable Instrumentation for Troubleshooting
Issue Identification & Inspection Management
Online Monitoring
Predictive Maintenance
Monitoring Equipment to Maintain Yield
Industrial IoT
IIoT Smart Factory Solutions
Comprehensive Equipment Data Monitoring
Control Room Management
VMS + IIoT Integration
Smart Factory Monitoring
Helping Factories Transform into Smart Manufacturing
Digital Transformation Solutions
Many small and medium-sized traditional industries face challenges in upgrading and transforming their businesses, mainly due to financial and management constraints.
One issue is the lack of substantial budget to purchase automation equipment, and another is the inability to implement data-driven management systems.
In the era of smart manufacturing, digital transformation is inevitable. But does digital transformation necessarily require a large investment?
For small and medium-sized enterprises (SMEs) with limited resources, is there a simpler and smoother upgrade solution?
EMS Smart Energy Management System
As companies are increasingly required to achieve carbon neutrality or emission reduction targets within their production processes to support global sustainability efforts,
effective energy management is a key step toward achieving sustainable production goals.
Source: Online news, Taiwan Hydrogen and Fuel Cell Partnership, Technology News, Wikipedia