Digital Transformation Solutions
Solutions|Digital Transformation SolutionsMany small and medium-sized traditional industries face challenges in upgrading and transforming their businesses, mainly encountering issues related to funding and management. How can existing usable equipment be transformed into smart machinery?
Reasons for Implementation
Digital Transformation of Industrial Upgrades Must Be Gradual
The first priority is to start collecting key equipment data and build the system step by step.
With the rapid advancement of Industry 4.0, many small and medium-sized traditional industries struggle with business upgrades and transformation, primarily facing financial and management challenges. First, they lack the large capital required to purchase automation equipment. Second, they lack the capability to implement data-driven management systems. In the era of smart manufacturing, digital transformation is inevitable. But does digital transformation necessarily require massive financial investments? Business transformation should not be rushed—it must be a gradual process. For these resource-limited small and medium-sized traditional industries, is there a simpler and pain-free upgrade solution? How can existing equipment be transformed into smart machinery?
Many enterprises have adopted various automation equipment to significantly reduce labor costs and shorten working hours while assigning hazardous or repetitive tasks to automated machines. At the same time, companies must tackle the challenge of effectively managing these automation systems. Equipment transmits operational data to users, indicating the machine’s current status, but how can this data be translated into actionable insights for humans?
Digital transformation, also known as data-driven upgrading, starts by collecting machine-generated data. This data is then analyzed, refined, and characterized to extract valuable insights that optimize production lines, enhance productivity, and improve facility management. For small and medium-sized traditional industries looking to embark on digital transformation, the first priority should be collecting critical equipment data and setting up the system gradually, following a phased approach.
Core Concept
Three Key Factors for Digital Transformation
Clear Objectives
When implementing automation equipment and digital management systems, businesses must not only understand market demands but also consider how to maximize revenue. The ultimate goal of digital transformation is to ensure sustainable business growth. Decision-makers must ask themselves: What do I want to see from digitalization? What benefits should be achieved? What challenges might arise? What are the short-term, mid-term, and long-term objectives? Considering these critical factors will ensure a well-planned and successfully executed strategy.
Cost Control
For many small and medium-sized traditional industries, financial resources are already limited, making budget allocation even more critical. When evaluating equipment or systems, hidden costs must also be considered, such as downtime during installation, training labor hours, ongoing maintenance costs, and the scalability of the system for future expansion. Digital transformation is not an overnight process—it requires a step-by-step approach with phased goals. This ensures effective implementation and optimal use of the budget.
Human-Centric Approach
One of the biggest challenges in business transformation is people—this includes workforce training, management, and skill development. Whether introducing automation equipment or implementing digital management systems, human factors must be prioritized. The ultimate goal of facility management is to improve efficiency. However, even if a digital system offers numerous features and detailed data, if it is not user-friendly, it will only burden employees rather than enhance efficiency. A well-implemented system should simplify operations, optimize workflows, and maximize efficiency without adding unnecessary complexity.
Execution Challenges
Equipped with Automated Equipment, but Production Efficiency Remains Low?
Despite heavily investing in automation equipment, are you still unable to improve production efficiency? This indicates management issues within the facility, such as undetected equipment anomalies or human errors, preventing the optimization of equipment performance and leading to declining production efficiency.
How to Execute
Upgrade Quickly Using Existing Equipment
Goodtech’s OEE Equipment Utilization Management System utilizes existing machines’ three-color indicator lights and installs sensors to collect data into the system. This helps users quickly understand the equipment utilization rate across production lines, identify abnormal downtimes, detect idle times, analyze utilization trends, and clarify the root causes to optimize decision-making.
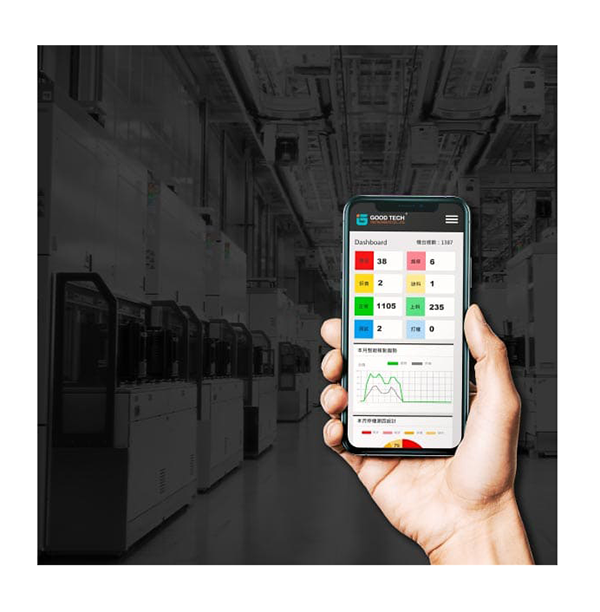
OEE Equipment Utilization Management System
The system applies to various factory machines equipped with three-color indicator lights, such as CNC machines, cutting machines, etc. The optical sensors are easy to install and quickly collect data, which is then processed by the system to visualize equipment status, calculate utilization rates, and display graphical data to help users better understand production conditions.
OEE Equipment Utilization Management SystemExecution Challenges
High System Costs Leading to Paper-Based Inspections?
Many factories believe digital transformation is too costly and unnecessary for data management. Equipment inspections still rely on manual efforts—data is written in notebooks, equipment status is observed visually, and abnormalities are diagnosed based on assumptions. The more equipment there is, the more complicated management becomes, leading to frequent errors. Furthermore, tracing issues for corrective actions is nearly impossible, causing recurring mistakes and inefficiencies.
How to Execute
Digitized Management to Reduce Human Errors
For various equipment inspection data, the IMS Industrial Monitoring & Inspection System allows users to set up inspection checklists, perform statistical analysis, and track historical records online. This eliminates the hassle of sorting through paper records and allows users to schedule inspections, set threshold values, and receive alerts for anomalies.
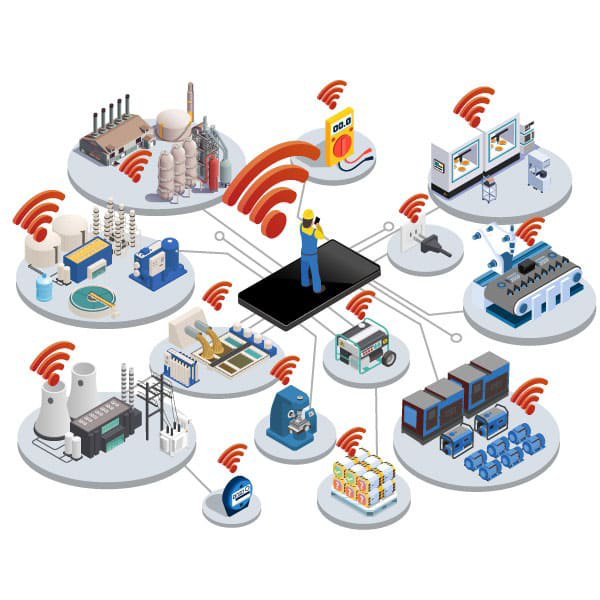
IMS Industrial Monitoring & Inspection System
A smart inspection system with flexible setup capabilities, assisting inspection personnel in mobile patrols and data management.
IMS Industrial Monitoring & Inspection SystemHow to Execute
Digital Transformation Solutions
The phased objectives of digital transformation should be gradually adjusted based on the conditions and goals of each facility. Goodtech provides flexible digital upgrade solutions for factory equipment monitoring issues, enabling the most immediate and simplest management methods for existing equipment to gradually achieve factory intelligence.
Implementation Benefits
Driving Industrial Transformation Towards Smart Manufacturing
In traditional industries, manufacturing quality often relies on the expertise of experienced workers. Many are resistant to factory automation or believe that digital transformation requires a significant investment, seeing no necessity for implementing digital management. However, industrial transformation can be achieved effectively and efficiently through a phased and strategic approach, utilizing existing equipment for the fastest and most beneficial digital management.
Automation focuses on replacing manual labor with machines for hazardous or repetitive tasks, significantly reducing workforce burdens. As equipment and machinery become automated, enhancing equipment intelligence is crucial, which requires monitoring and management systems to extend the lifespan of machinery.
Goodtech offers a range of monitoring solutions that integrate experienced craftsmanship with standardized guidelines. With a flexible system architecture that allows for future expansions, these solutions help factories maintain production line maintenance mechanisms or implement full-scale factory monitoring. This improves automation equipment quality, accelerates industrial transformation, and advances smart manufacturing.
Easy Installation
Simple Operation
Fastest ROI
Flexible Expansion
Support
Other Digital Transformation Topics