How to Start Predictive Monitoring and Plan a Smart Manufacturing Factory?
FAQ | How to Start Predictive Monitoring and Plan a Smart Manufacturing Factory?In the era of Industry 4.0 and smart manufacturing, factories are rapidly adopting automation to stay ahead. However, they often face common challenges. While automation replaces human labor, machines cannot communicate their status. When unexpected downtime occurs, significant losses have already been incurred.
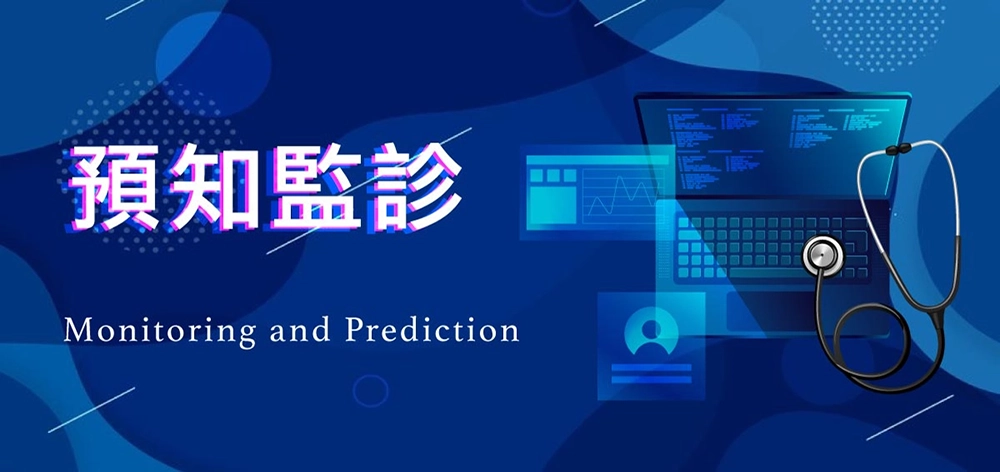
The Relationship Between Predictive Monitoring and Smart Manufacturing
Automation Equipment and Monitoring Go Hand in Hand
When it comes to smart manufacturing, you may ask:
Does having automation equipment alone mean achieving smart manufacturing?
Has the quality of the finished products improved?
When does equipment failure occur? And why does it happen?
The cost of upgrading the production line is already high, so how can expenses be reduced?
How can we continuously improve and enhance production line efficiency?
The current manufacturing line is still usable, but how can we integrate smart functions effectively?
In the era of Industry 4.0 and smart manufacturing, factories are rapidly adopting automation to stay competitive.
However, they often face common challenges. While automation replaces human labor, machines cannot communicate their status.
When unexpected downtime occurs, significant losses have already been incurred.
Therefore, having automation equipment alone is not enough. It is essential to implement real-time monitoring solutions to accurately grasp the smart manufacturing process.
Start Planning the Right Predictive Monitoring Strategy!
Accurately Monitor Equipment Status
To save on maintenance budgets, users often wait until machinery has serious issues or even complete failure before replacing parts.
However, they fail to anticipate that unexpected breakdowns can cause production line disruptions, delays in repairs, and extended waiting times for spare parts.
All these factors lead to higher costs and even pose potential workplace safety risks.
Even for users who follow a regular maintenance schedule, machine downtime probabilities can be significantly reduced,
but they still lack insight into the actual benefits of equipment servicing. In some cases, over-maintenance occurs.
The higher the maintenance frequency, the higher the costs. With numerous machines to manage, ensuring proper inspections is challenging.
If equipment could proactively inform users of its current status or if measurement instruments could detect anomalies,
unexpected failures and losses could be avoided.
Predictive Maintenance
It refers to enabling users to accurately monitor equipment status, increase machine reliability, and reduce unexpected downtimes.
By reducing unnecessary scheduled maintenance and spare parts stockpiling while aligning with production processes,
predictive maintenance helps extend equipment lifespan, lower maintenance costs, and enhance overall efficiency and productivity.
Machine Reliability
Consistent Product Quality
Reduce Over-Maintenance
Precise Maintenance Execution
Establish Maintenance Plans
Efficient Production Line Scheduling
Extend Equipment Lifespan
Increase Equipment Utilization
How to Start Predictive Maintenance?
Monitor Equipment Status and Develop a Maintenance Plan
Predictive maintenance is closely related to equipment diagnostics. Monitoring and diagnosing equipment status provide the foundation for predictive maintenance planning.
By analyzing the vibration characteristics of machinery, equipment conditions can be evaluated.
With a monitoring system, equipment can be tracked based on its usage patterns, either through scheduled checks or long-term continuous monitoring.
The collected data allows for decision-making regarding further actions and scheduling.
This process helps optimize production efficiency, detect equipment anomalies, estimate equipment lifespan, and enable self-monitoring with automated alerts for users.
For complex automated production lines, diagnostic monitoring ensures production quality consistency and enhances equipment reliability.
Factory equipment is complex and diverse—how should a diagnostic monitoring plan be structured?
For machines that require long-term monitoring and are located in remote areas, how can maintenance be effectively managed when technicians cannot access them?
Core production line equipment is expensive and operates continuously—how should priority-based monitoring be conducted?
If workplace safety inspections fail, more comprehensive monitoring solutions are needed.
After maintenance, how can we verify whether the equipment is truly effective?
How can quality control confirm that finished products meet consistency standards and that all internal functions are operating correctly?
These challenges can be addressed by equipment diagnostic consultants.
With years of expertise in measurement solutions, GoodTech leverages edge computing technology to provide customized measurement solutions for equipment.
The system is easy to operate, allowing users to interpret results at a glance.
This helps users monitor equipment status, establish maintenance plans, and improve both productivity and quality.
The Hidden Costs You Might Be Overlooking
The Importance of Predictive Maintenance
Have you realized the importance of predictive maintenance? Once you implement it, you will notice significant savings on hidden costs that are often overlooked.
As machines are used over time, their components gradually wear out. When abnormal vibrations begin affecting manufacturing quality,
machine efficiency declines, leading to a decrease in production efficiency (OEE).
If such issues are not addressed early, equipment may age prematurely or require early retirement.
Defective products generated during manufacturing also contribute to hidden costs.
Many users believe that since equipment is expensive and undergoes regular maintenance,
they can save costs by repairing only after equipment failure.
However, an unexpected production line shutdown can delay orders, decrease productivity, and waste human resources—resulting in greater losses.
With numerous machines in a factory, users often send equipment for maintenance checks without truly knowing whether an issue exists.
Over-maintenance can occur when machines are serviced simply because the scheduled time has arrived,
wasting unnecessary time and maintenance budgets.
Whether maintenance is conducted in-house or by external technicians,
customer service teams may assess that parts need replacing based only on the time elapsed.
Sometimes, machines are disassembled, and all parts are replaced without proper diagnosis,
resulting in wasted time and labor.
If a specific faulty component is identified, replacement parts might need to be ordered from overseas,
leading to long wait times and increased repair delays.
Once the machine is serviced and returned to the factory, how can its efficiency be evaluated?
If production efficiency and operational rates do not improve post-maintenance, then the entire process becomes a waste of resources.
Reduced Operational Efficiency
Equipment Malfunction
Factory Maintenance Inspection
Customer Service Evaluation
Long Wait for Spare Parts
Restored Machine Performance
Planning Predictive Monitoring Solutions for You
Professional Integrated Planning Services
The era of smart manufacturing is here—are you ready? From equipment components to precision manufacturing and final product assembly,
it is essential to not only improve manufacturing efficiency but also consider product yield rates and post-production maintenance.
In the Industry 4.0 era, many small and medium-sized enterprises and factories are still struggling with how to implement smart manufacturing.
Do you want to upgrade your equipment but face budget constraints?
Are you unsure how to plan in-factory measurement systems?
As your company expands and new equipment is introduced, do you find it challenging to maintain quality control?
Factory equipment comes in various types and complexities—some require long-term monitoring,
others need targeted inspections, while some demand regular maintenance.
All of these require systematic planning with user-friendly monitoring solutions.
GoodTech has extensive experience in measurement solutions across factory operations, technology manufacturing,
production plants, quality control, FABs, SUB-FABs, automotive manufacturing, robotic arms, and stamping industries.
Utilizing edge computing, we have developed various models of multi-functional measurement and monitoring systems,
including machine learning, AI intelligence, and IoT technology.
Our professional integrated planning services help businesses and users adapt to smart manufacturing trends,
upgrade factory equipment, and enhance productivity, quality, and corporate value.
Diagnostic Monitoring Process
Effectively Managing Various Equipment in the Factory
GoodTech provides comprehensive factory diagnostic monitoring planning.
Are you unsure how to address complex equipment issues? Or are you unable to identify the root cause of equipment anomalies?
Seek assistance from an equipment diagnostic consultant.
By integrating monitoring systems tailored to different machines,
factory equipment can be effectively managed, machine health can be assessed, maintenance plans can be formulated in advance,
and equipment lifespan can be estimated, ultimately achieving predictive maintenance.
To upgrade to smart manufacturing, most factories incorporate automated or semi-automated equipment.
While many small and medium-sized enterprises may not be able to fully implement automation at once,
upgrading factory processes to smart systems does not necessarily mean eliminating older equipment.
A gradual approach combined with human expertise can also enable machinery to become more intelligent.
1 / Factory Consultation: Understanding Needs & Identifying Issues
Equipment problems may lead to reduced product yield, production line downtime, or even machine damage and safety hazards due to poor factory setup.
Finding a suitable solution is crucial.
2 / Evaluation & Planning: Assessing Factory Layout & Developing a Plan
By evaluating factory layout and technical requirements, users can receive optimized plans based on experience.
Solutions may involve portable measurement instruments, wireless monitoring systems, or customized monitoring solutions.
3 / Implementation & Development: Designing Software & Hardware Solutions
Technical support includes software development, designing different hardware solutions tailored to machine types and data collection goals,
as well as ensuring compliance with factory standards during installation, wiring, and equipment deployment.
4 / Testing & Optimization: Adjusting Functional Tests & Planning Upgrades
Equipment is tested on-site, leveraging edge computing for data collection and machine quality analysis.
Based on data insights, further diagnostic monitoring plans are developed, equipment parameters are fine-tuned, and monitoring devices are upgraded accordingly.
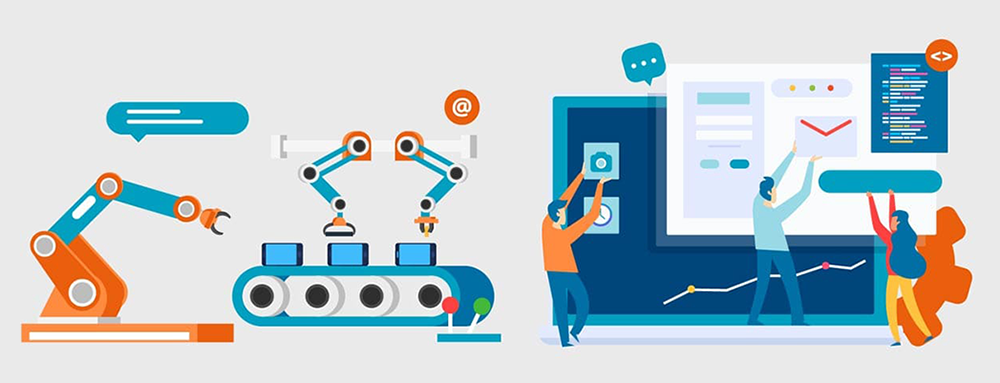
Managing Continuous Rotors & Cyclic Equipment
Factory-wide Rotary Machinery
As businesses face increasing pressure to achieve carbon neutrality or emission reduction goals in their production processes, effective energy management is a crucial part of achieving sustainable manufacturing goals.
Factory-wide Rotary MachineryCyclic Production Equipment
Composed of multiple mechanical and electrical systems, these machines perform various production tasks and execute repetitive cyclic processing. We classify them as cyclic (repetitive) production equipment.
Cyclic Production Equipment