With Numerous Machine Tools in the Facility, How to Prioritize Maintenance?
Case|With Numerous Machine Tools in the Facility, How to Prioritize Maintenance?Motors account for the largest proportion in various automated equipment. In terms of precision control for machine tools, servo motors and stepper motors play a key role. With so many tools in operation, how can maintenance schedules be effectively and quickly arranged?
Working Principle of Servo Motors
Motors make up the largest portion of various automated equipment. For machine tool precision control,
servo motors and stepper motors are commonly used. What is a servo motor? Servo motors, classified into DC and AC types,
offer high responsiveness, reaching speeds above 2000 rpm in a short time.
Their operational characteristics include position control and speed regulation. Key features of servo motors include
precise speed control over a wide range, stable and smooth operation even at low speeds, and the ability to instantly
accelerate or decelerate based on demand. They can quickly switch between forward and reverse rotation and maintain position
even under external forces. Within their rated capacity, they can generate high torque instantly, with high output power
and efficiency. Source: Wikipedia
Solution and Monitoring Explanation
VMS-PH Dynamic Quality Analysis Instrument
The VMS-PH dynamic quality analysis instrument is used to compare the dynamic signals of servo motors and slide rails.
Based on the analysis results, an optimal maintenance schedule can be arranged.
Measurement Conditions
1. Measurement Position: Left side of the X-axis slide rail, vertical motor casing.
Measured Machines: A, B, C, D, E, F, G, H.
Measurement Objective: Servo motor quality.
2. Measurement Position: Right side of the X-axis slide rail, horizontal direction.
Measured Machines: A, B, C, F, G, H.
Measurement Objective: Slide rail quality.
Spectrum Analysis: Utilize intelligent spectrum threshold management to monitor machine conditions.
1. X-Axis Slide Rail Left Side Motor Casing Vertical Measurement Point
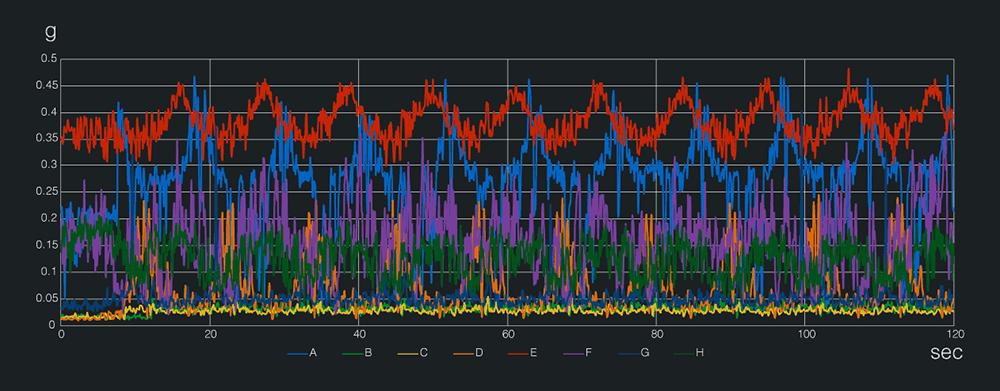
Servo Motor Quality
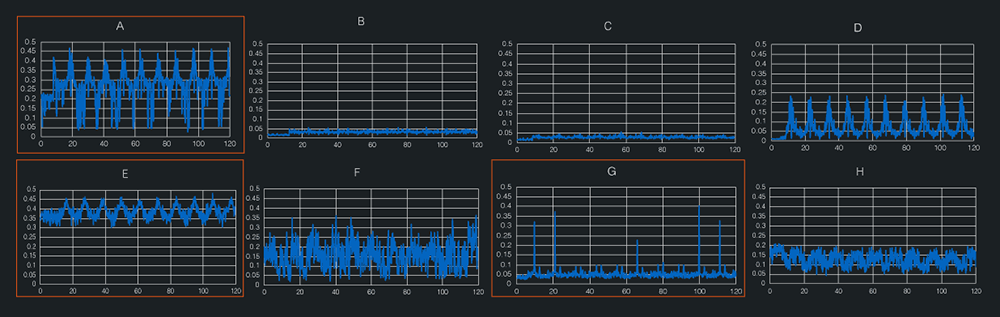
Results: Machines A and E have higher servo motor vibration levels, G has abnormal signal characteristics.
2. X-Axis Slide Rail Horizontal Measurement Point
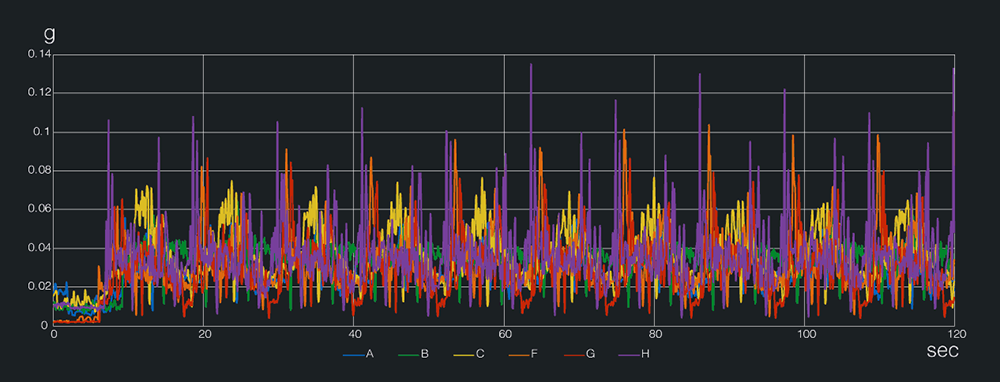
Slide Rail Quality
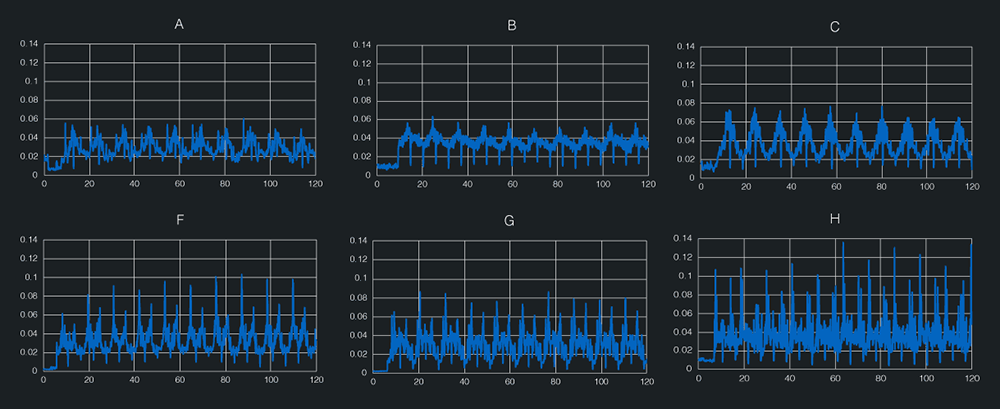
Results: Slide rail quality dynamic analysis ranking: HFGCBA
Intelligent Spectrum Threshold Detection
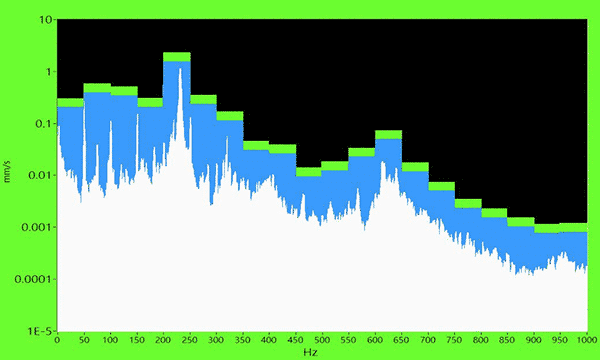
Abnormal Spectrum Detection Alerts
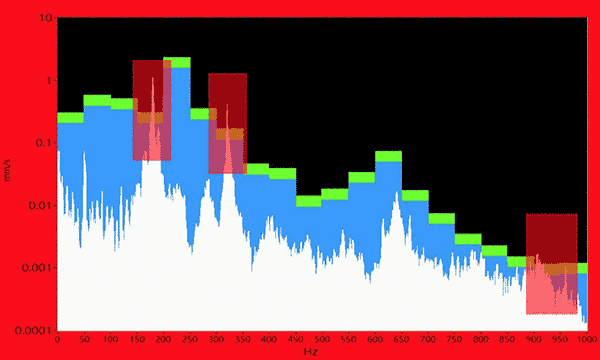
For the X-axis, intelligent thresholds can be set for each machine. Once vibrations at other frequencies occur, differences can be detected.
Measurement Conclusion
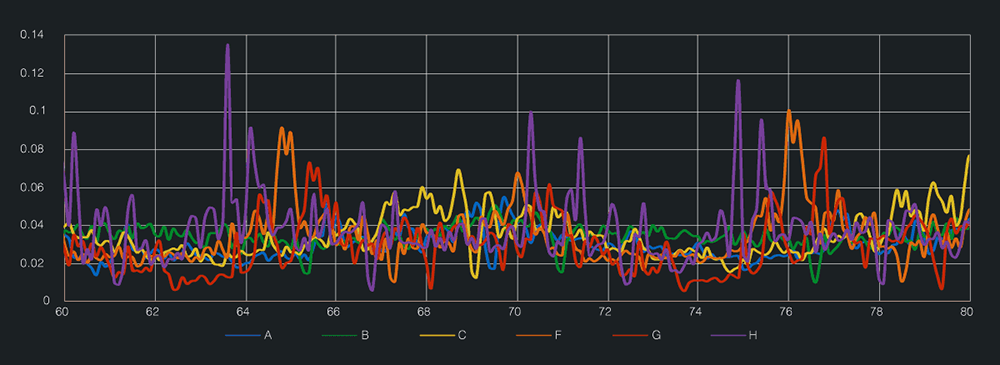
If the X-axis slide rail threshold g-value is set at 0.08
H is the highest, followed by F and G. These three machines show the largest deviation compared to the others,
so H should be inspected first.
It is recommended to measure the X-axis slide rail at the right horizontal position.
For this analysis, the machines H, F, and G should be inspected first.
The X-axis vertical measurement points can be used for servo motor dynamic signal comparison across machines.
A and E have the highest values, while G shows abnormal signal characteristics.
Spectrum analysis helps confirm machine frequency domain performance.
Intelligent threshold settings enable quick identification of frequency differences,
providing insights into machine condition changes.
The VMS-PM dynamic analysis instrument is designed for high-end precision equipment, featuring spectrum analysis, time-frequency analysis, vibration transfer rate, and dynamic analysis. It allows for on-site analysis to help users quickly and accurately pinpoint equipment issues.
VMS-PM Equipment Dynamic Analysis Instrument