Upgrade to Smart Machine Tools with Decision-Making Capabilities
Feature Description
The Heart of Machine Tools: Controlling Spindle Quality
Is your machine tool's spindle in good condition? The spindle is the heart of the machine tool, so controlling the quality of the spindle is of utmost importance.
VMS®-PM Mechanical Dynamic Analyzer can measure the vibration quality, dynamic balance, and resonance in the spindle's operating speed range for various types of spindles (including direct-drive, gear-driven, belt-driven, and internal spindles) in real time and display the results on-site.
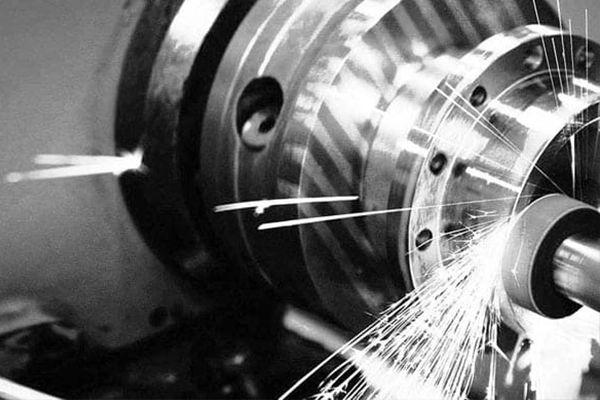
Feature Description
Manufacturing Tool Machine Component Quality Control
In addition to the inspection quality of the machine tool itself, the installation environment, speed of the moving structure, and the rotation speeds of various components will also affect processing quality.
VMS®-PM Mechanical Dynamic Analyzer can control other key components such as: pulleys, gearboxes, transmission machinery, the movement quality of various axes, and structural analysis of the machine body.
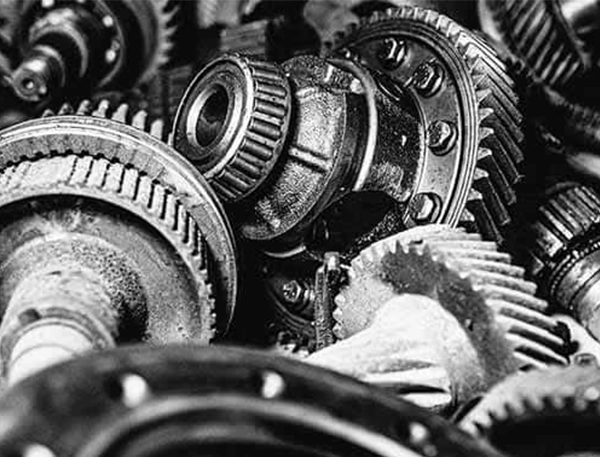
It can instantly measure and analyze the movement quality of single-axis, three-axis, five-axis machines, multi-axial moving structures, rotating tables, and more. The results can be immediately determined and used as a standard research and development tool for tool machine design.
Feature Description
Built-in Tool Machine Standard Value Norms
The status is displayed with different colored lights, making it easier for users to assess the equipment status. In addition, the system leads the market in monitoring software by adding the latest ISO 20816 standard, enabling users to better manage motor rotor components.
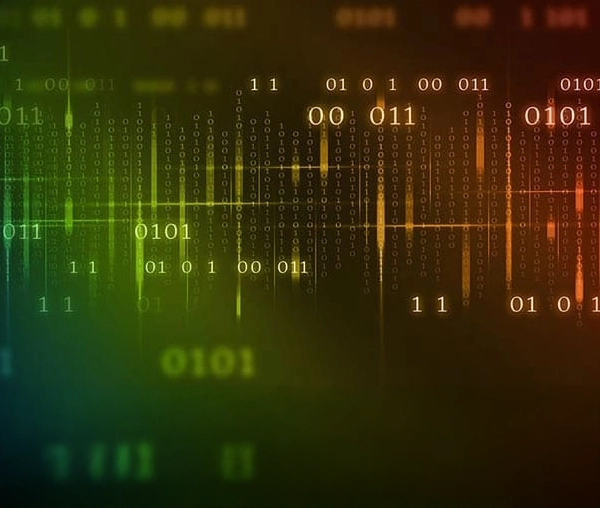
The status is displayed with different colored lights, making it easier for users to assess the equipment status. In addition, the system leads the market in monitoring software by adding the latest ISO 20816 standard, enabling users to better manage motor rotor components.
Feature Description
Custom-Designed Analyzer for CNC Tool Machines
VMS®-PM Mechanical Dynamic Analyzer is easy to carry, featuring a touch screen, four sensor interfaces, and a USB transmission port, allowing users to carry the device and perform measurements anywhere. The intuitive interface lets users select the appropriate specifications based on the equipment's wattage and size, enabling even non-experts to conduct machine diagnostics. A mini tablet version is also available, providing operators with easy measurement and analysis capabilities.
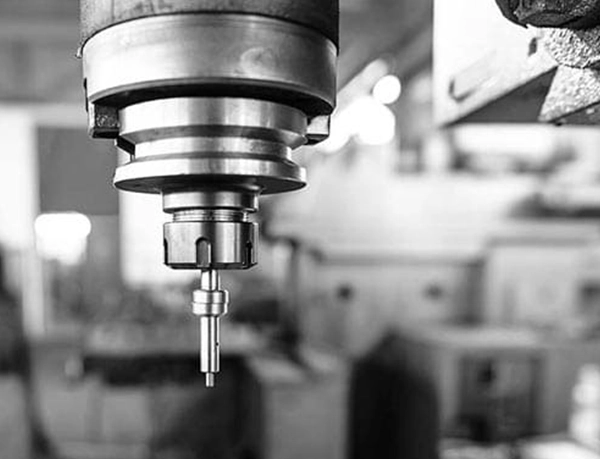
Made for
Tool Machines
Tailored to meet industry needs, VMS®-PM Mechanical Dynamic Analyzer was designed specifically for this purpose. It performs real-time measurement and analysis of various tool machine spindles and components, with results displayed instantly. It can be used as a standard R&D tool, quality control instrument, or the best diagnostic tool during client-side troubleshooting.
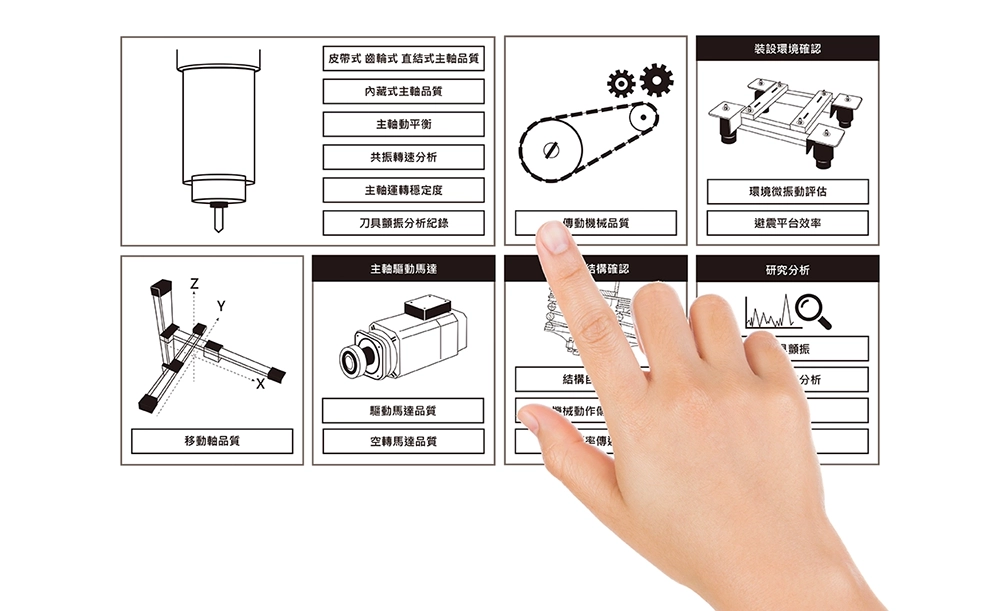
Application Scope
Suitable for quality measurement of various processing machines
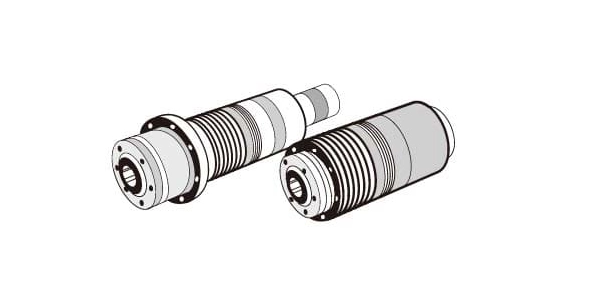
Spindle Quality Inspection
Includes direct-drive, gear, belt, and internal spindles. Use vibration signals from the non-rotating parts of the rotor machinery to evaluate the rotor.
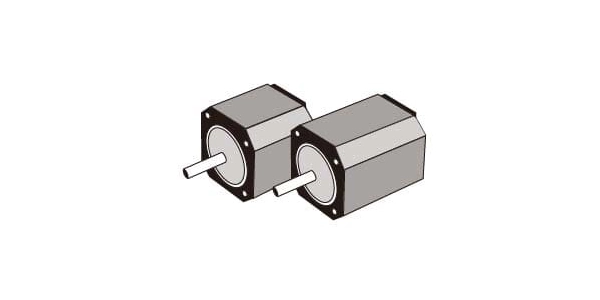
Spindle Motor End
Many power sources in the equipment are transmitted through motor rotors, so the health of the motor rotor equipment is closely related to the health of the machine equipment.
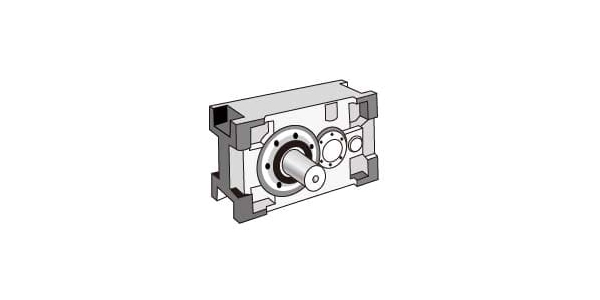
Gearbox and Other Composite Mechanisms
To know if the equipment efficiency is good, you must first understand whether transmission devices like gears are working correctly, allowing energy to be transmitted smoothly to the equipment.
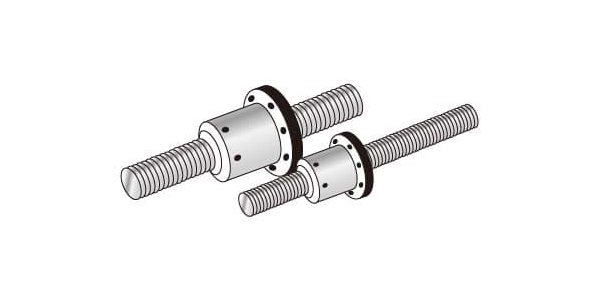
Screw and Other Driving Mechanisms
During movement, rotation, reciprocation, or stopping, certain vibrations occur. Evaluating vibration changes helps assess the manufacturing process.
Feature Explanation
UI Function Screen
Spindle Vibration Quality Inspection Standards
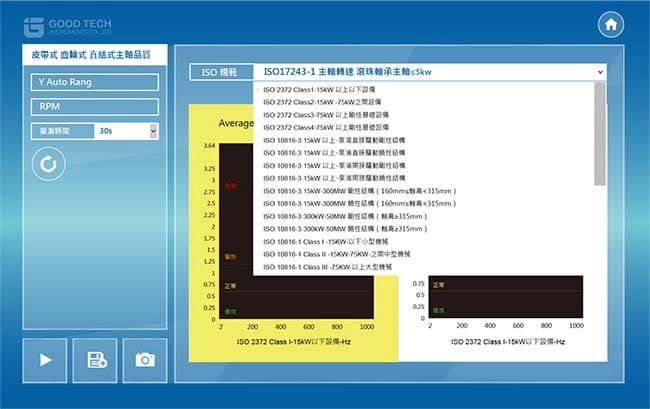
ISO-10816: Direct-coupled, Gear-driven, Belt-driven Spindles
Measurement types: Small rotor machines, Medium rotor machines, Large rotor machines
Speed range: 120-15000 RPM Test conditions: Tested without load
Classification criteria: Power, Shaft height, Structure (flexible or rigid)
ISO-17243: Built-in Spindles
Bearing type restrictions: Rolling bearings
Speed range: 600-30000 RPM Spindle type: Built-in spindle
Test conditions: Tested without load (no cutting, no milling, no grinding)
Classification criteria: Power, Maximum speed, Bearing type (Ball bearings, Roller bearings)
Spindle Balancing Management: ISO 1940
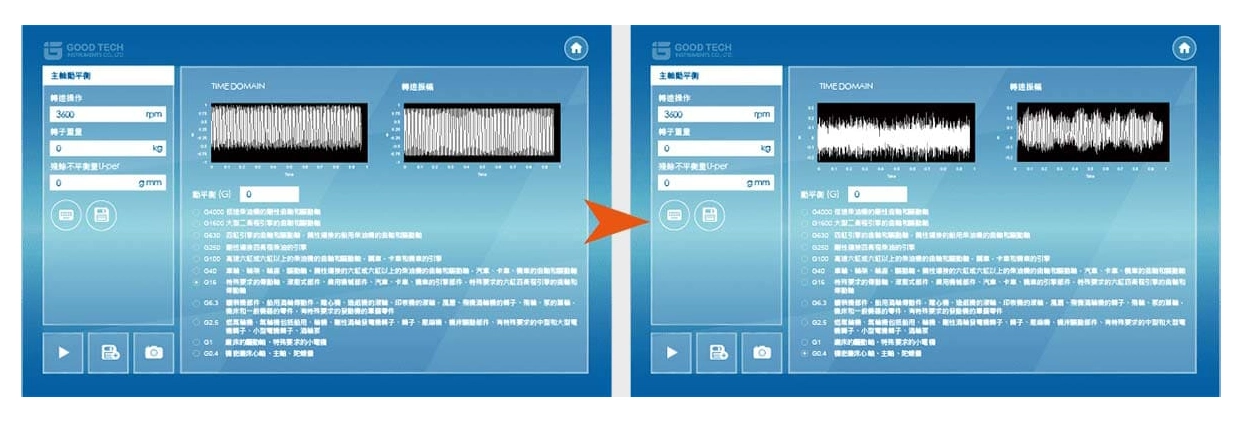
Spindle vibration imbalance can easily cause tool wear or accuracy errors. Since spindles and tools are often expensive, when spindle tool anomalies occur, they can further increase product defect rates and losses. Most rotating equipment and rotor machines undergo regular balancing calibration to avoid excessive vibrations caused by imbalance, which can lead to mechanical damage.
Spindle and Resonance Frequency Relationship
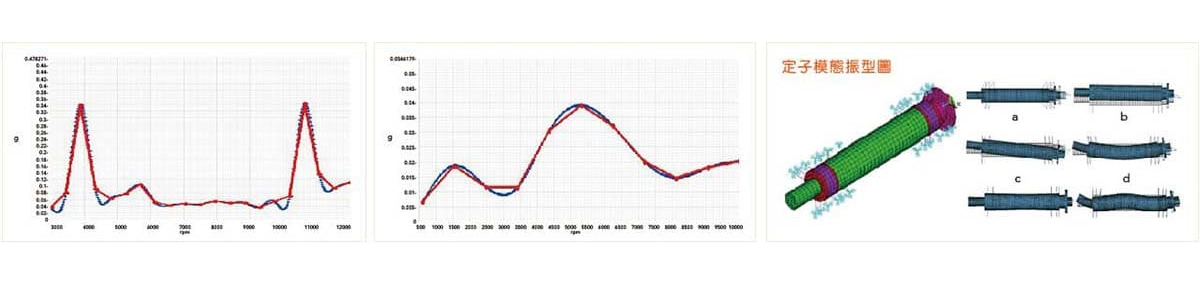
If rotating equipment exhibits resonance speeds, parameters should be set to avoid operating in the resonance frequency range, which can affect the spindle efficiency. The structure of a machining machine is composed of different components, and the natural frequencies caused by each component will influence each other, resulting in resonance problems that affect the spindle's operation and lifespan. Identifying the resonance range and avoiding inappropriate operating speeds will help prevent resonance.
Dynamic Signal Recording and Difference Monitoring During Workpiece Processing
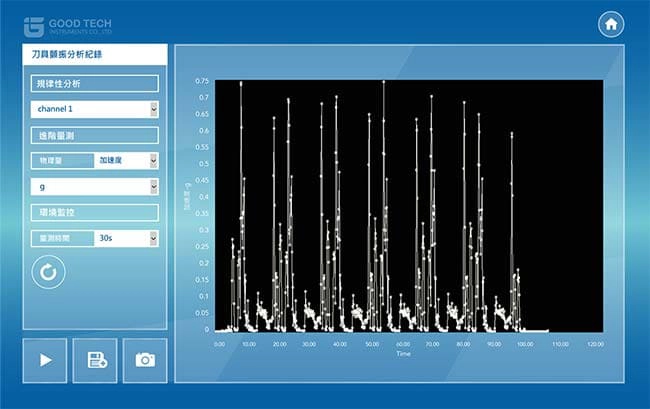
VMS®-PM Mechanical Dynamic Analyzer can record and monitor the dynamic signal cycle during each workpiece's processing. Identical workpieces and tools will generate similar dynamic signals.
If there are any abnormalities in the workpiece or tool, the program will detect significant differences in similarity and alert the user to check for anomalies in the workpiece or tool, preventing the production of defective products in the batch and saving time and cost on defective items.
Industry 4.0
Legacy Upgrade
Are you ready to upgrade your tools to smart machines? The portable VMS®-PM Mechanical Dynamic Analyzer is designed specifically for tools, helping traditional manufacturing plants upgrade to Industry 4.0. It is suitable for various traditional industries and all types of CNC machining and manufacturing tools.
Application Explanation
Recommended Measurement Types and Application Functions
Measurement Type | Application Function |
---|---|
Belt-driven, Gear-driven, Direct-drive Spindle Quality | Measure the quality of various rotor spindles according to ISO standards. |
Built-in Spindle Quality | Measure the quality of built-in spindles. |
Spindle Balancing | Measure the balancing level and residual imbalance of rotating spindles. |
Resonance Speed Analysis | Measure resonance caused by rotational vibrations in the spindle within the controlled speed range. |
Spindle Operation Stability | Measure vibration values and perform frequency spectrum analysis to assess the operational stability of the spindle over time. |
Tool Chatter Vibration Analysis | Record vibration changes at startup after the tool assembly. |
Transmission Mechanism Quality | Customize the vibration measurement for transmission mechanisms like gearboxes and pulleys, adjusting frequency bandwidth and tolerance. |
Moving Axis Quality | Measure vibration values during the movement of the axis to assess if there is rail damage or abnormal driving. |
Accelerometer Gain | Calibration function for accelerometers. |
Drive Motor Quality | Measure the quality of various rotors, rotating machinery, and motor systems according to ISO standards. |
Idle Motor Quality | Quality check for motors without load. |
Natural Frequency of Structure | Use two axes to find the resonance frequency produced by an object. |
Mechanical Vibration Transmission Analysis | Open multiple channels simultaneously to measure, compare, and record various vibration behaviors. |
Vibration Frequency Transmission Analysis | Vibration frequency spectrum analysis, measuring time domain, frequency domain, and vibration unit conversions. |
Environmental Micro-vibration Evaluation | Measure vibration targets and classify vibration levels based on environmental vibration recommended standards. |
Shock Platform Efficiency | Measure the signal difference between two accelerometer probes, and measure vibration transmission rate, phase shift, etc. |
Tool Chatter Vibration | Measure vibration values and frequency domain changes during variable-speed operation of tools after assembly. |
Impact Signal Analysis | Capture high-speed vibration dynamics for high-speed stamping mechanisms. |
Frequency Spectrum Analysis | Vibration frequency spectrum analysis function, measuring time domain, frequency domain, and vibration unit conversions. |
Time-Frequency Analysis | 2D and 3D time-frequency analysis of vibration values. |