Quick Deployment, Real-Time Motor Equipment Status Monitoring
Why is it necessary?
Why do we need to establish a rotor monitoring station?
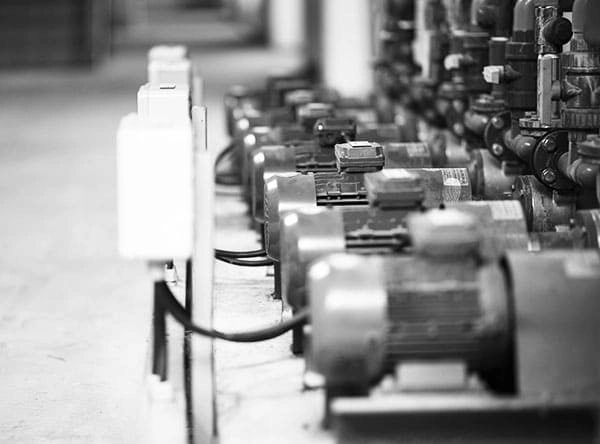
Establish a dedicated system for rotor equipment monitoring
There are numerous rotor devices in the factory, each with specific requirements. A dedicated monitoring system is needed to track their operational status. The system provides professional monitoring indicators and real-time key parameter tracking. When signs of failure appear, it issues alerts to prevent further damage and unexpected downtime.
But if the factory has already established an MES system, why is it still necessary to set up a separate monitoring station for rotor equipment? While integrating data output through the MES system allows a comprehensive understanding of key factory equipment data, For frontline production operators, having a system that provides real-time equipment status monitoring directly at the site helps identify problems early, improve efficiency, and quickly respond to sudden equipment failures. It also ensures stable operation. RM-IoT-Station offers the most cost-effective way to complement an existing MES system, creating a complete and comprehensive monitoring solution.
Common Challenges
Common Issues in Monitoring Key Rotor Machinery in Manufacturing Processes
Various Equipment Brands and Models
Factories have numerous rotor devices of different brands, types, and applications. How can they be managed uniformly?
Zero-Tolerance Downtime Production Line
Critical rotor equipment in essential production lines cannot be stopped. How can it be monitored and managed efficiently?
Complex Monitoring Software
Monitoring systems have complex settings. How can operators use them easily and ensure a smooth transition during handovers?
Difficult to Interpret Equipment Status
Equipment status is often assessed based on subjective experience. How can data-driven management improve accuracy?
Maintenance and Cost Evaluation
Is outsourcing equipment maintenance cost-effective? How can users determine the optimal timing for repairs?
Data Collection and Planning
No predictive maintenance plan in place? How should vast amounts of collected equipment data be utilized?
Feature Description
Equipped with a Three-Axis Sensor, Supporting Over 20 Types of Data
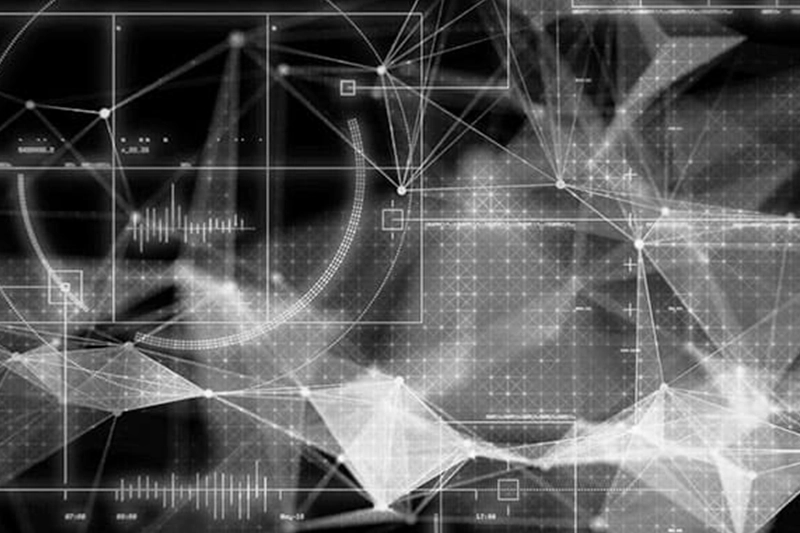
RM-IoT-Station Rotor Health Monitoring Station utilizes a MEMS accelerometer for full-directional measurement, capable of simultaneously detecting three axes (X, Y, Z) to provide comprehensive 3D information.
Since it can measure multiple directions at once, it is much simpler to configure than installing multiple single-axis accelerometers. The collected data is also more detailed, supporting up to 20 different data types. Users can leverage this data for AI training in the future to optimize system processes.
Feature Description
Built-in International ISO Standards, Easy to Use Without Technical Background
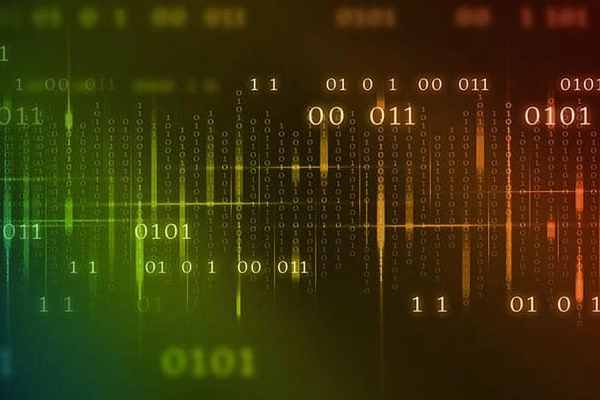
RM-IoT-Station Rotor Health Monitoring Station is equipped with built-in ISO 10816 / 20816 / 2372 standards. Based on these standards, it defines equipment status into four categories: Excellent, Normal, Warning, and Dangerous. The measurement results are displayed instantly, enabling users to quickly identify issues without waiting for inspection personnel, ensuring immediate problem resolution while also helping to establish in-house equipment health management standards.
Additionally, GoodTech leads the market by integrating the latest ISO 20816 standard, allowing users to more comprehensively manage motor rotor components.
Feature Description
Flexible Communication Protocols for Maximum Integration Freedom
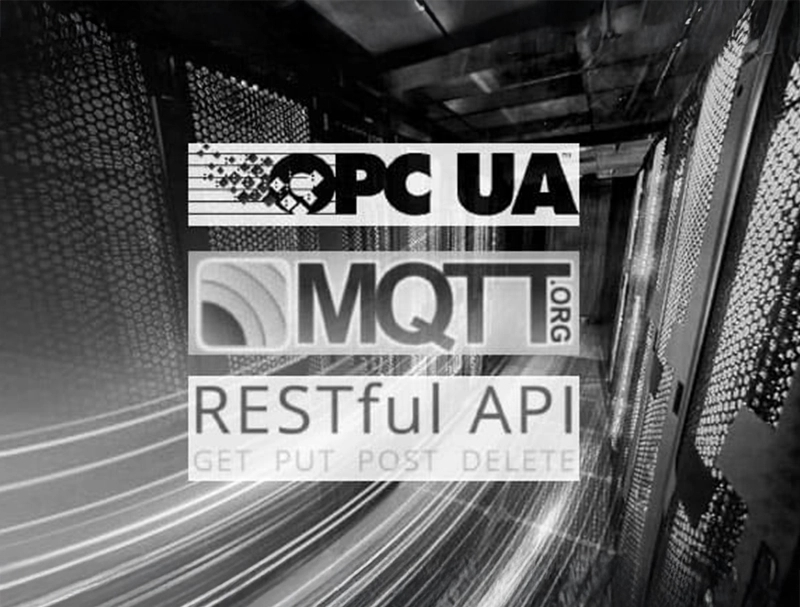
RM-IoT-Station Rotor Health Monitoring Station offers the highest level of flexibility in communication protocols, supporting OPC UA, MQTT, and RESTful API.
By supporting multiple communication protocols, IT professionals can seamlessly integrate the system into existing architectures and extend its functionality to meet future requirements with ease.
This openness and flexibility significantly simplify the integration process, enhancing system interoperability and scalability. Various characteristic data can be transmitted back to the RM-IoT Dashboard or third-party MES systems for AI training, making IT integration with external platforms more efficient and adaptable.
Feature Description
Real-Time Equipment Status Display with Smart HMI Panel
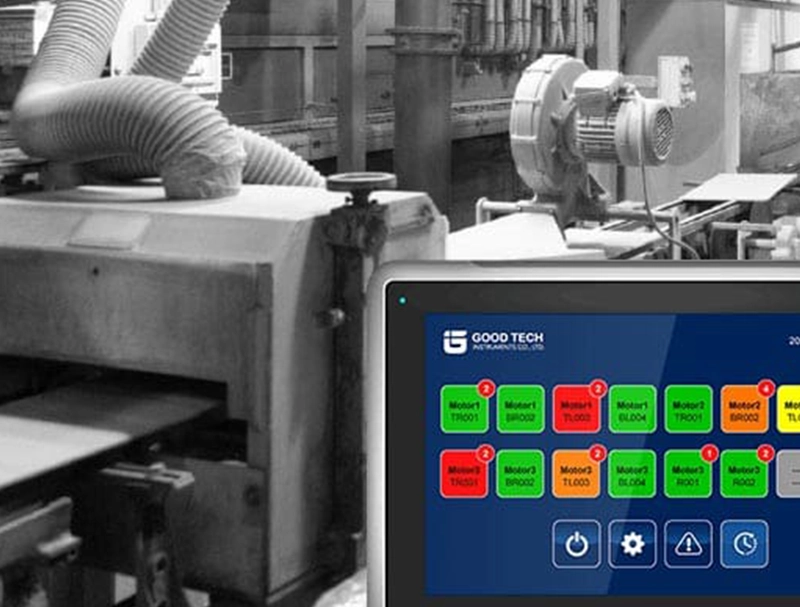
RM-IoT-Station Rotor Health Monitoring Station adopts a non-invasive measurement approach combined with an advanced smart HMI panel.
The smart HMI panel features a widescreen display and an IP65-rated enclosure. It provides an intuitive and user-friendly interface, allowing operators to efficiently monitor equipment status, respond quickly to issues, reduce downtime, and improve overall production efficiency.
Rapid Deployment
Instant Monitoring
For factory sites that have already implemented an MES system, RM-IoT-Station Rotor Health Monitoring Station can be installed quickly and immediately monitor rotor equipment at the production site. It offers flexible transmission options, and data can be uploaded to third-party system management.
UI Functional Interface
Rotor Quality Standard Management

Software Feature Introduction: The Rotor Quality Standard Management system includes
ISO 10816 / 20816 / 2372 standards, applicable to various rotating machinery in
semiconductor and transmission industries (motors, compressors, pumps, etc.).
Users do not need to memorize the standards manually; they can simply apply
the appropriate standard based on the motor output range.
The software uses
indicator colors to differentiate equipment status: Green (Excellent), Yellow (Normal),
Orange (Warning), and Red (Danger), allowing users to instantly grasp the
overall status of all equipment.
UI Functional Interface
User-Defined Standards and Expert Experience Integration
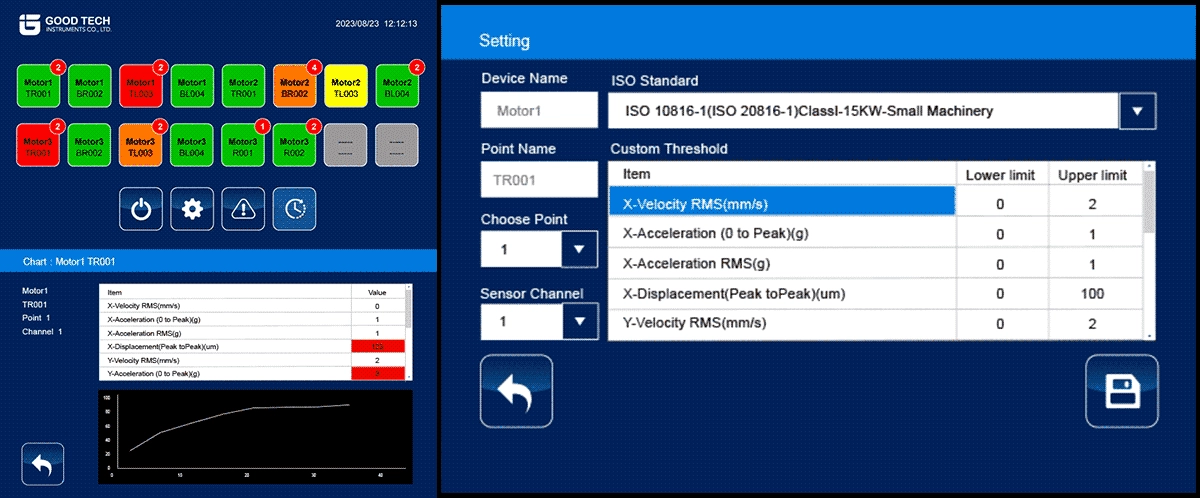
Software Feature Introduction: Customizable Alert Thresholds and Trend Graphs
The system's sensors utilize a three-axis MEMS vibration accelerometer, collecting over
20 types of monitoring data such as temperature, acceleration, velocity, and displacement.
When the ISO standard does not fully meet operational needs, users can define their own
threshold management or set limits based on manufacturer-provided parameters. If the
measured data exceeds the defined threshold, it will trigger a red alert.
All characteristic data are converted into trend graphs, allowing users to clearly
understand equipment degradation trends and maintenance benefits. Users can set the
desired interval range (e.g., weekly, monthly) and visualize trends through charts.
This enables proactive planning for predictive maintenance budgets, workforce allocation,
and production line configurations.
UI Functional Interface
Smart HMI Interface – Easy to Operate
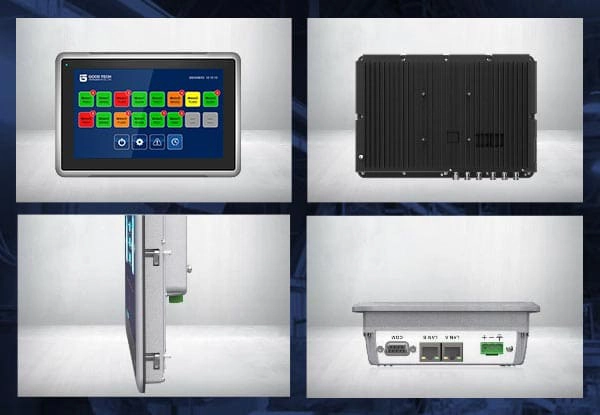

・Wide-screen format for enhanced display space.
・Powerful ARM Cortex-A9 processor.
・Certified by multiple standards: UL, CE, FCC, etc.
・Durable aluminum alloy casing with IP65 protection.
・Equipped with an SD card slot for memory expansion and data backup.
・Marine-grade certification, suitable for all maritime applications.
Application Scope
Suitable for Various Industries' Rotor Equipment
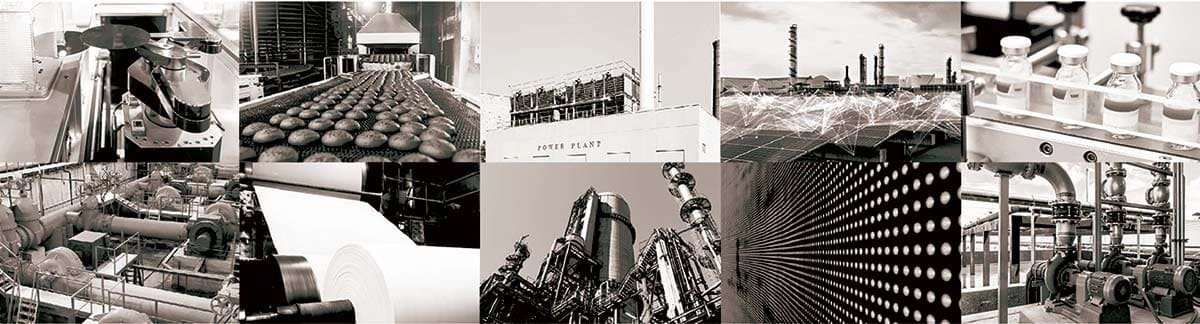
Application Fields:
Semiconductor Industry: Wafer cutting machines, packaging equipment, testing equipment, etc.
Petrochemical Plants: Compressors, pumping stations, fans, rotary equipment, etc.
Food Industry: Mixing, stirring, packaging machines, conveyor belts, and production lines.
Pharmaceutical Industry: Mixing, crushing, tablet pressing, packaging machines, and conveyors.
Pulp & Paper Industry: Pulp mixers, paper-making machines, cutting machines, calenders, etc.
Panel Manufacturing: Glass cutting machines, display manufacturing, assembly equipment, etc.
LED Industry: Cutting machines, dispensing machines, welding machines, and testing equipment.
Power Plants: Turbines, generators, water pumps, and other critical equipment.
Manufacturing & Processing: Machine tools, cutting machines, grinding machines, and conveyors.
Setup Process
Easy Setup & Start Monitoring
1. Install the sensor on the equipment
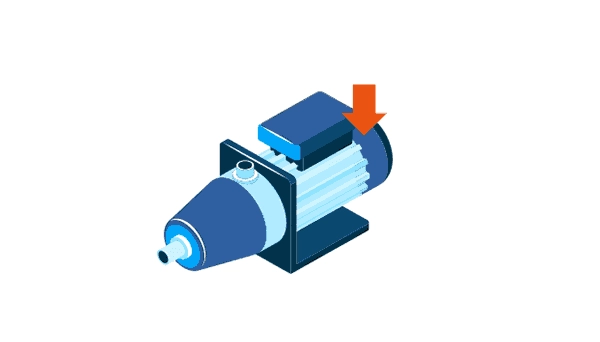
2. Select the corresponding ISO standard and set custom thresholds
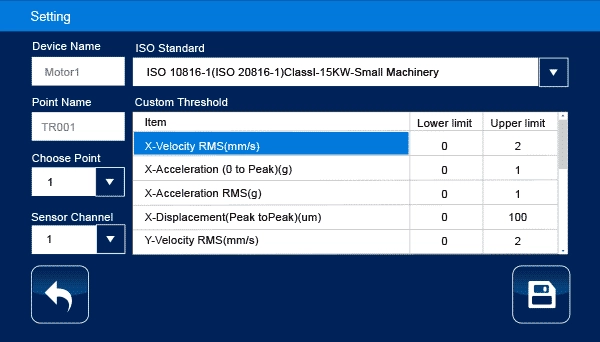
3. Start monitoring – Real-time equipment status display
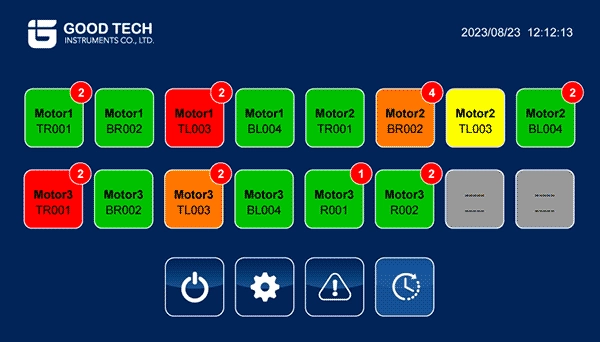
4. Utilize trend monitoring to plan predictive maintenance
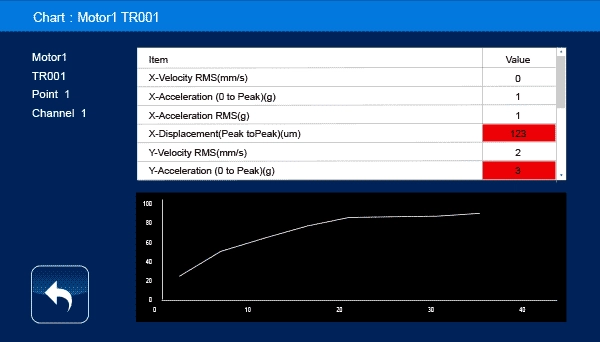
Architecture Overview
Rotor Equipment and System Architecture
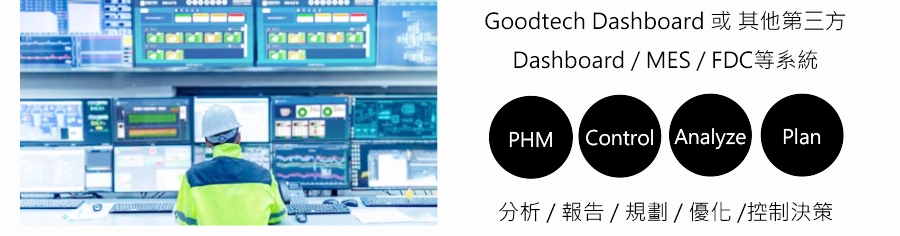



Support
Other Rotor Equipment Related Topics