予知診断を開始し、スマート製造工場を計画する方法とは?
質問集 | 予知診断を開始し、スマート製造工場を計画する方法とは?インダストリー4.0とスマート製造の時代において、各工場は競争力を維持するために自動化設備を積極的に導入しています。 しかし、多くの課題に直面することもあります。自動化設備は人の作業を代替しますが、機械自体は状態を伝えることができません。 予期せぬダウンタイムが発生した際には、すでに大きな損失が発生しているのです。
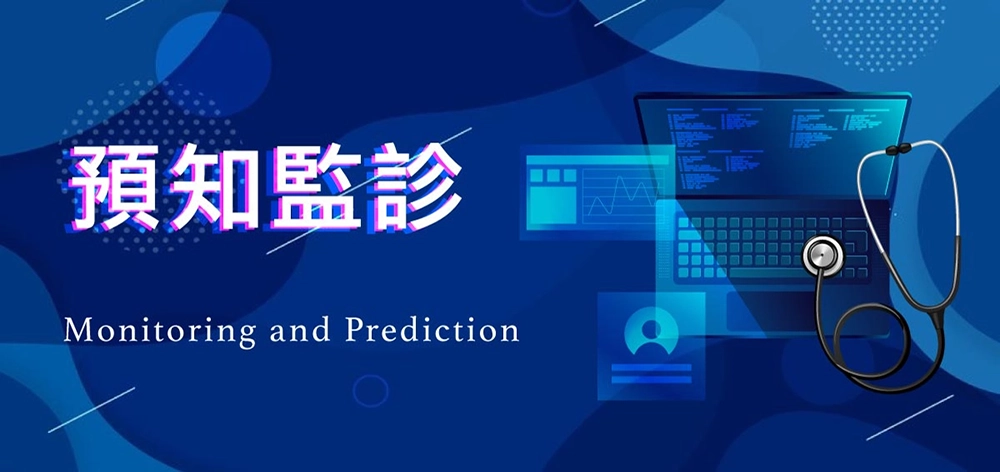
予知診断とスマート製造の関係
自動化設備と監視の両立
スマート製造に関して、次のような疑問を持つかもしれません:
自動化設備を導入すれば、それだけでスマート製造といえるのか?
製品の品質は向上しているのか?
設備の異常はいつ発生するのか? そしてなぜ発生するのか?
生産ラインのアップグレードにはすでに高額な費用がかかっているが、どうすればコストを削減できるのか?
どのようにして生産ラインの効率を継続的に改善できるのか?
現在の生産ラインはまだ使えるが、どのようにスマート機能を追加すればよいのか?
インダストリー4.0とスマート製造の時代において、各工場は競争力を維持するために自動化設備を積極的に導入しています。
しかし、多くの課題に直面することもあります。自動化設備は人の作業を代替しますが、機械自体は状態を伝えることができません。
予期せぬダウンタイムが発生した際には、すでに大きな損失が発生しているのです。
したがって、自動化設備の導入だけでは不十分であり、リアルタイム監視ソリューションを導入することで、生産ラインのスマート化プロセスを正確に把握する必要があります。
適切な予知診断計画を立てよう!
設備の状態を正確に把握
メンテナンスコストを削減するために、ユーザーは機器が深刻な問題を抱えたり、故障するまで部品の交換を行わないことがよくあります。
しかし、機械の故障を予測できなければ、製造ラインの停止、修理の遅延、部品調達の時間ロスが発生し、
それが高額なコストにつながるだけでなく、作業現場の安全リスクを引き起こす可能性もあります。
定期メンテナンスを実施しているユーザーでも、機器の故障リスクを大幅に低減できますが、
メンテナンスの実際の効果を正確に把握するのは難しく、過剰なメンテナンスが行われることもあります。
メンテナンス頻度が増えれば、その分コストも高くなります。多くの設備を管理する中で、
適切な点検や保守が行われているかを完全に把握するのは困難です。
もし設備が自ら現在の状態を通知したり、測定機器を活用して異常の原因を特定できれば、
突発的な故障や損失を防ぐことが可能になります。
予知保全
これは、ユーザーが設備の状態を正確に把握し、機器の信頼性を向上させ、突発的なダウンタイムのリスクを低減する ことを意味します。
不必要な定期メンテナンスや部品の過剰ストックを削減し、生産プロセスと調和させながら、
事前にメンテナンス計画を立てることで、機器の寿命を延ばし、メンテナンスコストを削減し、設備の稼働率と生産性を向上させます。
機器の信頼性
製品品質の一貫性
過剰メンテナンスの削減
精確な保守の実施
メンテナンス計画の策定
生産ラインの効率的なスケジューリング
機器の寿命延長
設備の利用率向上
予知保全を開始するには?
設備の状態を把握し、保全計画を立てる
予知保全と設備診断は密接に関連しています。
設備の状態を監視・診断することで、予知保全の計画立案が可能になります。
機械の振動特性を分析することで、設備の状態を評価できます。
監視システムを組み合わせることで、設備の使用特性に応じた定期的な監視や長時間監視を行い、
設備の状態に基づいて適切な判断やスケジュール調整を行うことができます。
これにより、生産効率の向上、異常の早期発見、設備寿命の予測、自動アラート機能によるユーザー通知が可能になります。
複雑な自動化プロセスでは、診断監視によって生産ラインの品質を安定させ、設備の信頼性を向上させることができます。
工場設備は複雑で多種多様ですが、どのように診断監視計画を立てるべきでしょうか?
長時間の監視が必要な設備が遠隔地にある場合、技術者が直接点検できない環境ではどのように監視すればよいでしょうか?
重要な生産ライン設備は高額で長時間稼働しますが、どのように重点的に監視すべきでしょうか?
工場の安全検査に不合格となった場合、より包括的な監視ソリューションが必要です。
保守後の設備は本当に効果があるのか?
品質管理において、製品の一貫性や内部機能が正常であるかをどのように確認すればよいでしょうか?
これらの課題は、設備診断の専門コンサルタントに任せることができます。
GoodTechは長年の測定経験を活かし、エッジコンピューティング技術を用いた設備に最適な測定ソリューションを提供します。
操作が簡単で、結果を直感的に判断できるため、ユーザーは設備の状態を把握し、保全計画を立て、生産性と品質を向上させることができます。
見落としがちな隠れたコスト
予知保全の重要性
予知保全の重要性を理解していますか? 予知保全を導入すれば、見落としがちな隠れたコストの削減に気付くはずです。
機械は使用時間や頻度によって徐々に摩耗していきます。
異常振動が発生し、製造品質に影響を及ぼすと、機械の効率が低下し、
生産効率(OEE)の低下 を引き起こします。
問題を早期に対処しなければ、設備の老朽化や早期引退につながる可能性があります。
製造中に発生する不良品もまた、隠れたコストの一種です。
多くのユーザーは設備のコストが高く、定期メンテナンスを行っているため、
設備が故障した時 にのみ修理すればよいと考えがちです。
しかし、予期せぬ生産ラインの停止が発生すれば、納期遅延や生産性の低下、人材リソースの無駄遣いなど、
かえって大きな損失を招く可能性があります。
工場内には多数の機械があり、ユーザーは機器を 保守点検 に送ることが多いですが、
本当に異常があるのかを確認しないまま過剰なメンテナンスを行うこともあります。
本来問題のない機器でも、保守スケジュールに従って無駄に点検され、
貴重な時間とメンテナンス予算を浪費してしまいます。
機器の保守点検を外部業者や社内の技術者が行う場合、
カスタマーサポートが部品交換を推奨 することがありますが、
実際には交換の必要がない場合もあります。
時には機械を完全に分解し、全ての部品を交換することもあり、
これが時間と労力の無駄につながります。
故障原因が特定され、特定の部品が必要になった場合、
それが海外からの取り寄せであれば、到着までの 修理遅延 が発生します。
また、修理完了後に設備が工場に戻った際、本当に効率が向上しているのか をどのように評価すべきでしょうか?
修理後も生産効率や設備稼働率が向上しない場合、それまでの全てのプロセスが無駄になってしまいます。
稼働率の低下
設備の異常故障
工場での保守点検
カスタマーサポート評価
部品調達の長期化
修理後の機械性能
予知診断ソリューションの計画をサポート
専門的な統合計画サービス
スマート製造の時代が到来しています。あなたは準備ができていますか?
製造工場では、設備部品から精密製造、生産、そして製品の最終組み立てに至るまで、
ただ製造効率を向上させるだけでなく、製品の歩留まりや出荷後のメンテナンスも考慮する必要があります。
インダストリー4.0の時代において、多くの中小企業や工場がスマート製造への移行に苦戦しています。
設備をアップグレードしたいが、予算が足りないとお悩みではありませんか?
工場内の測定計画をどのように進めればよいか分からないですか?
会社の規模拡大に伴い、新しい設備を導入する必要があるが、品質管理が難しいと感じていますか?
工場の設備は多種多様であり、一部は長時間の監視が必要であり、
他の設備は重点的な監視が求められたり、定期点検が必要な場合もあります。
これらの設備は、体系的に計画され、分かりやすい監視システムが必要です。
GoodTechは、工場管理、テクノロジー工場、生産製造工場、品質管理部門、FAB、SUB-FAB、
自動車製造、ロボットアーム、プレス加工業界 において、長年の測定経験を有しています。
エッジコンピューティングを活用し、様々な種類の多機能測定・監視システム、
機械学習、AI技術、IoTソリューションを開発しています。
当社の専門的な統合計画サービスを通じて、企業やユーザーがスマート製造の流れに適応し、
工場設備のアップグレードを実現し、生産性、品質、企業価値を向上させるお手伝いをいたします。
診断監視プロセス
工場内のさまざまな設備を効果的に管理
GoodTechは、工場全体の診断監視計画を提供します。
設備のトラブルシューティングに困っていますか?
あるいは、設備の異常の根本原因が特定できませんか?
そのような場合は、設備診断の専門家にご相談ください。
各種機械に対応した監視システムを導入することで、
工場設備の管理が強化され、機械の健康状態を把握し、
メンテナンス計画を事前に立て、設備寿命を予測することができます。
これにより、予知保全の実現が可能になります。
スマート製造へのアップグレードのために、多くの工場では自動化または半自動化設備を導入しています。
中小企業の多くは、一度にすべての設備を最新化することが難しいですが、
だからといって旧型設備を廃棄する必要はありません。
段階的なアプローチと人の経験を組み合わせることで、機械をスマート化することが可能です。
1 / 工場コンサルティング:ニーズの把握と問題の特定
設備の問題が製品の歩留まり低下や生産ラインの停止を引き起こしたり、
工場の環境設定が悪いために機械が損傷したり、安全リスクが発生する場合があります。
適切な解決策を見つけることが重要です。
2 / 評価と計画:工場レイアウトの評価とプラン作成
工場の配置や技術要件を評価し、経験を活かした最適なプランを提供します。
携帯型測定器、ワイヤレス監視システム、カスタマイズされた監視ソリューションなどを組み合わせた計画が可能です。
3 / 導入と開発:ソフトウェアおよびハードウェアの設計
ソフトウェア開発の支援や、各機械に適したハードウェアの設計、
データ収集の目的に応じたカスタマイズ、
さらに工場規格に準拠した設備の設置や配線工事を行います。
4 / テストと最適化:機能テストとアップグレード計画
設備の現場テストを実施し、エッジコンピューティングを活用してデータを収集・分析します。
そのデータに基づいて、さらなる診断計画を立案し、設備パラメータを調整し、
監視システムをアップグレードすることが可能です。
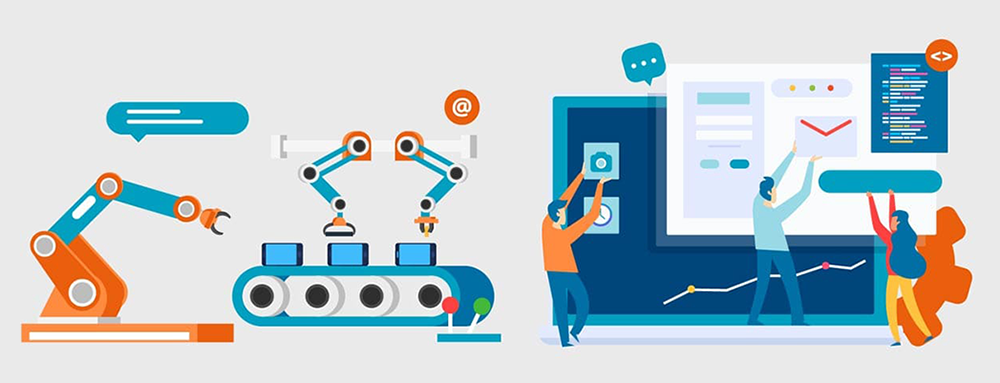