Seamlessly Connect to Intelligent Manufacturing?
FAQ|How to Build a Smart Manufacturing Site and Seamlessly Connect to Intelligent Manufacturing?From product development to human-machine collaboration, effective quality management is essential for intelligent manufacturing. To reduce production maintenance costs and improve production line efficiency, equipment intelligence is a key prerequisite for upgrading and transforming the manufacturing industry.
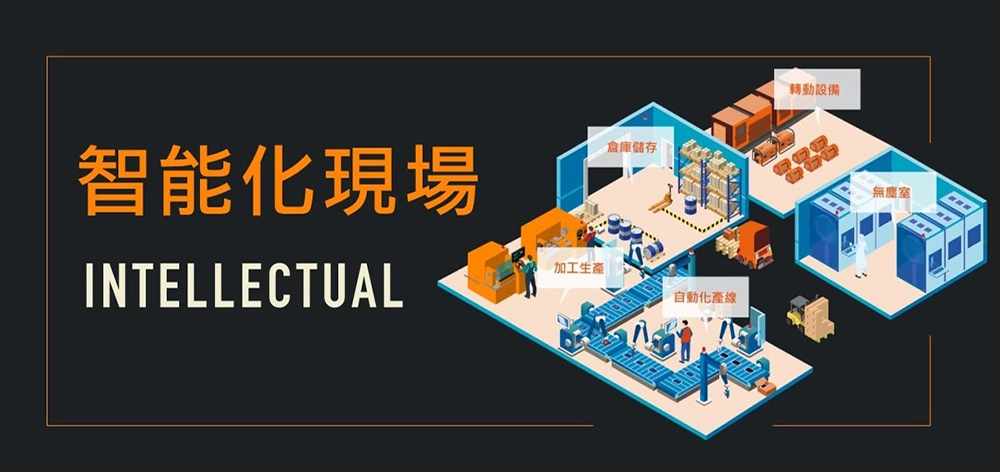
Introduction
The First Step in Smart Manufacturing
Building an Intelligent Manufacturing Site
Various aspects of smart manufacturing, such as production intelligence, equipment intelligence, energy management intelligence, and production supply management intelligence, can collectively be referred to as an intelligent site.
From product development to human-machine collaboration, effective quality management is essential for smart manufacturing.
Reducing production maintenance costs and improving production line efficiency are key objectives, with equipment intelligence serving as a crucial prerequisite for upgrading and transforming the manufacturing industry.
How can companies improve production line utilization, reduce loss rates, and ensure consistent product quality?
Achieving an intelligent site allows enterprises to integrate and monitor equipment, adjust machine quality based on equipment data, optimize production line processes through technical personnel, and unify data across the facility.
The first step in smart manufacturing is to plan an intelligent site, enhance equipment intelligence, and continuously monitor the smart manufacturing work environment and its details.
Common Challenges
What Problems Occur in Intelligent Site Management?
Want to Manage an Intelligent Site Effectively?
Do you want to reduce product loss rates? Are numerous rotating devices and rotor machinery difficult to monitor?
Do you need efficient machine management but struggle to identify equipment issues?
Are expensive CNC machines and robotic arms equipped with monitoring software that lacks essential features?
One of the key challenges in intelligent site management for smart manufacturing is that users often lack insight into equipment problems, leading to long-term operation in suboptimal conditions.
For example, improving product yield without real data as a reference is difficult—without identifying which production process causes product loss, process optimization becomes guesswork.
Some manufacturers wish to retain semi-automated production lines rather than rapidly replacing machines but still need practical solutions for intelligence enhancement.
When purchasing precision equipment, it is unclear whether vibrations from other machines will affect the production process.
Additionally, a single factory may have multiple machine types supplied by different vendors, resulting in independent, non-integrated machine data that cannot be used across systems.
Adopting Smart Manufacturing While Avoiding Long Implementation Times?
Gootech provides professional intelligent site management solutions tailored to different equipment, factory attributes, and budget timelines.
For complex and vast data information, our solutions simplify and visualize the data, making it easier for users to quickly assess site conditions.
Additionally, users can choose to retain raw data and flexibly use it for optimizing production process designs.
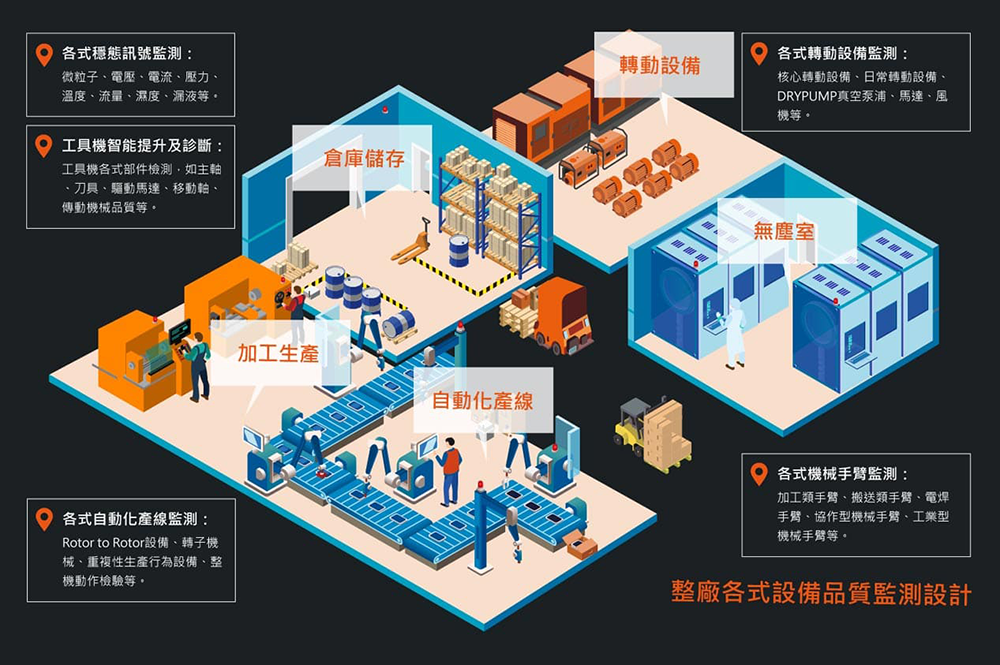
Implementation
1. The First Priority of an Intelligent Site: Smart Machinery
Smart Machinery – Intelligent Tool Machines
The manufacturing industry has played a key role in leading Taiwan’s economic miracle. With the arrival of Industry 4.0, despite ongoing industrial transformation, manufacturing remains the core of industrial upgrading.
Tool machines serve as a benchmark for a nation's manufacturing strength and represent one of the few industries in Taiwan that has developed its technology entirely independently.
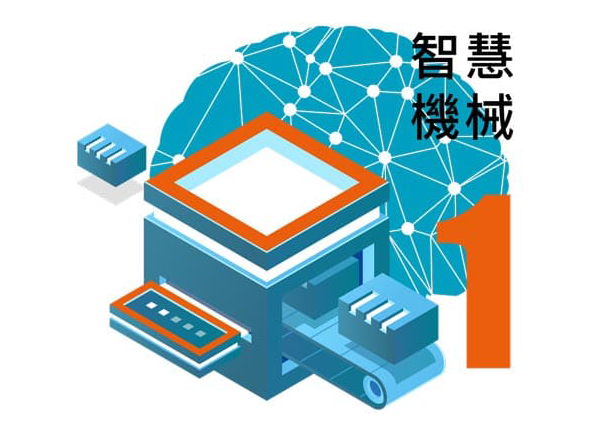
Taiwan ranks second in the world in per capita engineering machine output value, just behind Switzerland. As global industry trends evolve, the key focus for Taiwan’s tool machine enterprises is how to make machines smarter and create added value. Achieving smart machinery is the first step, followed by integrating it into an intelligent site, and ultimately extending it into smart manufacturing.
The era of Industry 4.0 has introduced smart machinery. Smart machinery integrates various intelligent technology elements, enabling traditional mechanical equipment to feature predictive maintenance, precision compensation, automatic parameter setting, and automatic scheduling. For small and medium-sized manufacturers, incorporating various sensors into tool machines to capture machine data can further enhance equipment utilization and strengthen the overall functionality of the machine.
VMS-PM Equipment Dynamic AnalyzerHow to Implement
2. The Backbone System of the Smart Factory: IIOT Industrial Internet of Things
Industrial IoT: An Essential Component of Smart Manufacturing
Smart manufacturing requires automation equipment in smart factories, which heavily relies on rotating equipment such as motors, pumps, and steam turbines. These traditional devices, in large numbers and various types, serve as the backbone of factory operations, playing a crucial role in manufacturing processes.
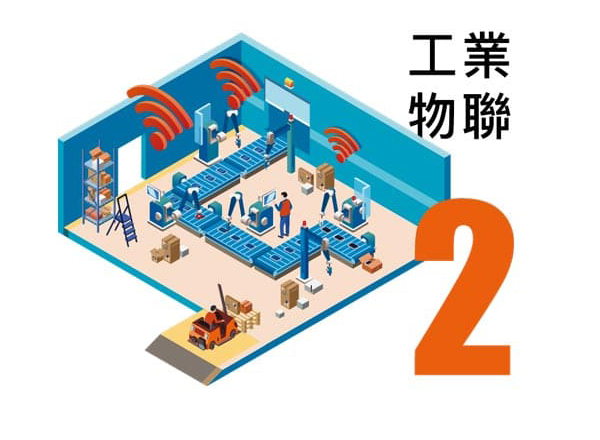
Factory inspection personnel often need to conduct routine inspections at specific times and locations. With the implementation of IIOT (Industrial Internet of Things) for remote monitoring, significant time savings can be achieved for inspection staff.
The system of a smart factory is complex, and for process monitoring, IIOT (Industrial Internet of Things) can be used to achieve comprehensive data integration and monitoring. IIOT (Industrial Internet of Things) not only allows predictive diagnostics based on accumulated database data but also enables predictive maintenance planning. This predictive diagnosis feature helps equipment manufacturers understand the equipment status, schedule maintenance, and prepare spare parts in advance. Additionally, for on-site safety and maintenance concerns, long-term monitoring and management can be implemented through Industrial IoT.
Infinite Industrial IoTHow to Implement
3. The Core of Smart Manufacturing: Machine Learning and AI
In the Industry 4.0 era, which is advancing rapidly alongside AI (Artificial Intelligence), industries face increasing demands for complex mechanical movements, streamlined production processes, improved efficiency, and consistent product quality. By leveraging high-performance measurement systems and AI-based analytics, manufacturers can quickly diagnose and resolve equipment issues.
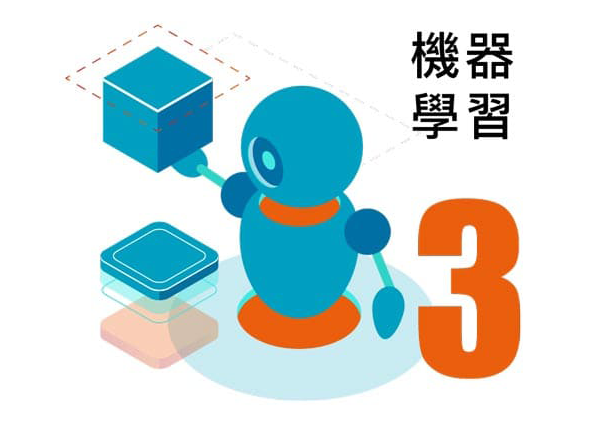
In the Industry 4.0 era, which is advancing rapidly alongside AI (Artificial Intelligence), industries face increasing demands for complex mechanical movements, streamlined production processes, improved efficiency, and consistent product quality. By leveraging high-performance measurement systems and AI-based analytics, manufacturers can quickly diagnose and resolve equipment issues.
The implementation of machine learning technology allows large amounts of data to be input into machines, which then analyze the data using specialized algorithms. This enables machines to learn, make judgments, or predict future events.
Issues related to identifying repetitive mechanical behavior can be addressed using the high-performance measurement capabilities of the VMS-ML Machine Learning Intelligent Monitoring System. By learning dynamic mechanical signals and providing AI-based computational parameters, product development and testing personnel can use the collected data for verification and validation tests. This helps optimize production line processes and improve efficiency.
VMS-ML Machine Learning Monitoring SystemSupporting Smart Factory Transformation
Digital Transformation Solutions
Many small and medium-sized traditional industries face challenges in upgrading and transforming their businesses. The main difficulties usually revolve around budget constraints and management issues.
Firstly, they lack the financial resources to invest in automated equipment. Secondly, they struggle with implementing data-driven management systems.
In the era of smart manufacturing, digital transformation is an inevitable path. But does digital transformation necessarily require a huge investment? Is there a simpler, more seamless solution for these resource-limited small and medium-sized enterprises?
EMS Smart Energy Management System
As companies face increasing demands to achieve carbon neutrality or emission reduction targets in their production processes to support global sustainability efforts, effective energy management has become a crucial component in achieving sustainable production goals.
Source: Online News, Taiwan Hydrogen & Fuel Cell Partnership, Tech Trends, Wikipedia