Suitable for Facility Management, Efficiently Managing Multiple Rotor
Why is it needed?
Reduce Annual Maintenance Costs
In the past, due to limited technology and experience, maintenance was often reactive—fixing equipment only after it failed.
This led to frequent breakdowns and frequent replacement of consumables.
Later, maintenance strategies evolved to include preventive maintenance, involving periodic replacement of worn-out parts and
scheduled inspections of critical components. However, this often resulted in excessive maintenance, leading to unnecessary waste.
In rotating machinery, vibration measurement is one of the most frequently used predictive maintenance techniques. The early stages of
failure in many rotor-based machines can be detected through time-domain or spectral analysis of vibration signals. When diagnostic
technologies and maintenance systems are effectively integrated, large numbers of rotating machinery can be maintained more efficiently
and accurately, preventing unnecessary maintenance and reducing budget costs.
Utilizing the IMS-PR Motor Rotor Inspection Analyzer allows for effective quality control of your extensive fleet of rotating
machinery.
Facility Challenges
Common Motor Management Issues in Facility Operations
Is Equipment in Good Condition?
Managing a large number of motor and rotor devices requires extensive inspection and measurement, consuming significant time. Compiling and analyzing the equipment's current condition can be highly complex and cumbersome.
How to Plan Maintenance Scheduling?
After compiling data, users rely solely on personal experience to plan maintenance schedules. This leads to inconsistent standards and a lack of strong, data-driven decision-making for equipment maintenance.
How to Determine Spare Parts Inventory?
When an issue arises, users often send equipment back to the manufacturer without understanding the root cause. This results in unnecessary part replacements and prolonged lead times for spare parts, making inventory management difficult.
Unexpected Downtime Causes Losses
Even with routine inspections, the inability to monitor real-time equipment status may result in unexpected shutdowns. This can disrupt production lines or affect product quality, leading to severe financial losses.
How to Solve
Effectively Improve Inspection Efficiency
Users can create customized inspection maps based on industry or facility needs.
Built-in comprehensive rotor classification with ISO recommendations for automatic condition assessment.
Users can name and assign multiple measurement points for motor rotors or pumps.
Inspection map for clear equipment status analysis, historical reports, measurement summaries, and trend tracking.
Easily create rotor inspection maps with simple steps, no technical background required.
Portable measuring instruments with IP65-certified industrial waterproof and dustproof protection.
Feature Description
Create a Customized Inspection Map for Rotor Equipment
IMS-PR Motor Rotor Inspection Analyzer is specifically designed for rotor equipment, incorporating measurement functions tailored to their unique requirements. Users can categorize and create custom maps based on facility layout and equipment attributes, assigning different numbers of measurement points per device.
The system provides real-time equipment status display on the map, using indicator lights to assess quality conditions. This feature helps users plan and schedule timely maintenance and servicing.

Feature Description
Suitable for Predictive Maintenance of Various Motor Rotors
IMS-PR Motor Rotor Inspection Analyzer utilizes vibration measurement signals to evaluate the health status of motors, making it suitable for quality assessment of various motors, pumps, and other equipment. Facility personnel can use trend charts and numerical data to assess equipment conditions, enhancing the efficiency of maintenance and servicing.
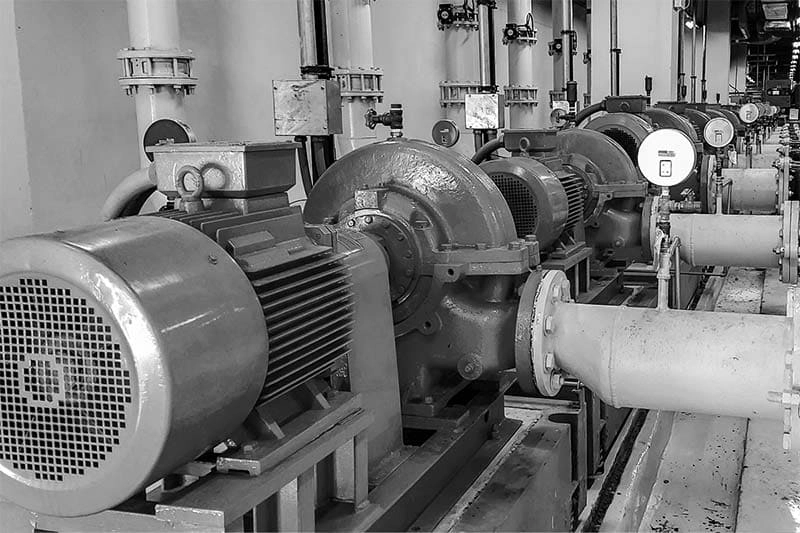
Feature Description
Built-in ISO Vibration Reference Standards
IMS-PR Motor Rotor Inspection Analyzer defines equipment status based on ISO vibration standards, categorizing conditions into four levels: Excellent, Normal, Warning, and Dangerous. Measurement results are displayed instantly, providing users with clear insights without waiting for an inspector to arrive. This enables immediate issue resolution and helps users establish their own internal equipment health management standards.
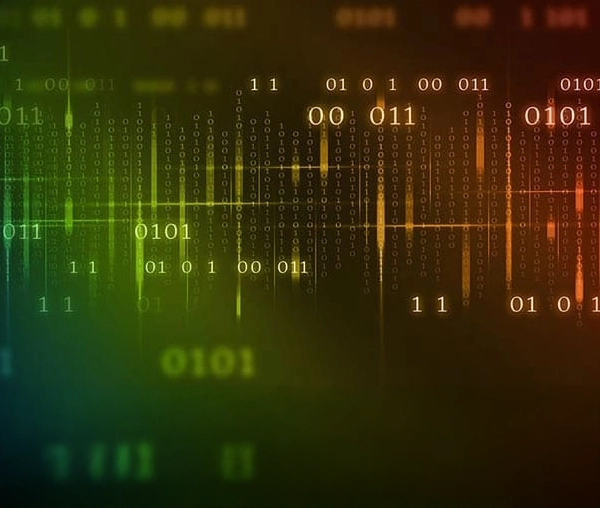
Additionally, Goodtech leads the market by integrating the latest ISO 20816 standard, offering a more comprehensive management system for motor rotor components.
Feature Description
Portable & Intuitive Touch Interface for Easy Operation
The portable IMS-PR Motor Rotor Inspection Analyzer allows on-the-spot measurements anywhere. Simply select the appropriate standard based on the equipment's wattage and size, and testing can be performed with ease—no specialized expertise required.
With just a few simple steps, key monitoring points for motor rotors in the facility can be classified and managed efficiently, making equipment management faster and more convenient.
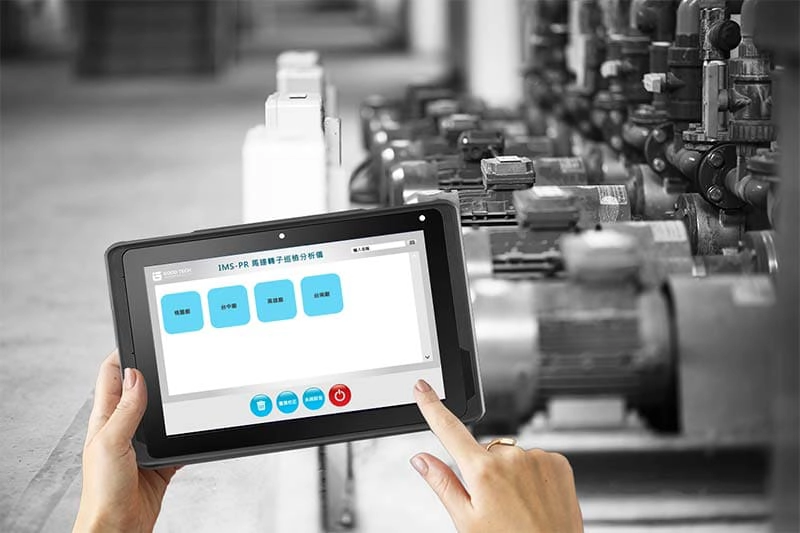
Effectively Prevent
Unplanned Downtime
With a large number of motor rotor devices in operation, implementing proper inspection and maintenance procedures can effectively prevent the losses and risks caused by unplanned downtime. Additionally, it can lead to significant cost savings in maintenance budgets.
Function Description
UI Interface Screens
Instantly Understand the Health Status of Motor Rotors
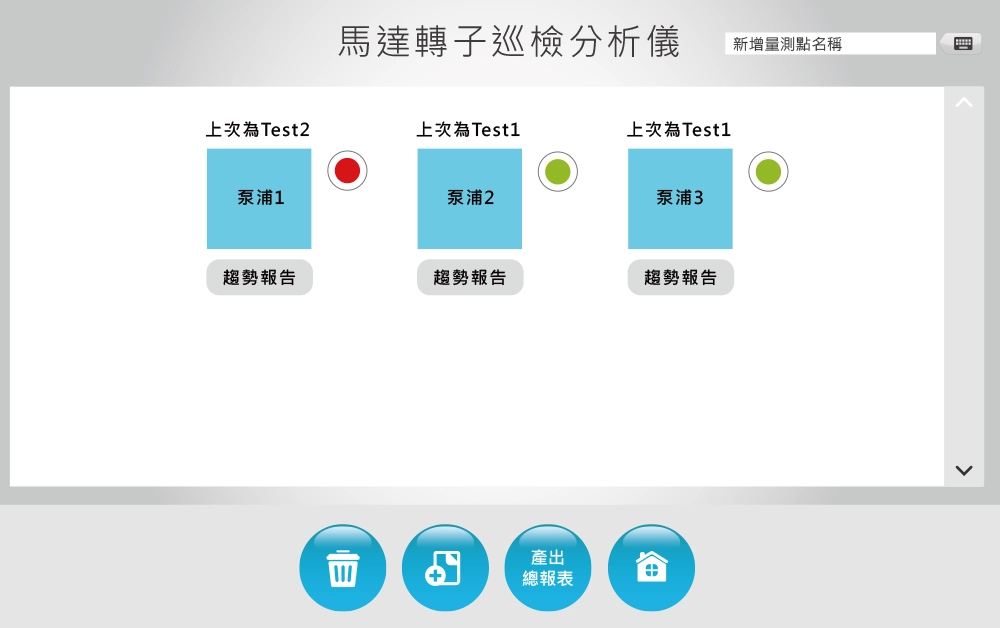
IMS-PR Motor Rotor Inspection Analyzer displays the health status of motor rotors using signal indicators: Red Light: Abnormal / Green Light: Normal. Users can react in real time and make maintenance decisions accordingly.
Vibration Quality Evaluation Method
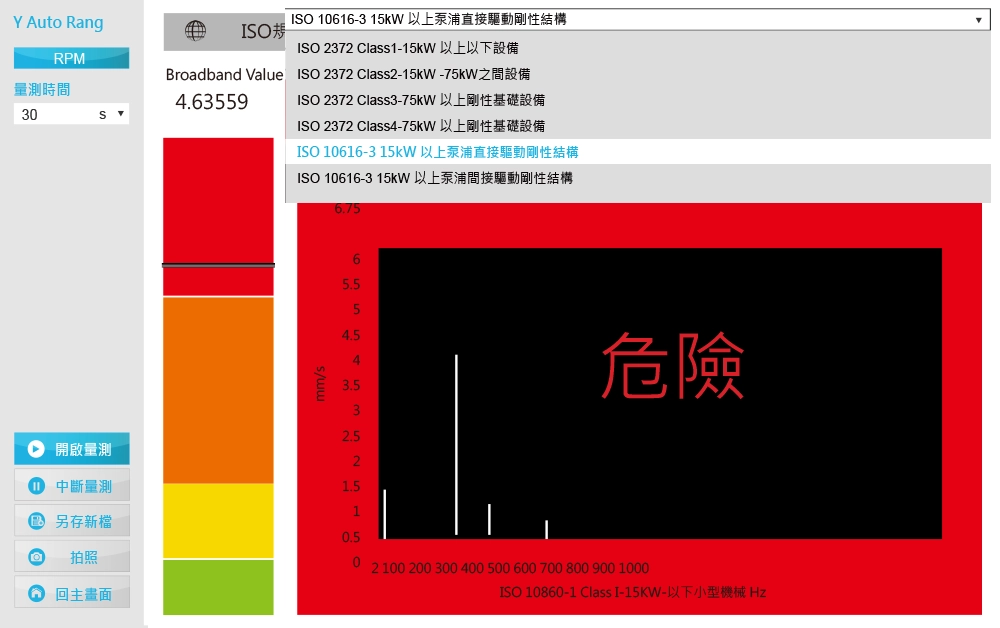
1. Based on existing measurement benchmarks, mechanical vibration variations serve as the quality criteria
Zone A - Excellent (New Machine) Newly manufactured machinery with excellent vibration quality and no specific time limitation.
Zone B - Normal Machine Acceptable vibration levels, allowing long-term use with no specific time limitation.
Zone C - Warning State Not suitable for prolonged use; maintenance and repairs should be scheduled appropriately.
Zone D - Danger State Abnormal vibration levels that could lead to machine damage; immediate repair is recommended.
e.g.: For a category of 300KW-50MW motors with a shaft height of ≥315mm and rigid structure, the upper limit for Zone B is 4.5mm/s. Therefore, the quality threshold value is: standard value (previous stable measurement) ± (4.5mm/s) x 25%.
2. If there are no prior measurement values, start with the suggested "Zone 1" standard measurement, then establish a measurement benchmark
Machine warning thresholds must not exceed the Zone C standard of the respective category.
If exceeding Zone C, follow the recommended "1" approach for maintenance and repairs.
Each measurement using this evaluation method should place the sensor at the same test point for accuracy.
There must be prior measurement values as a benchmark. Subsequent periodic measurements at the same test point must not exceed the specified variation Δ. [Variation Δ: 25% of the Zone B upper limit value for the respective category]
Report Visualization
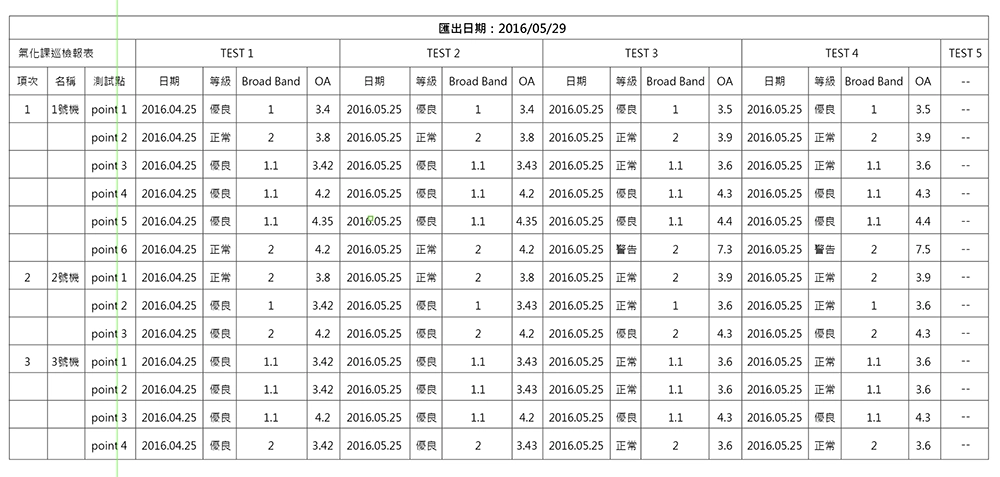
A lightweight touchscreen interface simplifies operation. The system is specifically designed for motor rotor measurement functions, enabling plug-and-play measurements. Convenient for inspection personnel to carry, with real-time display of measurement results on a tablet screen.
Usage Process
Brief Setup Guide
IMS-PR Motor Rotor Inspection Analyzer allows users to create inspection maps independently. With just a few steps, motor rotors in the facility can be categorized and managed efficiently.
1. Create a Map
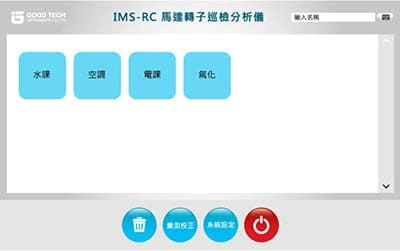
2. Set Up Inspection Points
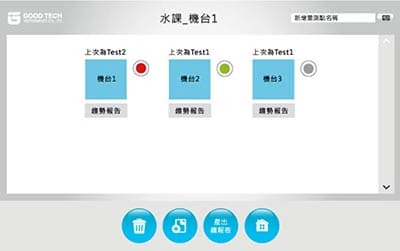
3. Define Measurement Points
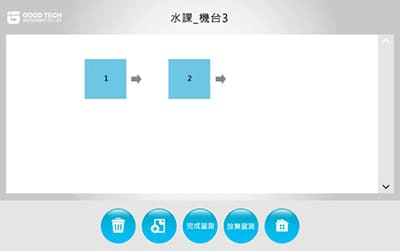
4. Measurement Display
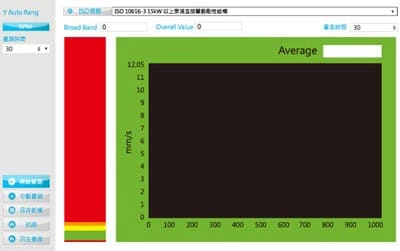
5. Select the Corresponding Standards
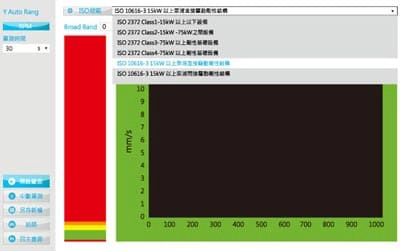
6. Obtain Equipment Results
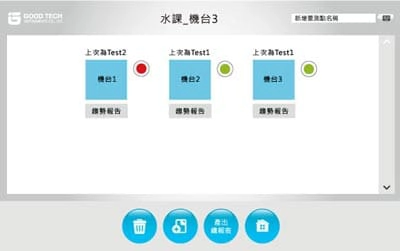
Benefits
Instant Feedback
IMS-PR Motor Rotor Inspection Analyzer features a lightweight touchscreen with a user-friendly interface. The system is designed specifically for measuring motor rotor performance, offering plug-and-play functionality for convenient on-the-go inspections. The tablet screen instantly displays equipment status and diagnostic results. It provides users with precise maintenance instructions and predictive maintenance insights, helping improve maintenance planning efficiency, preventing unexpected production line shutdowns, and reducing unnecessary maintenance costs.
Quick to Learn
Equipment Control
Precision Maintenance
Enhanced Efficiency
Prevent Downtime
Reduce Costs
Application
Target Users
In-house Facility Management Department:
Responsible for equipment maintenance/regular inspections, replacing subjective human judgment with data-driven evidence.
Facility/Equipment Engineers:
Verify equipment condition and provide data support when requesting repairs.
Outsourced Equipment Maintenance Contractors:
Contractors managing plant equipment maintenance and providing periodic inspection services.
Equipment Manufacturers:
During scheduled maintenance, identify equipment issues and assist customers with repairs/replacements while keeping records.
Equipment Repair Service Providers:
Provide repair diagnostics and offer regular inspection services for customers.
Application
Target Equipment
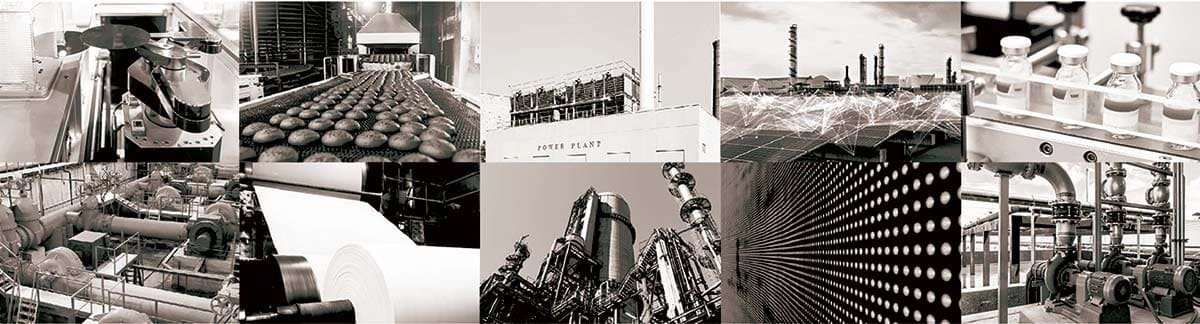
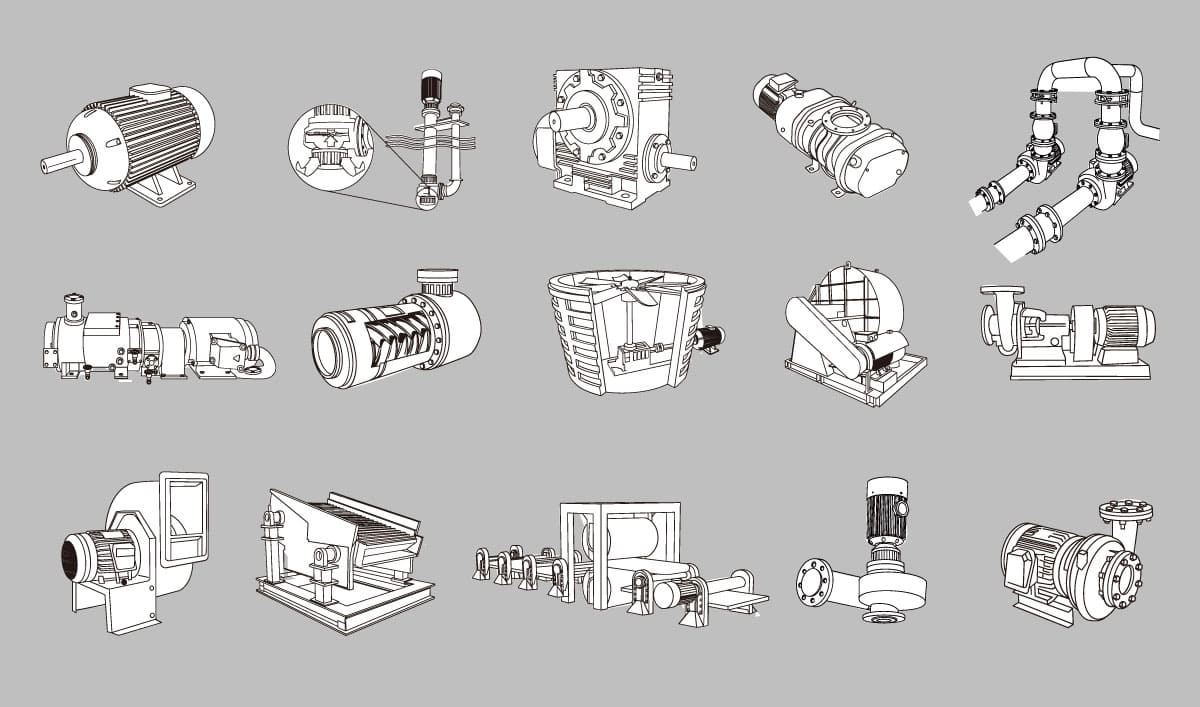
Application Fields:
Semiconductor industry, petrochemical plants, food factories, pharmaceutical plants, paper mills, panel factories, LED factories, power plants, pumping stations, wastewater treatment plants, manufacturing, equipment manufacturers, maintenance service providers, etc.
Target Equipment:
Pumps and Vacuum/Water Extraction Equipment: Vacuum pumps, oil pumps, sewage pumps, etc.
Production Machinery: Machine tool spindles, cutting machines, etc.
Air Compressors: Screw-type, centrifugal, reciprocating air compressors, etc.
Others: Cooling towers, exhaust fans, air handling units, etc.
Specifications
Perfect Integration of Hardware, Electrical, and Software
Equipped with a USB interface for easy measurement data storage, featuring full-touch input and a 10-inch full-color screen for real-time measurement data and calculation results display. Compact and lightweight, allowing users to conveniently carry it to on-site environments for measurement. Expandable camera functionality enables effortless storage of measurement environments. Certified with an IP65 international protection rating for water and dust resistance.
Support
Other Rotor Equipment Related Topics