Is Managing Rotating Equipment in Facilities Difficult?
Application Field | FacilitiesFrom equipment components to precision manufacturing and final product assembly, improving manufacturing efficiency is essential. However, product yield rate and post-shipment maintenance should also be considered.
Motivation
Unsure Where to Start with Facility Equipment Management?
The era of smart manufacturing is here—are you ready?
From equipment components to precision manufacturing and final product assembly, improving manufacturing efficiency is crucial. However, product yield rate and post-shipment maintenance should also be considered.
With Industry 4.0, many small and medium-sized enterprises (SMEs) and factories still struggle with planning for smart equipment. Do you wish to upgrade your equipment but find the budget insufficient? Are you unsure how to plan in-factory measurement systems?
As your company expands and new equipment is introduced, how do you ensure quality control?
Managing a Large Volume of Rotating Equipment is Challenging?
Factories have a wide range of rotating equipment, with large quantities requiring measurement, consuming significant time. How can we efficiently measure and manage a large number of devices?
There is often a massive number of rotating equipment in factories, such as
exhaust fan motors, compressor motors, high-voltage motors, vacuum pumps, and water supply pumps.
Although dedicated engineers handle inspections, it often takes an entire day to cover the whole factory, yet measurements remain incomplete.
Additionally, in facility management, expensive rotating equipment is commonly used for precision manufacturing, where long lead times, continuous production, and strong correlations between equipment and product quality make diagnostics even more critical.
How to Implement
How to Plan and Monitor Various Rotating Equipment?
Facility systems vary by industry and can generally be categorized into process cooling water systems, exhaust gas reduction systems, ultrapure water systems, wastewater treatment systems, gas supply systems, process vacuum systems, power monitoring systems, and more. These systems can be further classified into four main types: daily rotating equipment, hard-to-maintain rotating equipment, rotating equipment in special environments, and critical rotating equipment.
Daily Rotating Equipment in Facilities
Examples: Various water and power supply motors, pumps, etc. These are large quantities of rotating equipment that are relatively easy to back up. However, factory personnel must spend a significant amount of time and manpower inspecting these machines.
Large Rotating Equipment with High Safety Risks
Rotor pump equipment is often placed in scattered locations or areas difficult for personnel to access. Additionally, extremely large equipment is hard to maintain, increasing the burden on inspection personnel.
Critical Rotating Equipment in Facilities
These are key machines in the factory, often expensive, and used for precision manufacturing. They have long procurement lead times, must remain operational at all times, and have a significant impact on both product quality and production.
Rotating Equipment in Special Environments
These machines operate in extreme conditions such as high temperature, high pressure, or chemical environments. Examples include vacuum system pumps in FAB/SUBFAB facilities and exhaust ventilation systems.
Implementation Challenges
How to Perform Predictive Diagnostics for Daily Rotating Equipment?
A Large Number of Motors and Pumps
For daily rotating equipment in facility management, traditional inspection methods involve personnel patrolling the plant, noting anomalies on paper records, and then forwarding them to maintenance or engineering departments after organizing the data.
This process is time-consuming and prone to errors.
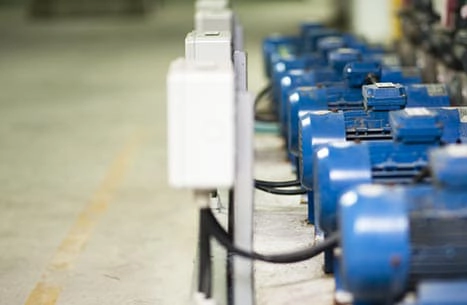
Managing numerous motor rotor devices is challenging, and inspection personnel often spend extensive hours measuring equipment. Additionally, the maintenance budget allocated annually for facility rotors—such as exhaust fan motors, compressor motors, high-voltage motors, vacuum pumps, and water supply pumps—is a considerable expense.
Execution Goals
Predictive Diagnostics for Daily Rotating Equipment
# Prevent Unexpected Failures and Reduce Downtime Losses
A large number of motors and pumps are at risk of unexpected failures. Daily rotating equipment operates continuously, and any unexpected shutdown can significantly impact factory production.
For example, if a compressor motor fails, it may simply cause the air conditioning system to stop, but in severe cases, it could lead to a complete production halt.
# Reduce Excessive Maintenance and Lower Annual Maintenance Costs
Many factories establish maintenance schedules based on the equipment's installation date rather than its actual condition. Since facilities contain numerous rotating devices, companies often allocate a large annual maintenance budget for inspections and repairs.
However, due to a lack of real-time equipment status monitoring, some parts may be replaced even when they are still in good condition, leading to unnecessary waste.
# Verify Repaired Equipment and Control Outsourced Maintenance Quality
Frequent issues arise where a repaired component fails again shortly after being returned, requiring another repair cycle. This repetitive process wastes both time and money.
Is the performance of the repaired rotor equipment better than before? If so, by how much? Is outsourcing maintenance truly cost-effective?
These questions often trouble factory management.
# Analyze Failure Causes and Ensure Precise Repairs
Factory maintenance personnel often face challenges when repairing different machine models. Traditional troubleshooting methods involve disassembling the entire machine and inspecting each component individually.
In some cases, a minor issue may take an entire workday to diagnose, and reassembling the machine perfectly is not always guaranteed.
Understanding the root cause of failures allows maintenance staff to execute repairs more efficiently.
Prevent Unexpected Failures
Reduce Excessive Maintenance
Verify Maintenance Effectiveness
Analyze Failure Causes
How to Implement
Daily Rotating Equipment
Now, with IMS-PR Motor Rotor Inspection & Analysis Device, managing a large number of rotating equipment is easier than ever! It significantly reduces the time required for facility inspections.
The IMS-PR analyzer allows users to create customized inspection maps based on industry-specific needs. Motors, rotors, or pump points can be named directly, making it more user-friendly and practical. The portable design enables convenient use, while the system directly identifies abnormal vibrations, maintenance-required statuses, and quality conditions on the inspection map.
IMS-PR Motor Rotor Inspection & Analysis DeviceMeanwhile, SMS-RC Rotating Machinery Vibration Analyzer can quickly identify the causes of equipment abnormalities, allowing inspectors to make immediate and accurate maintenance decisions.
SMS-RC Rotating Machinery Vibration Analyzer
Implementation Challenges
How to Monitor Large Rotating Equipment with Safety Risks?
Motors and Pumps Installed Outdoors
Facility inspection personnel must check a large number of motor rotor devices one by one.
Even inspecting equipment inside the factory already consumes a significant amount of time and manpower.
When it comes to motors and pumps installed in remote outdoor areas, inspections become even more labor-intensive.
Furthermore, when equipment fails, operators often find themselves unprepared for immediate action.
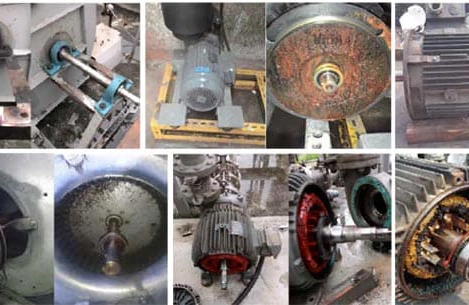
For facility management, a long-term online monitoring system is essential to continuously track equipment conditions. The system should provide real-time alerts when abnormalities occur, notifying users immediately. Additionally, large rotating equipment with high safety risks significantly impacts the overall safety of the facility. By implementing an automated monitoring system, factories can standardize inspection protocols, establish routine maintenance workflows, and ultimately enhance workplace safety while reducing unexpected risks associated with equipment failures. By detecting abnormalities in real-time and sending instant warnings, the system can immediately alert operators in an intuitive manner, effectively preventing workplace safety hazards.
Implementation Goals
Ensuring the Quality of Large Rotating Equipment with Safety Risks
# Prevent Unexpected Failures and Reduce Downtime Losses
Motors, pumps, and other rotating equipment in facility management are particularly vulnerable to unexpected failures.
Moreover, their locations are often scattered, far from the user’s operation area, or placed in environments where dust accumulates easily, increasing the risk of malfunction.
If failures occur without timely detection, the entire facility’s operation may be affected.
# Online Monitoring for Hard-to-Inspect Equipment
For motors, high-altitude equipment, and other hard-to-reach machinery, online monitoring provides a more convenient way to track system conditions remotely.
Since changes in rotating equipment conditions are often subtle, long-term monitoring is necessary to analyze trends, estimate lifespan, and schedule maintenance plans accordingly.
# Real-Time Equipment Monitoring and Alert Notifications
Through a visualized screen interface, the status of motors and pumps can be displayed clearly, allowing for the centralized management of multiple rotating machines.
When abnormalities occur, warning indicators appear, and notifications can be sent via LINE, email, or smart mobile devices to ensure that the status is monitored at all times.
# Flexible Expansion with Lower Wiring Costs
In an ideal scenario, facility planning would be implemented all at once. However, in reality, businesses must consider budget constraints, cost-effectiveness, and phased implementation.
To accommodate this, a flexible system design is essential, allowing for gradual expansion while leveraging wireless technology to significantly reduce wiring and installation costs.
By minimizing infrastructure costs, both technical and financial efficiency can be optimized.
Prevent Unexpected Failures
Online Monitoring for Equipment Status
Send Abnormal Alerts
Flexible Expansion
How to Implement
Rotating Equipment with Safety Risks
For facility rotating equipment that is difficult to maintain due to safety concerns, a Wireless Rotor Health Monitoring System can be utilized. Users can adjust the email alert notification timing as needed. This system helps reduce wiring costs and space usage across large industrial areas.
It features temporary memory storage to prevent data loss and uses the MQTT communication protocol. Additionally, it allows enterprises to implement wireless monitoring across facilities, integrate all data into a unified system, and visualize information in a clear and simple manner for users.
RM-IoT-B Wireless Rotor Monitoring System (Battery-Powered)
Implementation Challenges
How to Perform Diagnostics on Critical Rotating Equipment?
Directly Impacts Production Line and Product Quality
Critical rotating equipment in facility management is often expensive and serves as a key component in primary production lines.
These machines need to operate continuously, and their procurement lead times can be long.
Therefore, such equipment requires specialized monitoring and real-time condition tracking.
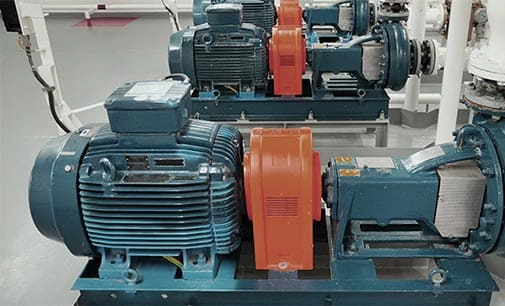
If a motor or rotor device experiences failure and stops working, it will significantly impact the production line, product yield rate, material loss rate, and overall production capacity. To maintain stable quality, most facility managers utilize dedicated monitoring systems** for motors, pumps, and rotating equipment.
Implementation Goals
Ensuring the Quality of Critical Rotating Equipment
# Long-Term Online Monitoring to Reduce Production Line Variability
Critical rotating equipment in facility management directly affects product quality on the production line.
During operation, abnormal vibrations and rotational issues can impact the manufacturing process.
Thus, continuous long-term monitoring is necessary to minimize variations in the production process
and ensure smooth operation of the production line.
# Extend Equipment Lifespan with Clear Maintenance Scheduling
Critical rotating equipment is often expensive, with long procurement lead times and high material costs.
Unplanned downtime for maintenance can negatively impact production efficiency.
By accurately assessing equipment quality, proactive maintenance planning can be implemented to
**avoid disruptions** during production, ultimately extending the lifespan of core rotating equipment.
# User-Friendly Software for Instant Quality Assessment
The software system must be intuitive and easy to operate, allowing facility personnel—
even those without technical expertise—to quickly understand the quality of motors and pumps.
It should provide real-time measurement data, automatic vibration analysis, historical data storage,
and report generation. Additionally, instant alerts should notify users of any equipment abnormalities
to ensure timely decision-making.
# Continuous Data Collection for Reliable Original Data
Critical rotating equipment requires continuous, uninterrupted monitoring to accumulate anomaly characteristics
and convert them into trends for more precise decision-making.
Furthermore, the raw data collected can serve as a foundation for future AI model training.
Long-Term Online Monitoring
Extend Equipment Lifespan
Instant Status Assessment
Provide Useful Data
How to Implement
Critical Rotating Equipment
For expensive rotating equipment in facility management—where long procurement times, non-stop operation requirements, and direct impact on product quality are critical factors— the RM-IoT-Online Rotor Health Management System can be used for monitoring. It offers long-term online monitoring capabilities, allowing users to analyze quality trends through trend charts and further evaluate rotor health conditions via graphical analysis. This enables predictive maintenance, proactive servicing, and the prevention of unexpected shutdowns.
Additionally, the system can be integrated with IMS-PR Motor Rotor Inspection & Analysis Device to create inspection maps for routine inspections. Alternatively, SMS-RC Rotating Machinery Vibration Analyzer can be used to analyze the root causes of rotor equipment abnormalities.
RM-IoT-Online Rotor Health Management System
Implementation Challenges
How to Diagnose Rotating Equipment in Special Environments?
Rotating Equipment Operating in Extreme or Hazardous Industrial Environments
Some rotating equipment in special facility areas operates under extreme or hazardous industrial conditions,
placing higher demands on monitoring and maintenance.
These requirements include safety, reliability, durability, and adaptability to specific environmental conditions.
When designing, installing, and operating such equipment, it is crucial to comply with relevant safety standards and regulations.
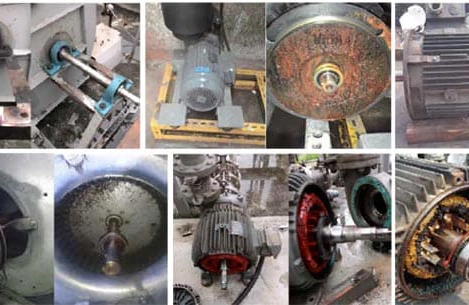
Special environments such as chemical plants, submerged applications, high-temperature and high-pressure areas, explosion-prone zones, and corrosive media environments require additional measures to ensure safe operation and equipment reliability. In addition to strict and challenging monitoring procedures, suitable specialized sensors that meet environmental standards and requirements must be used to carefully execute monitoring tasks.
Implementation Goals
Rotating Equipment Quality in Special Environments
# Adapt Different Sensors Based on Environmental Conditions
In special facility areas such aschemical plants, submerged applications, high-temperature and high-pressure zones, explosion-prone areas, and corrosive media environments,
the Rotor Health Monitoring System must be equipped with sensors tailored to these conditions.
For example, dustproof, explosion-proof, high-temperature resistant, and waterproof sensors may be required.
# Compatible with Various Equipment, Allowing Manual Threshold Configuration
Rotating equipment in special environments comes in a wide variety of types.
Beyond basic monitoring and management, the system should allow users to set custom quality thresholds based on experience,
ensuring that monitoring aligns precisely with each piece of equipment’s specific quality requirements.
# Simple Expansion, Simultaneous Monitoring Across Multiple Areas
The software system must be easy to use and expand,
allowing facility personnel without technical expertise to quickly deploy, configure, and understand equipment quality data.
Additionally, the system should provide real-time measurement data, automatic vibration quality assessments, and other critical insights.
# Centralized Control with Instant Alert Notifications
Given that rotating equipment in special environments is often dispersed across large areas,
the system must centralize management and monitor multiple devices simultaneously.
In the event of abnormal conditions, the system should provide instant alerts,
ensuring that users can promptly detect and resolve potential failures.
Adapt Different Sensors
Manual Experience-Based Settings
Easy Expansion & Deployment
Centralized Command Center Management
Implementation Goals
Rotating Equipment in Special Environments
Rotating equipment in special environments presents greater monitoring challenges, and its stability directly affects production line operations and product quality. The RM-IoT-NET Networked Rotor Health Monitoring System helps users ensure equipment stability and reliability, thereby securing stable production lines.
This system employs daisy-chain network topology, where the main system connects up to 255 nodes via RJ45 network cable modules. Additionally, it supports AI, FDC, MES, PHM, and SCADA system integration, offering high connectivity flexibility while reducing system connection costs. This scalable solution optimizes space utilization and budget allocation.
RM-IoT-NET Rotor Health Monitoring SystemSupport
Other Rotor Equipment-Related Topics