Smart Monitoring Solution for Power-Consuming Equipment
Solutions|Smart Monitoring Solution for Power-Consuming EquipmentThere is a close relationship between ESG and corporate power consumption equipment. Energy usage and carbon reduction goals are key indicators in ESG evaluations.
Reasons for Implementation
The Relationship Between ESG and Power-Consuming Equipment
Improving ESG Performance Through Power Equipment Optimization
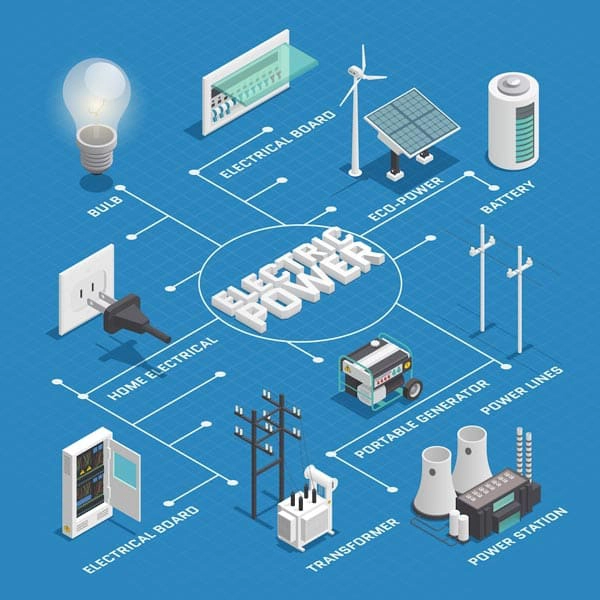
ESG stands for Environmental, Social, and Governance, and it serves as a key standard for evaluating a company’s sustainability performance.
There is a close link between ESG and corporate power-consuming equipment. Energy usage and carbon reduction goals are crucial indicators in ESG evaluations.
If the power-consuming equipment used by a company improves energy efficiency and reduces energy waste, its environmental and social impact will be minimized, leading to improved ESG performance.
Therefore, companies should focus on their ESG performance and enhance it by optimizing power equipment usage.
This approach benefits both the company’s sustainable development and aligns with societal and environmental expectations.
Implementation Benefits
Managing Power-Consuming Equipment from the Source
With ESG investments becoming increasingly widespread, companies should regard power-consuming equipment management as a key element in achieving sustainable development goals.
By adopting energy-saving and carbon reduction measures, businesses can lower electricity consumption and carbon emissions.
This can be achieved by replacing outdated equipment with high-efficiency alternatives, installing energy-saving devices, and optimizing energy usage timing.
Additionally, companies should establish a comprehensive energy management system, enhance energy monitoring and control, and promote energy-saving awareness among employees.
This approach not only reduces operational costs and increases competitiveness but also aligns with societal expectations, actively supporting ESG initiatives and achieving sustainable development goals.
Implementation
Key Areas for Monitoring Power-Consuming Equipment
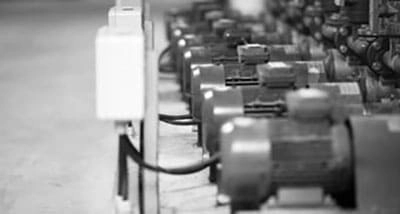
Production Equipment
Production equipment (such as motors and machining tools) accounts for a significant portion of electricity consumption.
By monitoring vibration levels, companies can assess equipment condition, implement predictive maintenance, improve efficiency, and prevent unnecessary operation.
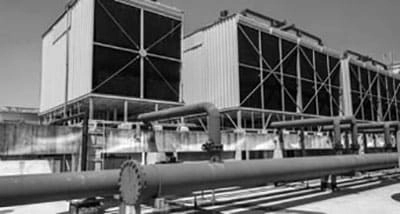
HVAC Systems
HVAC systems (such as central air conditioning, compressors, and industrial refrigeration units) are among the largest energy consumers.
Monitoring current and vibration levels helps assess equipment quality, usage duration, and energy consumption.
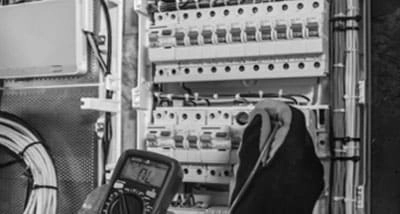
Power Distribution Systems
Power distribution systems (such as transformers and distribution panels) transmit electricity from supply stations to various electrical devices.
Monitoring current and power consumption allows for better management of energy distribution and usage.
Execution Challenges
Diverse power equipment data makes effective management difficult?
Power-consuming equipment, such as various HVAC units, motors, compressors, and production line machinery, comes in different units and formats. Additionally, different equipment requires different inspection cycles. Recording and managing this data manually can be a major burden for inspection personnel. A comprehensive system that integrates data management is essential.
Implementation
Flexible Inspection Mode
High-Freedom System for Asset Management
IMS Industrial Monitoring & Inspection System offers a flexible architecture that allows users to add management areas freely, set equipment inspection cycles, and define upper and lower parameter limits. It is suitable for all types of equipment and is particularly ideal for small and medium-sized enterprises with limited budgets or those in an expansion phase. Additionally, it supports paperless data management, improving overall efficiency.
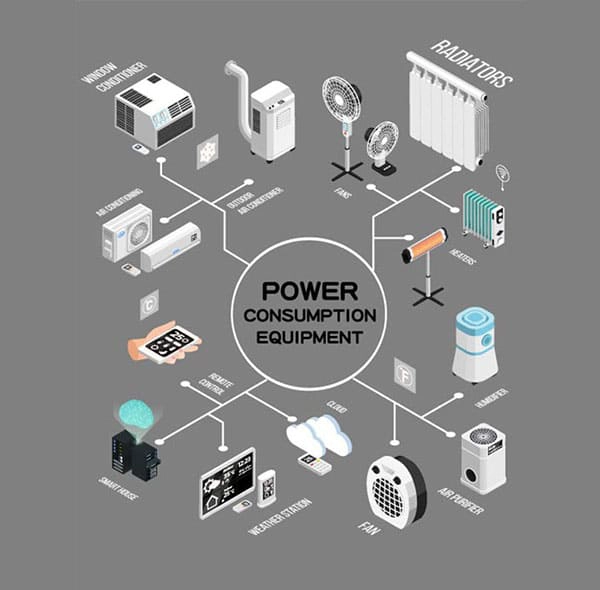
Execution Challenges
Difficulties in inspecting equipment due to accessibility or large-scale systems?
Some power-consuming equipment, such as cooling towers, compressors, and fans in HVAC systems, is often located outdoors at high altitudes or consists of large-scale installations. This makes regular inspections challenging, preventing timely issue detection. Moreover, the risks involved in inspecting such equipment can pose serious safety hazards for workers, potentially leading to workplace accidents and compliance issues.
Implementation
Challenges of Manual Inspections and Wiring
Wireless Sensing for Efficient Inspection Planning
RM-IOT-B Online Monitoring System replaces manual inspections by using sensors to collect equipment data, enabling real-time monitoring of equipment conditions. It is suitable for various motor and pump systems, providing instant status assessment of the equipment. The system integrates a three-axis wireless accelerometer and utilizes a low-power LoRa transmission method, supporting up to 25 different measurement parameters for monitoring. By leveraging trend analysis, preventive maintenance can be scheduled in advance, reducing unexpected downtime and minimizing equipment downtime.
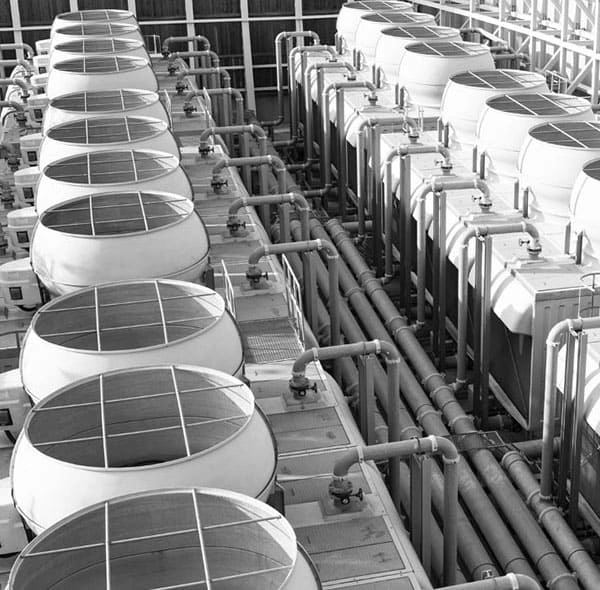
Challenges
Inefficient Equipment Running Continuously, Leading to Energy Waste?
Motorized equipment used in daily production, due to its large quantity in factories, often operates inefficiently when its condition is not properly monitored. This results in unnecessary energy waste and increased carbon emissions, negatively impacting the environment.
Implementation
Establishing a Dedicated Control Room
Real-Time Factory Monitoring
By utilizing IIOT, real-time data can be displayed, enabling centralized monitoring of all equipment conditions. When an issue arises, immediate maintenance or part replacement can be performed, reducing energy waste caused by inefficient operation. Additionally, recording power consumption data allows for effective energy management, supporting the company’s ESG initiatives.
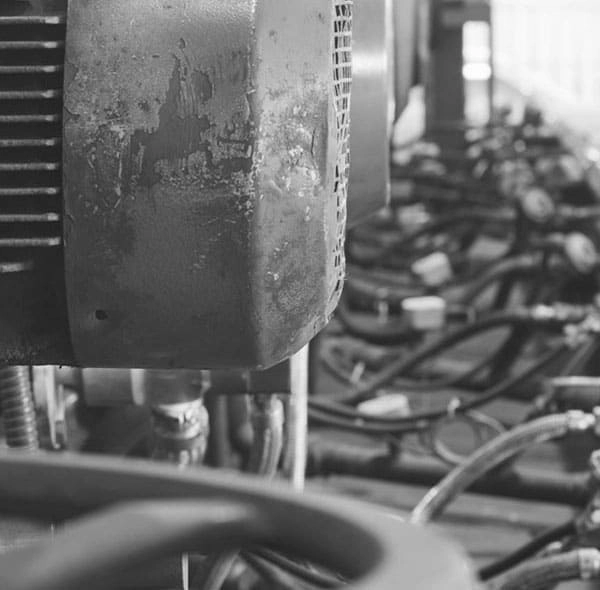
Implementation
Smart Monitoring for Power-Consuming Equipment
Monitoring Benefits
Implementing ESG
Develop Carbon Reduction Strategies
Optimize Product Design
Improve Equipment Efficiency
Enhance Corporate Image
Companies can identify energy-wasting equipment and develop carbon reduction strategies. By utilizing energy-efficient equipment, they can reduce carbon emissions and contribute to environmental sustainability. Monitoring product energy consumption enables companies to optimize product design for greater efficiency and sustainability, thereby enhancing competitiveness. Additionally, companies can use monitoring systems to track equipment status, manage energy distribution, and prevent unnecessary operations, ultimately maximizing efficiency. A strong commitment to sustainability enhances corporate brand value and attracts investors and customers.
Support
Other ESG-Related Topics