What is Smart Manufacturing?
FAQ|What is Smart Manufacturing?True smart manufacturing goes beyond automation by enhancing equipment performance, continuously optimizing production lines, and integrating effective management and decision-making to strategically improve overall efficiency.
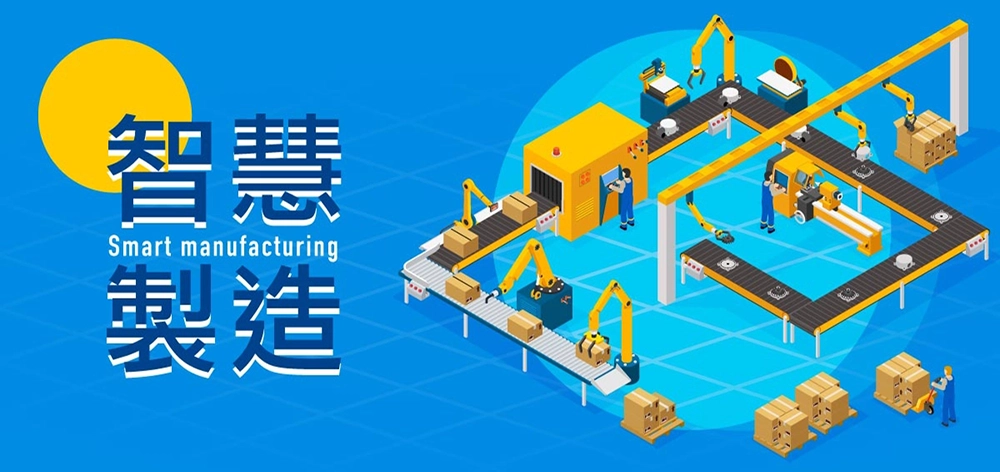
Strategically Enhancing Overall Efficiency
Automation and Monitoring in Parallel
The goal of smart manufacturing is to shorten product development cycles, reduce costs, improve production efficiency, and enhance product quality, all while strategically enhancing overall efficiency. This includes smart production, smart equipment, smart energy management, and smart supply chain management.
However, does having automated production line equipment automatically qualify as smart manufacturing? Smart manufacturing is not simply about replacing human labor with automation. It is an advanced manufacturing process, system, or model that spans design, production, management, and service, incorporating deep self-awareness, intelligent optimization, autonomous decision-making, and precise control with self-execution capabilities.
To achieve intelligent manufacturing processes, it is essential to leverage end-to-end data flow and networking technologies. The foundation of smart manufacturing lies in the ability of machinery to integrate various smart technologies, enabling predictive maintenance, precision compensation, automatic parameter adjustment, and automated scheduling.
While some factories have begun transitioning toward smart manufacturing, true smart manufacturing requires further enhancement of equipment performance, continuous production line optimization, and the integration of effective management and decision-making, all aimed at strategically enhancing overall efficiency.
How is a Smart Manufacturing Factory Structured?
Fully Integrated Smart Manufacturing Process
A smart manufacturing factory consists of various layers, each requiring specific equipment. By integrating system devices and accumulating vast amounts of complex data, analysis can be conducted to derive final insights, improve production processes, and identify root causes of issues. This enables interconnected equipment to maximize efficiency and achieve a fully integrated smart manufacturing process across the entire facility.
Application Layer
Automated production lines, etc.
Application Layer
Automated equipment
Application Layer
Sensors, AI technology
Application Layer
Internet, cloud computing, etc.
How to Start a Smart Factory
From Efficiency to Effectiveness
No matter how advanced the technology or smart solutions are, the ultimate goal is to improve overall effectiveness—whether by saving energy, time, or costs, enhancing quality, or reducing waste. Smart manufacturing requires companies to accurately and quickly understand the status of factory equipment and real-time production lines, allowing them to adjust production modes accordingly and improve factory management, decision-making, and execution capabilities.
From Mass Production to Small-Batch, Multi-Variety Manufacturing
With rapid market changes and the demand for customization in Industry 4.0, products are shifting towards customized development with smaller batch sizes and greater diversity. For businesses, shortening production cycles, reducing inventory, and ensuring consistent quality are essential goals, which align with the core objectives of smart manufacturing.
From Manual Operations to Automated Decision-Making
Previously, repetitive tasks required human labor, but with smart manufacturing, automated machinery can replace manual work, eliminating inefficiencies and reducing human errors. As machines take over, accurate decision-making becomes critical for maintaining production quality. Understanding equipment conditions allows users to respond to production line issues in real time and make better decisions. Start planning your predictive diagnostics solution today.
Common Challenges in Smart Manufacturing and Automated Factories
What Are the Common Challenges?
In the era of Industry 4.0 and smart manufacturing, many factories have adopted automation to stay competitive. However, they often face the following challenges:
How can automated production lines effectively prevent unexpected downtime?
How can quality consistency be ensured for finished products?
When and why do equipment failures occur?
How can anomalies in multi-axis robotic arm movements be detected?
How can existing production lines be upgraded to smart manufacturing with minimal disruption?
How can maintenance budgets be effectively optimized for multiple pieces of equipment?
Equipment Monitoring, Predictive Maintenance, and Smart Manufacturing
Enhancing Operational Reliability and Productivity
Equipment monitoring and predictive maintenance play a crucial role in smart manufacturing, enabling higher productivity, reduced maintenance costs, and minimized downtime. These technologies use data analytics and IoT to predict and prevent equipment failures, ensuring greater operational reliability and efficiency.
1. Equipment Monitoring and Data Analytics
Equipment monitoring continuously tracks machine performance and collects key metrics such as temperature, vibration, pressure, and current. These data points are transmitted via IoT devices and sensors to a central control system for real-time analysis and storage. By leveraging data analytics platforms, businesses can gain insights into equipment health and detect anomalies before issues arise.
2. Predictive Maintenance Applications
Predictive Maintenance leverages data analytics and machine learning to forecast potential failures. Unlike traditional scheduled maintenance, predictive maintenance anticipates failures based on real-time data trends, optimizing maintenance schedules and reducing unexpected downtimes.
3. Benefits of Smart Manufacturing
1. Lower maintenance costs: Precise failure predictions help reduce costly emergency repairs and optimize resource allocation.
2. Extended equipment lifespan: Continuous monitoring prevents excessive wear and tear, extending operational longevity.
3. Optimized production workflow: Data-driven insights enhance both individual equipment maintenance and overall production efficiency.
4. Reduced unplanned downtime: Predictive maintenance prevents sudden breakdowns, ensuring seamless production.
Digital Transformation for a Sustainable Factory
Digital Transformation Solutions
Many small and medium-sized manufacturing enterprises face challenges in upgrading and transforming their businesses.
The main obstacles are funding and management issues.
One issue is the lack of a substantial budget to invest in automation equipment.
Another is the inability to implement data-driven management systems.
In the era of smart manufacturing, digital transformation is an inevitable trend.
But does digital transformation necessarily require large-scale investments?
Is there a simpler and more cost-effective upgrade solution for small and medium-sized manufacturers with limited resources?
EMS Smart Energy Management System
As businesses face increasing pressure to achieve carbon neutrality and emission reduction goals in their production processes,
effective energy management is a crucial step toward achieving sustainable production goals and supporting global sustainability efforts.
Source: Online News, Taiwan Hydrogen & Fuel Cell Partnership, Tech Media, Wikipedia