Diagnosis and Troubleshooting for Dicing Saw Components
Why is it necessary?
Key Factors Affecting Dicing Process Quality
Dicing Blade Quality
Blade dullness, deformation, vibration, or excessive cutting force can impact the precision of the cutting path. The quality of the dicing blade depends on the supplier’s manufacturing quality control and process integration.
Dicing Process Parameters
Process parameters include feed rate, water flow rate, velocity, and blade rotation speed. These factors must be adjusted according to wafer type and characteristics, based on accumulated expertise from packaging facilities.
Dicing Machine Quality
When using similar or identical dicing machines, how can manufacturers maintain high product yield, stability, and standardization of their equipment’s performance?
With technological advancements and market demand, electronic products are becoming more powerful yet increasingly compact and lightweight.
Consequently, IC dimensions continue to shrink. In the wafer dicing process, the goal is to increase the number of die per wafer,
reduce the cutting lane width, and maximize wafer value. Every step in wafer manufacturing that could affect wafer quality
becomes critical. To enhance wafer yield, improve process standards, and reduce scrap costs during dicing, ensuring high-quality
dicing process control has become a crucial challenge.
GoodTech’s IMS-DS Wafer Dicing Saw Quality Management Analyzer helps users assess the condition of dicing saws,
diagnose and troubleshoot individual components, and precisely control wafer dicing saw quality.
Monitoring Items
Key Components of a Dicing Machine?
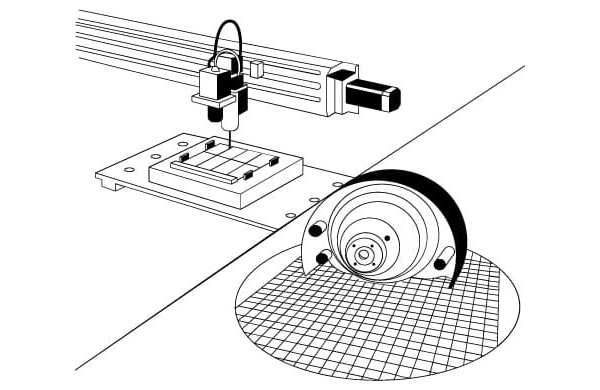
The key components of a dicing machine include:
The spindle (cutting rotation axis), vertical movement axis (Z-axis), horizontal movement axis (Y-axis), longitudinal movement axis (X-axis), and wafer dicing blade.
In the dicing process, any malfunction in motion control, positioning control, or mechanical wear and tear directly impacts cutting quality.
Each component can be further categorized into:
Dicing Machine Spindle:
Air-bearing spindle, spindle dynamic balance level, cutting tool, blade adapter, protective cover.
Vertical Movement Axis (Z-axis):
Servo motor, driver, bearings, ball screw, linear guideway.
Horizontal Movement Axis (Y-axis):
Servo motor, driver, bearings, ball screw, linear guideway.
Longitudinal Movement Axis (X-axis):
Servo motor, driver, bearings, ball screw, linear guideway.
Increase Yield
Reduce Scrap
Helps users assess the condition of wafer dicing machines, leading to increased wafer yield, improved process standards, and reduced scrap costs. By diagnosing and troubleshooting individual components, it enables precise and effective quality control of wafer dicing machines.
Function Description
UI Feature Screens
Wafer Dicing Saw Quality Management
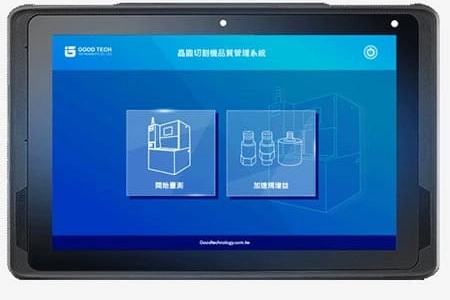
IMS-DS Wafer Dicing Saw Quality Management Analyzer enables effective management of wafer dicing saws and is compatible with various brands and models.
Measurement parameters can be easily configured for vibration levels and dynamic balance standards. Users can set threshold values independently for precise and efficient wafer dicing saw quality control.
Intuitive and Visual User Interface
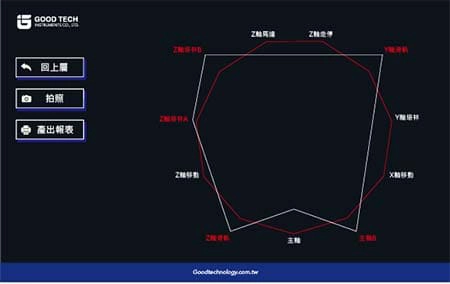
IMS-DS Wafer Dicing Saw Quality Management Analyzer features an intuitive, graphical, and visual interface, simplifying complex measurement processes. The system provides an easy-to-use, intuitive experience for users.
It includes a built-in measurement point photo setup function for easy reference. The summary analysis feature presents results using a radar chart, allowing users to quickly identify components requiring urgent maintenance.
Built-in Dicing Machine Recommendations and Guidelines
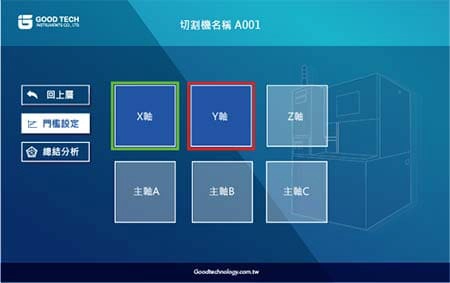
IMS-DS Wafer Dicing Saw Quality Management Analyzer includes built-in inspection recommendations and factory-specific standards for dicing machines. Users can set and customize standards to meet their needs. When component failures occur, the system provides warning notifications.
Red indicates abnormal values, suggesting potential component wear. Green indicates normal values, confirming that components are in good condition. This provides users with an accurate reference for maintenance decisions and analysis.
Portable and Lightweight Touchscreen Display
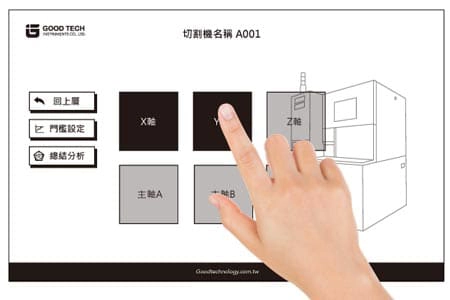
IMS-DS Wafer Dicing Saw Quality Management Analyzer is lightweight and portable, allowing users to conduct real-time measurements anywhere. Additionally, users can request on-site measurement services from our expert engineers, who will provide hands-on operation, professional insights, and training for an optimized experience.
Benefits
Immediate Feedback
IMS-DS Wafer Dicing Saw Quality Management Analyzer is designed to separate each die (DIE) from the wafer during the dicing process.
The spindle operates at speeds between 30,000 to 60,000 rpm. Since the spacing between dies is extremely small and the dies themselves are fragile,
high precision is required. The quality of the dicing process has a direct impact on the final quality of the dies.
For example, axial vibration in the dicing machine can increase the cutting lane width, potentially damaging or scrapping dies.
If the cutting line deviates or misaligns, the die could chip or crack, leading to electrical failures or high defect rates during IC packaging.
IMS-DS Wafer Dicing Saw Quality Management Analyzer offers precise measurement options tailored to the required parameters.
By accumulating data and setting threshold values, the system provides engineers with key insights to optimize production yield.
The intuitive, graphical, and visual interface simplifies traditional complex measurement operations, allowing users to quickly master the system.
A photo-based measurement point setup makes it easier to remember testing locations. Automatic report generation reduces documentation time,
while real-time alerts provide clear maintenance guidance and predictive maintenance recommendations.
This helps prevent unnecessary over-maintenance, reduces maintenance costs, and ultimately enhances wafer yield, improves precision, and minimizes scrap losses.
Quick to Master
Equipment Control
Precision Maintenance
Optimize Efficiency
Reduce Scrap
Lower Costs
Specifications
Seamless Integration of Hardware, Electronics, and Software
Equipped with a USB interface for easy data access and transfer, the system features a full touchscreen input and a 10-inch full-color display for real-time measurement data and computational results. Its lightweight and portable design enables users to conveniently conduct on-site measurements. Additionally, the system supports camera expansion for capturing and storing measurement environments effortlessly. It is IP65-rated, ensuring waterproof and dustproof protection compliant with international safety standards.
Support
Other Semiconductor Industry Solutions