Ensuring Precision in the Cutting Process
Download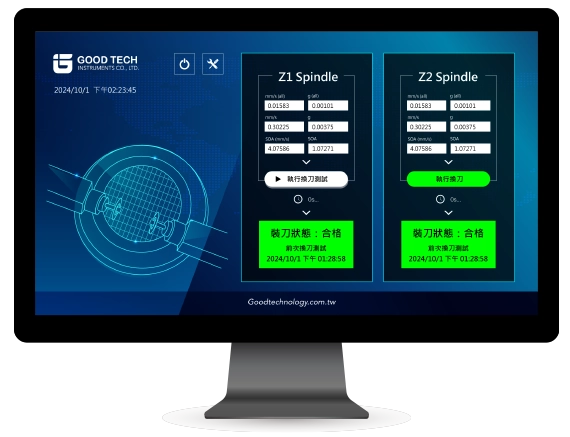
Blade Installation Quality Monitoring System
Ensuring Die Cutting and Blade Installation Quality
Why is it necessary?
Caution! Micron-level precision determines process success!
From raw materials to final wafer-level packaging, wafers go through hundreds of processes, including material processing, lithography, etching, doping, cleaning, and metallization. With CoWoS stacking technology, its highly integrated multi-layer structure and dense interconnections make each wafer extremely valuable. As a result, precision requirements are becoming more stringent, and even the slightest deviation can impact process success.
What happens when the blade cuts at an angle?
The cutting blade is one of the key factors affecting precision cutting.
Even the slightest misalignment or damage to the blade can lead to uneven wafer edges,
inconsistent cut widths, and an increased risk of microcracks, die chipping, die cracking,
or misaligned cuts.
Moreover, if the cut angles are uneven, the next cutting process may result in
accelerated tool wear, breakage, more frequent blade replacements,
or even chip damage.

Monitoring Items
Wafer Cutting Process Management
Feature Description
Digitalized Control to Ensure Blade Replacement and Installation Quality!
Is it difficult to control blade installation quality during replacement? To ensure stability in the cutting process, any installation error can result in inaccurate cuts. Therefore, by utilizing VMS-CK Blade Installation Quality Monitoring System, every blade replacement process is standardized through digitalized control.
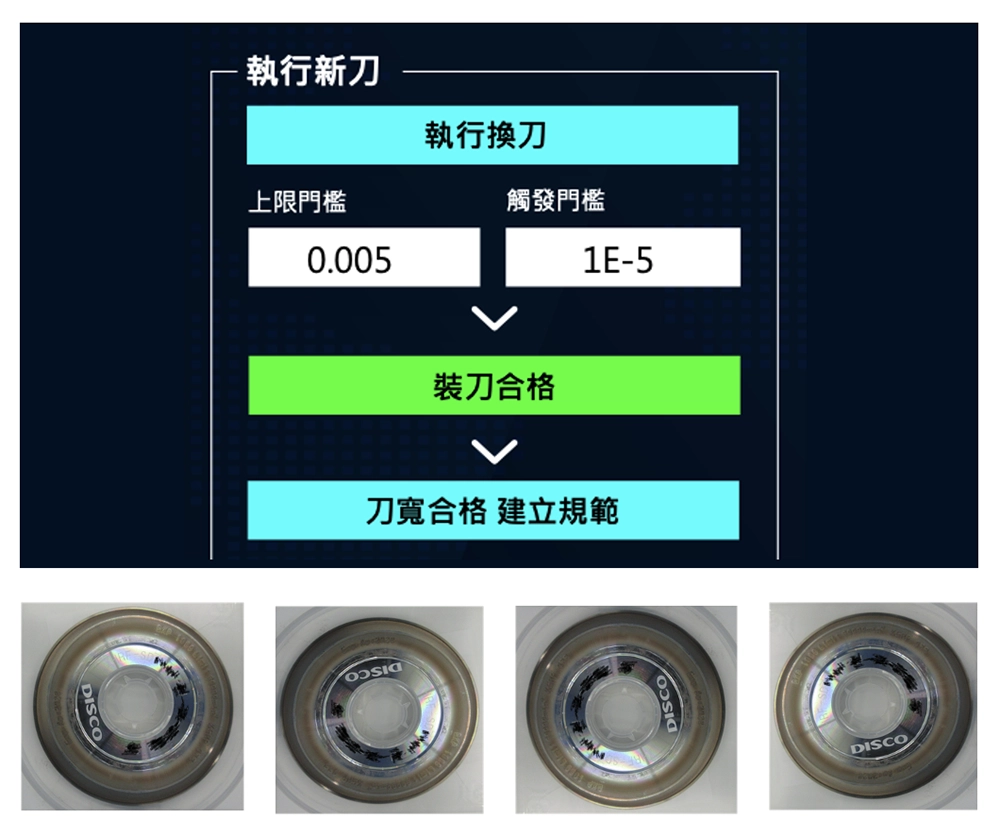
During blade replacement, up to four angle adjustments can be made to achieve optimal dynamic balance. With standardized blade installation, controlled cutting with optimal vibration quality is ensured!
Feature Description
Detect Variations in the Cutting Cycle and Reduce Defect Rates!
During the wafer cutting process, extremely fine debris is generated. Due to high cutting and feed speeds, these small fragments are ejected at high velocity. When these tiny particles get caught in the cutting process, they can accelerate blade wear or cause damage due to impact.
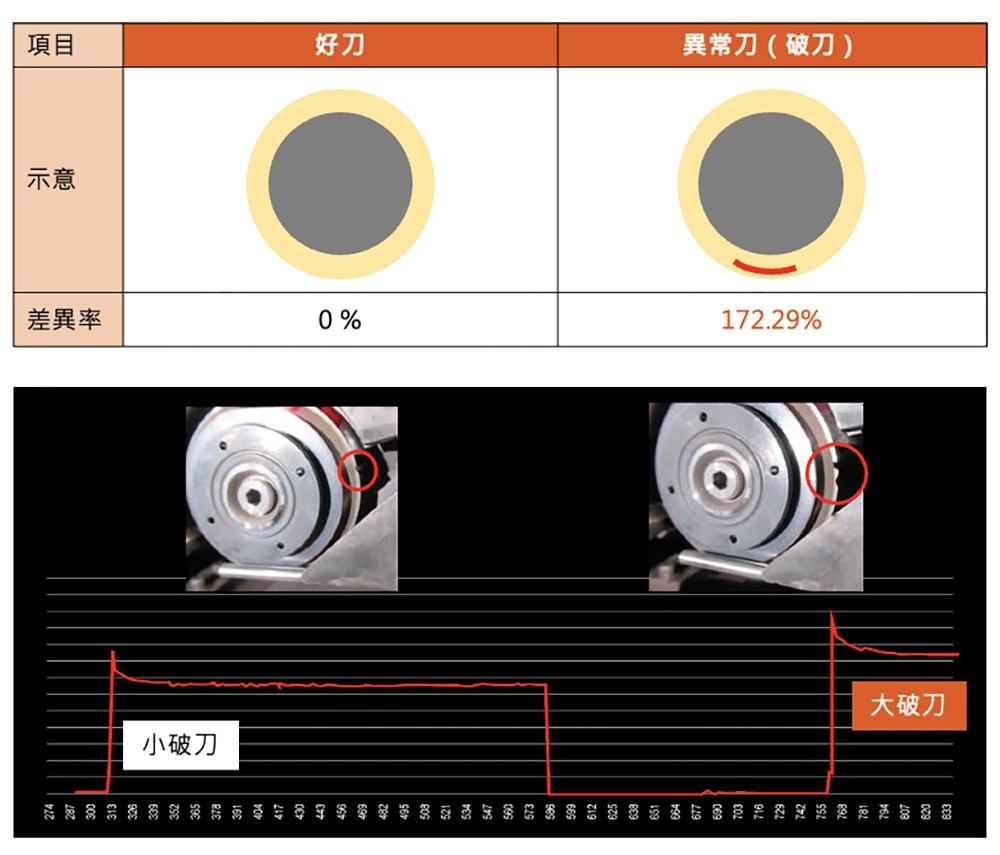
By using the VMS-CK Blade Installation Quality Monitoring System, vibration levels during the cutting cycle can be monitored, helping to detect potential variations and prevent product damage caused by continued use of an abnormal blade.
Feature Description
Monitor Moving Axes and Spindle to Prevent Vibration Anomalies!
If abnormal vibrations occur in the moving axis or spindle during the cutting process,
it can cause deviations in the cutting trajectory, leading to cracks, chipping,
rough edges, and defects, ultimately affecting wafer edge quality and subsequent processes.
Factors such as component wear due to prolonged use, structural resonance,
and motor drive abnormalities can all contribute to vibration anomalies.
Therefore, by utilizing the VMS-CK Blade Installation Quality Monitoring System,
the quality of the spindle and moving axes can be monitored,
preventing abnormal vibrations from affecting the blade.
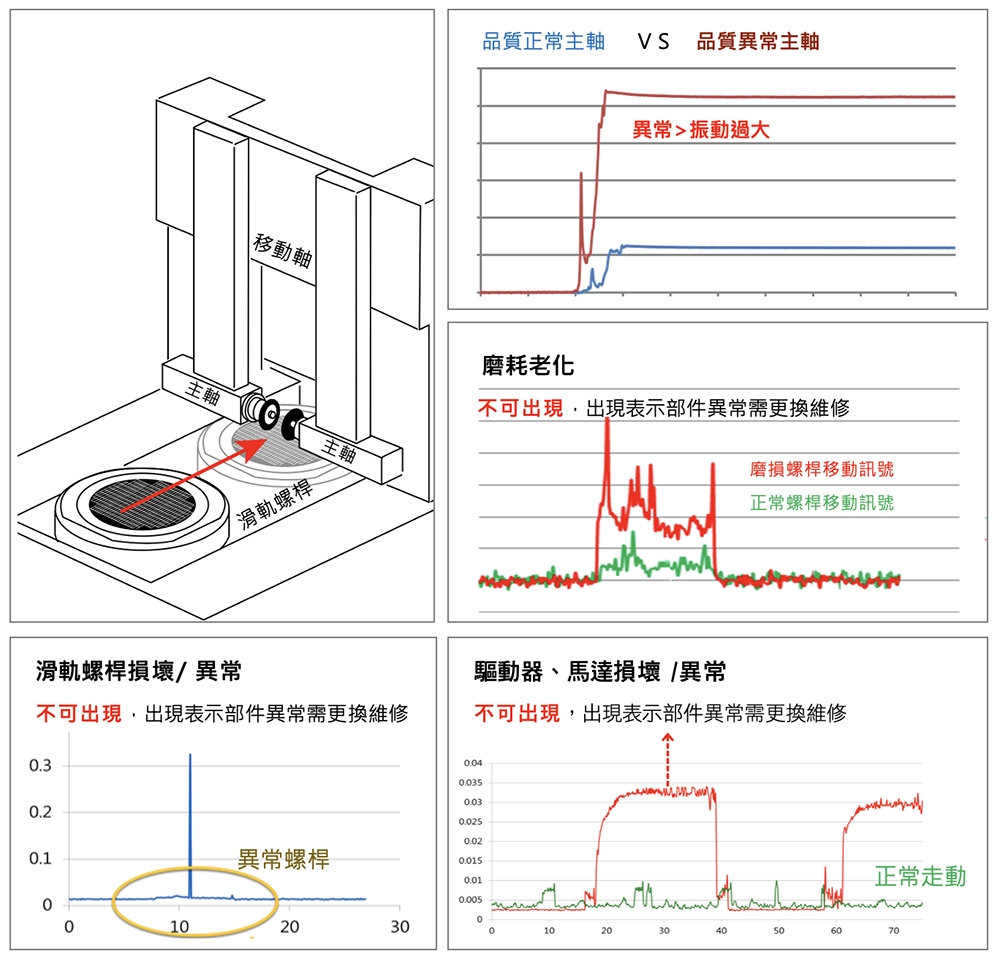
Feature Description
Monitor Blade Condition Trends and Establish Threshold Management!
Wafer materials have high hardness, and the cutting speed is fast. During the cutting process, impurities and mechanical stress gradually cause blade wear, deformation, and aging, necessitating periodic blade replacement. But how can we determine the optimal timing for blade replacement?<
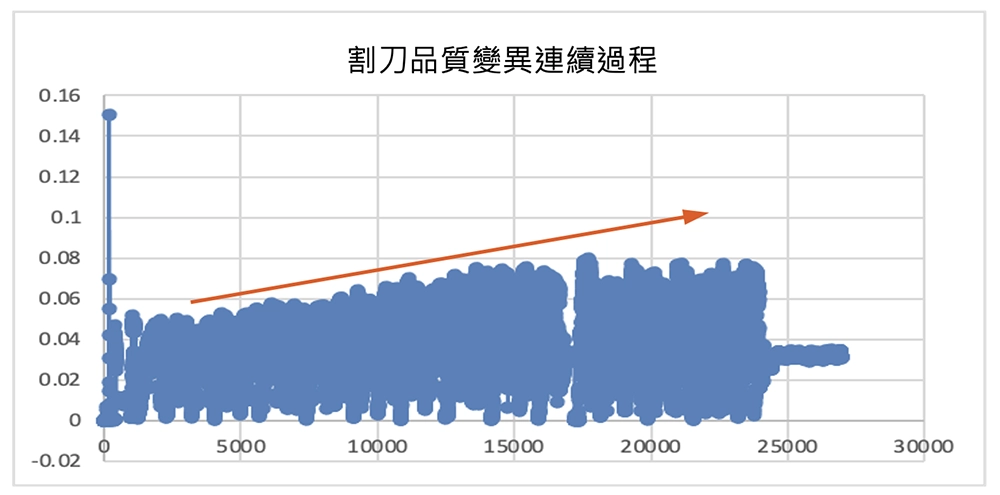
By utilizing the VMS-CK Blade Installation Quality Monitoring System, the quality trend of the blade can be monitored, allowing threshold management to detect anomalies early and prevent defects caused by misaligned blades.
Feature Description
Protect Products with Real-Time Data Analysis!
During the dicing process, if the incoming wafer has already been cut at an angle in a previous step, the blade may come into contact with the die before reaching the intended cutting depth, leading to die cracks or chipping, ultimately causing quality defects.
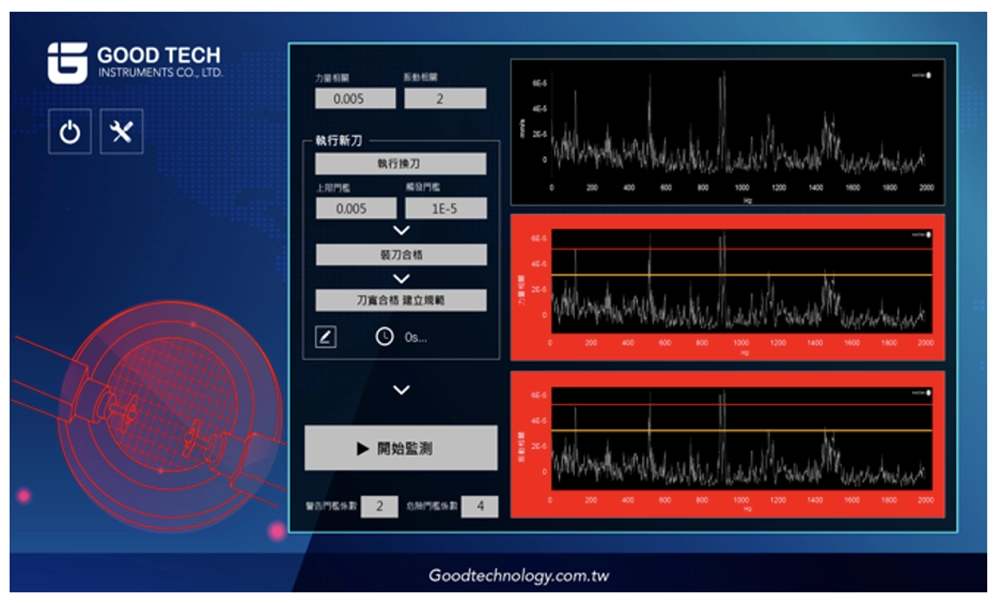
To prevent such issues, the VMS-CK Blade Installation Quality Monitoring System monitors vibration characteristics during the cutting cycle, allowing the detection of potential anomalies and preventing continuous product damage. Management plans can be tailored based on real-time operating conditions.
Benefits
Increased Efficiency, Shorter Lead Times!
By utilizing the VMS-CK Blade Installation Quality Monitoring System, equipment quality control is enhanced, reducing cutting deviations, wafer placement errors, and die abnormalities during the process. Accurate predictive maintenance reduces replacement frequency and costs, extending equipment lifespan. Consistent wafer cutting quality minimizes rework and scrap due to quality issues. Regular maintenance of equipment and blades decreases downtime caused by failures and blade damage, boosting production output. Strict quality monitoring and equipment management ensure product consistency and high quality, strengthening customer trust and satisfaction. A highly efficient production process with a lower rework rate shortens production cycles, allowing faster response to market demands.
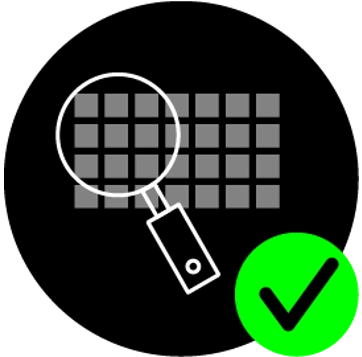
Increase
Product Yield
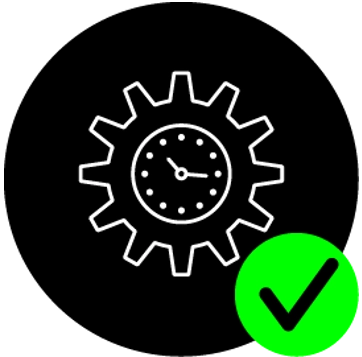
Extend
Equipment Lifespan
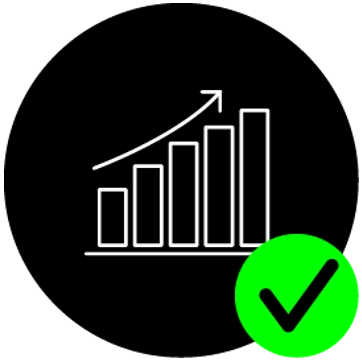
Improve
Production Efficiency
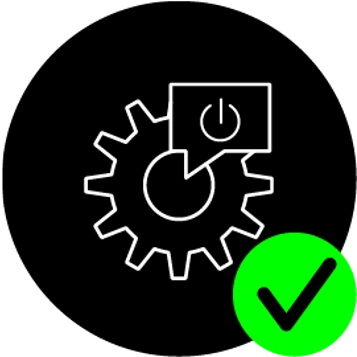
Reduce
Downtime
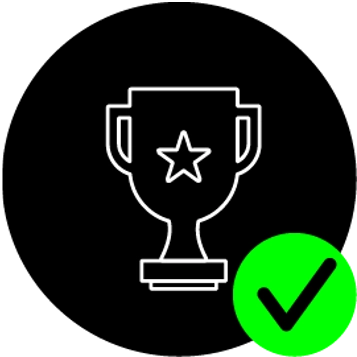
Enhance
Competitiveness
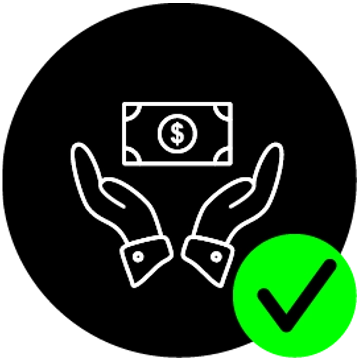
Shorten
Delivery Time
Operation Process
Reduce Blade Wear and Extend Lifespan
1. The lower the characteristic value monitored, the better the vibration quality factor
(vibration response across different frequency bands and physical quantities, as well as dynamic balance).
2. As manufacturing conditions become more stringent in the future, better blade installation quality
will lead to improved long-term monitoring and better signal-to-noise ratio (SNR) for detecting abnormalities.
3. By ensuring proper blade installation, blade wear can be reduced, and its lifespan extended.
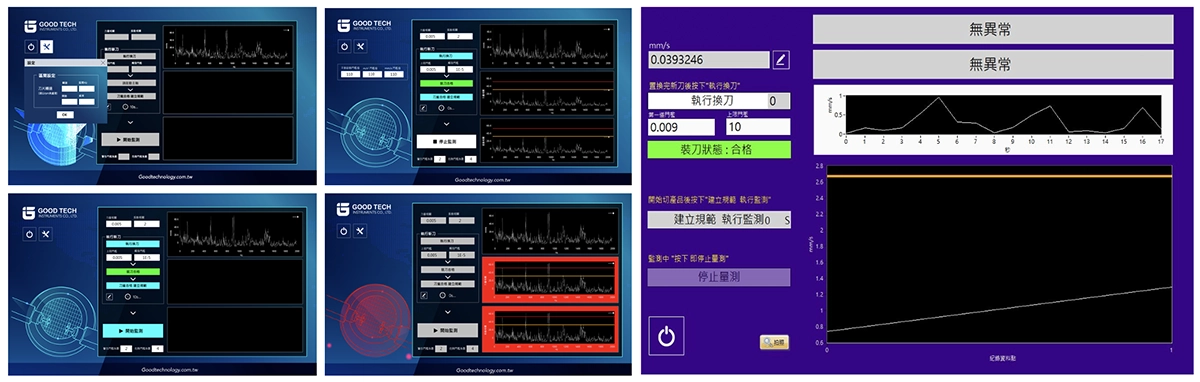
Support
Other Semiconductor-Related Fields