設備効率管理
解決策|設備効率管理ソリューション最新のデータ分析技術を活用し、エネルギー消費をリアルタイムで監視し、炭素排出量を削減。 効果的な OEE 管理を実施することで、効率的かつ環境に優しい生産モデルを構築し、 工場の最適な生産状態を実現しながら、環境への影響を最小限に抑えます。
導入理由
設備効率 (OEE) 管理の重要性
設備総合効率(Overall Equipment Efficiency, OEE)
OEE は、製造プロセスにおける設備の運用効率を評価するための重要な指標です。
OEE を監視することで、企業は設備の実際の稼働状況を把握し、改善の可能性を特定できます。
これにより、生産効率の向上、不要なダウンタイムの削減、設備の最適化が可能になります。
稼働率・性能・良品率の関係性を理解することで、企業はより効果的にリソースを計画し、
生産ラインの安定した運用を確保できます。結果として、生産コストの削減と製品品質の向上につながり、
顧客の要求を満たし、満足度を高めることができます。
FactoryOEE は、革新的な工場管理ツールであり、生産効率の向上だけでなく、
エネルギー消費と炭素排出量の削減にも注力しています。
最新のデータ分析技術を活用し、エネルギー消費をリアルタイムで監視することで、
環境負荷を抑えつつ、持続可能な生産体制を構築します。
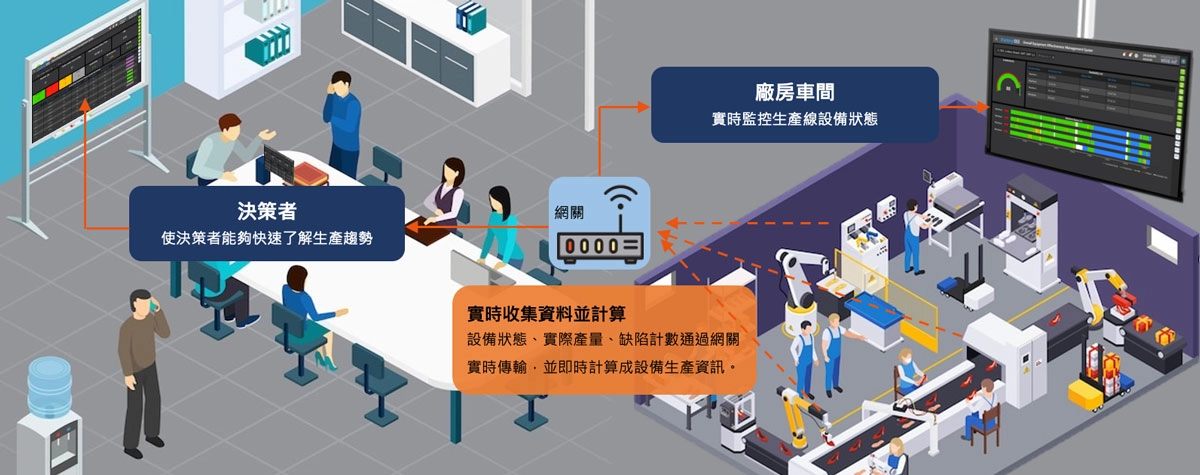
実施課題
工場の設備は稼働しているのに、生産能力が向上しない?
工場の生産能力の向上は管理者にとって大きな課題です。 設備が正常に動いているように見えても、生産性が向上しないのはなぜでしょうか? その原因はさまざまで、設備の故障による生産速度の低下や、計画的な生産スケジュールの不適切さが考えられます。 このような課題を迅速に特定できる管理ツールが必要であり、工場の生産能力を早急に回復させることが求められています。
実施方法
生産ラインのボトルネックを迅速に特定
設備効率管理システムは、即時導入可能な可視化ダッシュボードです。 生産ラインの運用データ(生産速度、リソース使用状況、ダウンタイムなど)を収集し、 生産性を低下させる要因を特定します。 また、頻繁に故障する設備や生産指示の進捗状況を一目で把握でき、 設備の稼働率向上とムダの削減を実現します。
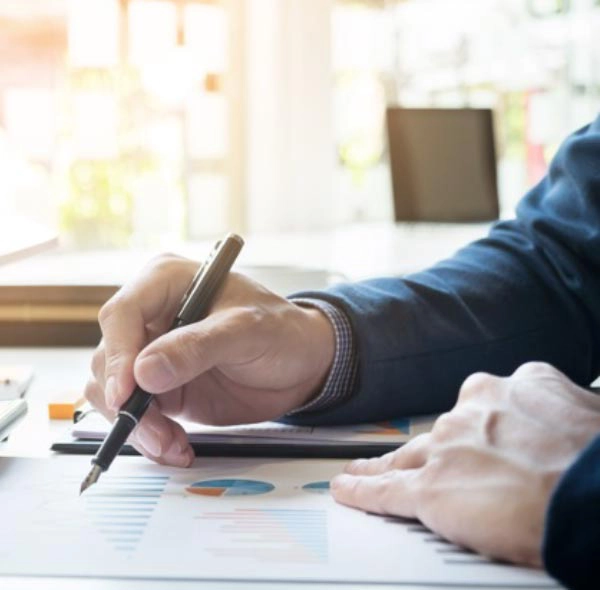
実施課題
工場が生産におけるエネルギー消費と炭素排出量を把握できていない?
ESG(環境・社会・ガバナンス)に対する関心が高まる中、 「炭素コスト」の時代が到来し、顧客は炭素排出量やエネルギー消費量に注目しています。 製造プロセスにおいて排出される炭素量は、すべてコストとして計上されるため、 製品の炭素排出量を計算し、生産履歴を確立することが重要な課題となっています。 では、どのようにして製品の炭素排出量を計算し、生産履歴を構築すればよいのでしょうか?
実施方法
エネルギー消費と炭素排出を把握し、明確な生産履歴を作成
設備効率管理システムを活用し、生産プロセスにおけるデータを収集することで、 各設備のエネルギー消費量と炭素排出量を正確に把握できます。 さらに、工単情報と統合することで、各生産単位における炭素排出量とエネルギー消費量を計算し、 製品ごとの生産履歴を明確に記録し、炭素排出に関する詳細なトラッキングを可能にします。
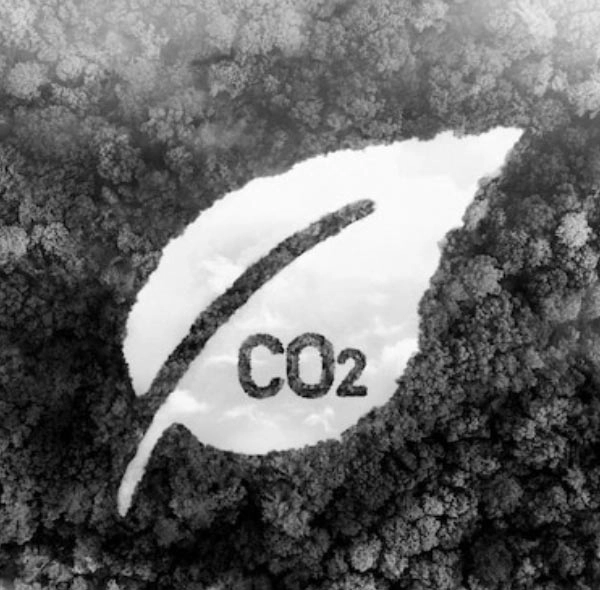
実施課題
設備が突然停止して対応方法がわからない? 進捗状況を把握できない?
工場で設備が予期せず停止した場合、 誰に報告すべきか、どのように対処すべきかわからず、 生産ラインの停滞、設備や人員の無駄な待機が発生し、コストの増大につながります。 さらに、修理を依頼しても、その後の進捗が分からず、 管理者が生産ラインの状況を把握できないことが問題となっています。
実施方法
異常イベントの追跡を確立し、精密な管理を実現
設備効率管理システム は、異常発生時に自動でイベントを記録し、 処理状況や進捗をリアルタイムで更新できるため、 設備管理プロセスを精密に管理することが可能です。 ダッシュボードを通じて異常通知を送信でき、スマートデバイスとの連携も容易です。 また、担当者グループを設定し、異常の重要度に応じて通知の優先度を調整することも可能です。

実施方法
Factory OEE 設備効率管理システム
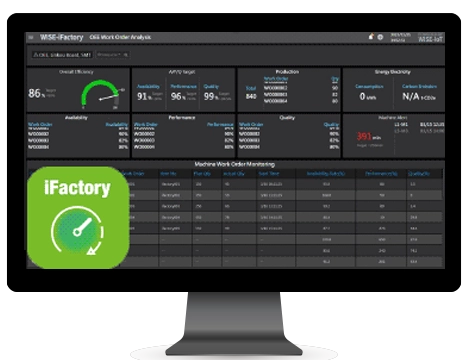
設備の生産性向上:
設備の稼働状況を自動記録し、管理者がデータに基づいて設備のパラメータや
プロセスを最適化し、生産性を向上させます。
機械のエネルギー消費を把握:
各設備のエネルギー消費量と炭素排出量を一目で確認でき、
製造プロセスにかかるエネルギーコストを正確に管理できます。
無駄な稼働時間を削減:
異常を迅速に検出・解決し、ダウンタイムを最小限に抑えることで、
ムダを削減し、製造コストを下げ、製品の利益率を向上させます。
サービスアーキテクチャ
Factory OEE 設備効率管理システム構成
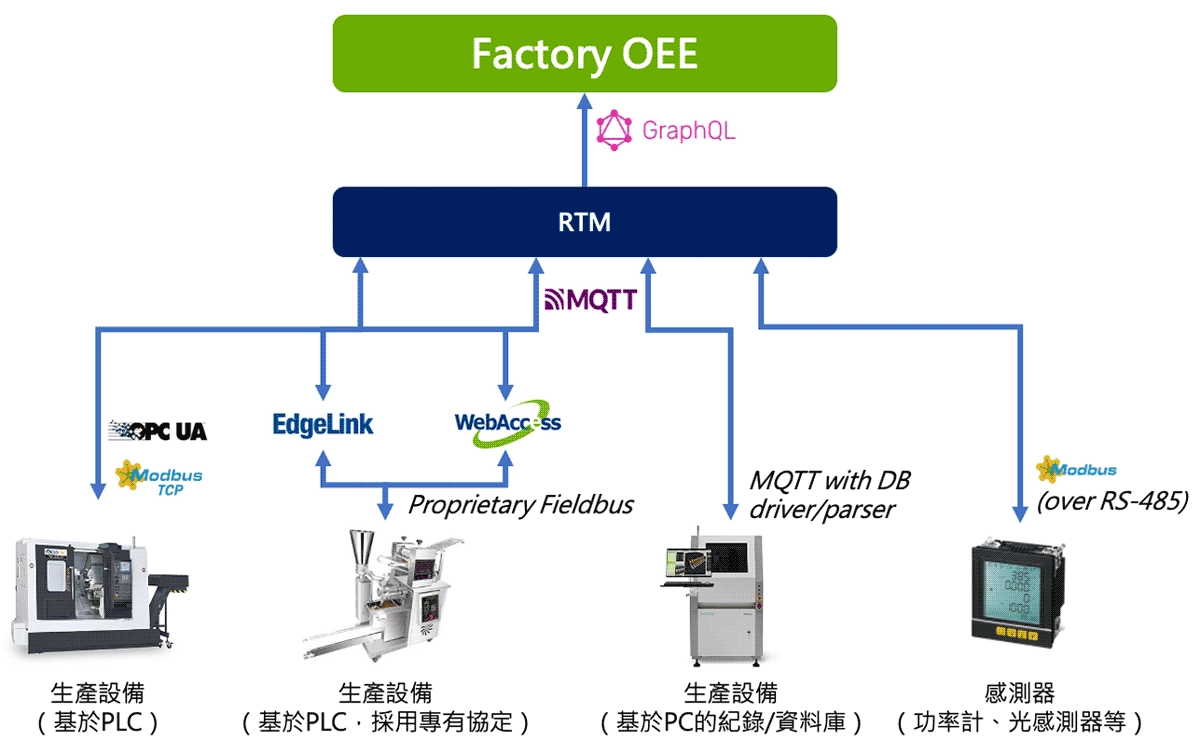
処理プロセス
異常イベント処理フロー
イベント発生
異常イベントの発生とアラート
・材料不足、ランプ点滅、機械停止などの異常を検出
・タッチパネルまたは機械からイベントをトリガー
イベント通知
異常イベントの関係者への通知
・ダッシュボード、電子メール、即時メッセージなどで通知
・リアルタイム通知でチームメンバーにタスクを割り当て可能
対応
リアルタイムでイベント対応と追跡
・カスタマイズ可能な対応時間
・カスタマイズ可能な優先度設定
・異常の原因を記録可能
・作業者と管理者がタスクを受信可能
・iMobile インターフェースを通じて作業状況や時間を報告
解決
異常イベントの修正後
Andon システムがイベントログを作成し、ダッシュボード、電子メール、即時メッセージを通じて配信。
異常状況の概要をリアルタイムで表示し、メンテナンスチームと管理者が生産ラインの改善を適切に管理可能。
Support
その他のOEE関連トピック