Equipment Efficiency Management Solution
Solutions|Equipment Efficiency Management SolutionUtilizing advanced data analytics, real-time monitoring of energy consumption can help reduce the carbon footprint. By implementing effective OEE management strategies, we aim to build a highly efficient and environmentally friendly production model that optimizes factory performance while minimizing environmental impact.
Reasons for Implementation
The Importance of OEE Management
Overall Equipment Efficiency (OEE)
OEE is a key metric for evaluating the operational efficiency of manufacturing equipment.
By monitoring OEE, businesses can assess real-time equipment performance and identify areas for improvement.
This helps enhance productivity, reduce unnecessary downtime, and optimize equipment utilization.
By understanding the relationships between utilization rate, equipment performance, and yield rate,
companies can plan resources more effectively to ensure stable production operations.
As a result, production costs are reduced, product quality is stabilized, and customer demands are met,
ultimately improving customer satisfaction.
FactoryOEE is an innovative factory management tool that not only boosts production efficiency
but also emphasizes energy conservation and carbon emission reduction.
By leveraging cutting-edge data analytics, real-time energy consumption monitoring enables
sustainable and efficient production while minimizing environmental impact.
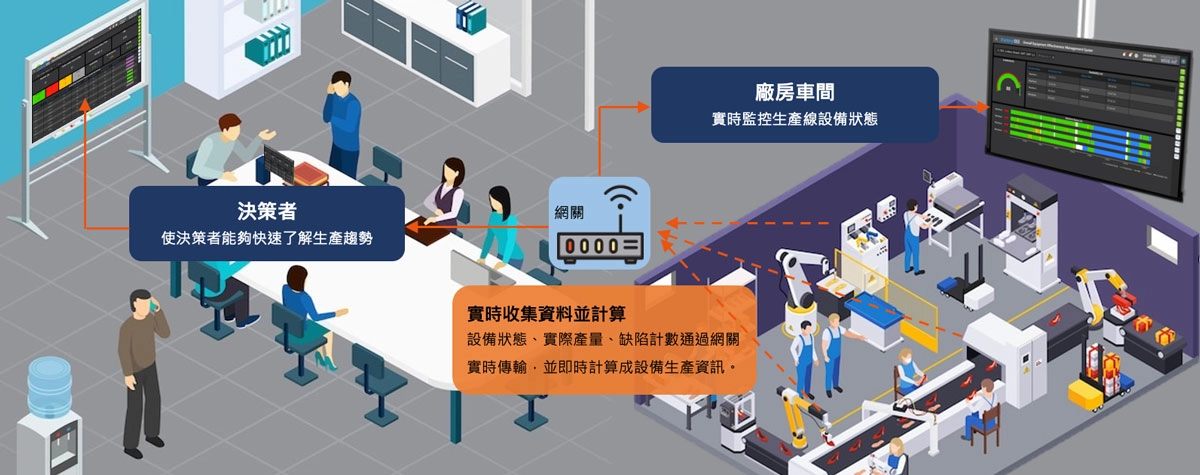
Implementation Challenges
The machines in the factory seem to be running, but why isn’t productivity improving?
Increasing factory productivity is a major concern for managers. Even when machines appear to be operating normally, productivity may not be improving. There are many possible reasons for this, such as reduced production efficiency due to equipment failures or inefficient production scheduling. A management tool that can quickly identify these issues is essential to restore factory productivity efficiently.
Implementation Method
Quickly Identify Bottlenecks Affecting Production Efficiency
The Equipment Efficiency Management System is a ready-to-use visual dashboard that collects operational data from production lines, such as production speed, resource utilization, and downtime. This allows users to quickly identify bottlenecks and frequently malfunctioning machines. Additionally, production orders can be tracked at a glance, maximizing equipment utilization and minimizing waste.
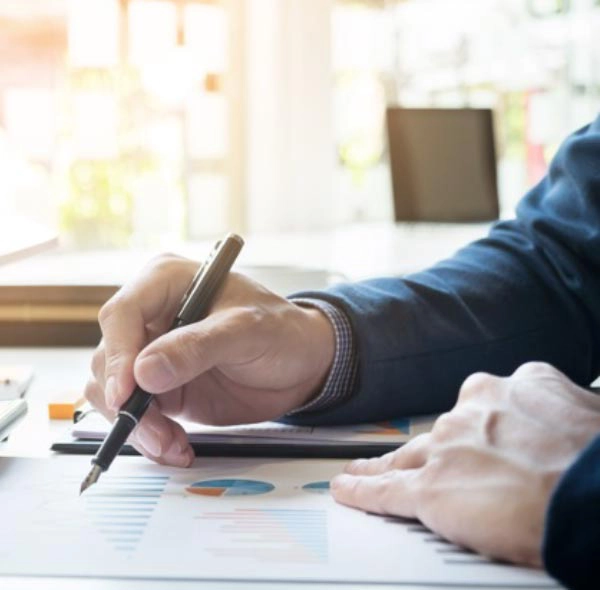
Implementation Challenges
Are factories unable to track energy consumption and carbon emissions in production?
With the rise of ESG (Environmental, Social, and Governance) concerns, the era of "carbon cost" has arrived, and customers are increasingly focusing on carbon emissions and energy consumption. Since every unit of carbon emission in the manufacturing process translates into costs, it is crucial to calculate the carbon footprint of products and establish production records. But how can manufacturers accurately calculate carbon emissions and build production histories?
Implementation Method
Track Energy Consumption and Carbon Emissions for a Transparent Production Record
By utilizing an Equipment Efficiency Management System, factories can collect data from the production process and accurately measure energy consumption and carbon emissions for each piece of equipment. Furthermore, by integrating work order information, the system calculates carbon emissions per production unit, helping businesses establish a clear production record and track emissions at every stage.
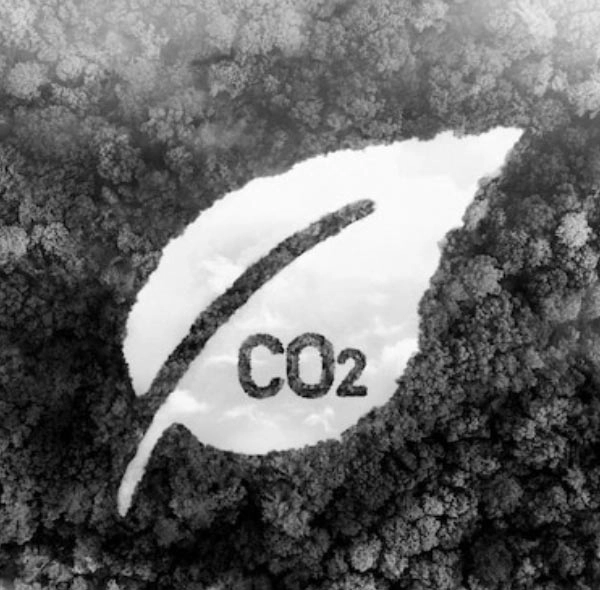
Implementation Challenges
Unexpected Machine Downtime? No Clear Response Plan?
When unexpected equipment downtime occurs in a factory, employees often don’t know whom to report to or how to respond. This results in unclear production delays, idle equipment, and wasted labor costs. Even after reporting the issue for maintenance, managers struggle to track repair progress, making it difficult to oversee production schedules effectively.
Implementation Method
Establish Event Tracking for Precision Management
The Equipment Efficiency Management System allows factories to log abnormal events, update statuses in real-time, and track issue resolution for efficient incident management. The dashboard enables automatic notifications across various smart devices. Users can configure contact groups for event notifications and adjust event priority levels based on severity to ensure appropriate escalation.

Implementation Method
Factory OEE Equipment Efficiency Management System
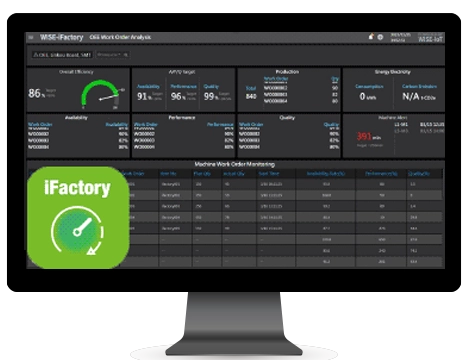
Increase Equipment Productivity:
Automatically record equipment operation status,
allowing managers to optimize parameters and processes
based on data to improve productivity.
Monitor Energy Consumption:
Clearly visualize the energy consumption and carbon emissions
of each piece of equipment, enabling precise cost and energy management
in the manufacturing process.
Reduce Idle Equipment Time:
Quickly identify and resolve abnormalities,
minimize downtime, eliminate inefficiencies,
reduce manufacturing costs, and increase product profitability.
Service Architecture
Factory OEE Equipment Efficiency Management System Architecture
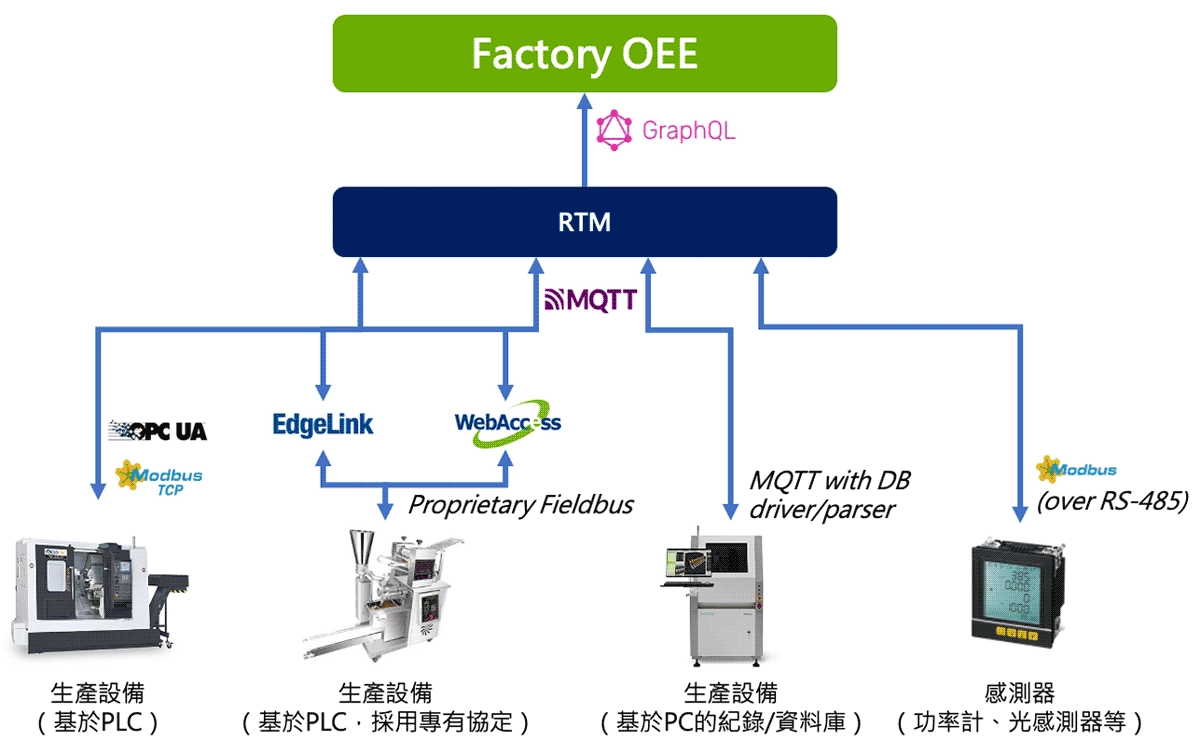
Processing Flow
Abnormal Event Handling Process
Event Trigger
Trigger alerts when an abnormal event occurs
・Detects material shortages, flashing lights, machine stoppages, etc.
・Events can be triggered via touch screen or machine
Event Notification
Notify relevant personnel of abnormal events
・Alerts via dashboard, email, instant messaging, etc.
・Real-time notifications can assign tasks to team members
Response
Real-time handling and tracking of events
・Customizable handling time
・Customizable priority levels
・Record the cause of the abnormality
・Tasks can be received by workshop workers and managers
・Report work status and time via the iMobile interface
Resolution
After an abnormal event is resolved
Andon creates an event log and distributes it via Dashboard, email, and instant messaging.
The overview displays real-time abnormal conditions, allowing the maintenance team and management to effectively control production improvements.
Support
Other OEE-Related Topics