Smart Monitoring for Automotive Manufacturing Processes
Solutions|Smart Monitoring for Automotive Manufacturing ProcessesThe automotive production process involves complex manufacturing steps that rely on a system integrating human expertise with automated equipment in an intelligent production line. Generally, it consists of five major processes, each of which is an intricate and large-scale industrial manufacturing procedure.
Why Implement It?
Ensuring Seamless Integration of Automotive Manufacturing Processes
Stamping → Welding → Painting → Final Assembly → Inspection
A brief overview of the five key processes: Stamping: Cutting and stamping metal sheets into various component shapes. Welding: Using automated welding robots to assemble and weld body parts. Painting: Applying anti-rust and aesthetic coatings to car body components. Final Assembly: Assembling the entire car, including the body, engine, tires, dashboard, and interior. Inspection: Conducting test drives under various simulated conditions to ensure the safety and quality of vehicles before delivery.
To ensure efficiency, precision, and quality at every stage, modern automotive production lines increasingly rely on intelligent and automated systems. With monitoring systems, real-time quality inspections can be conducted during the production process, ensuring that each step meets the required standards, reducing defect rates, and enhancing the final product quality. Additionally, the system can promptly detect anomalies, reducing human errors while improving overall production safety.
Moreover, by accumulating data, it is even possible to predict potential equipment failures or wear, allowing for proactive maintenance. This helps prevent unexpected breakdowns that could halt the production line, thereby reducing maintenance costs and downtime while ensuring a seamless production process.
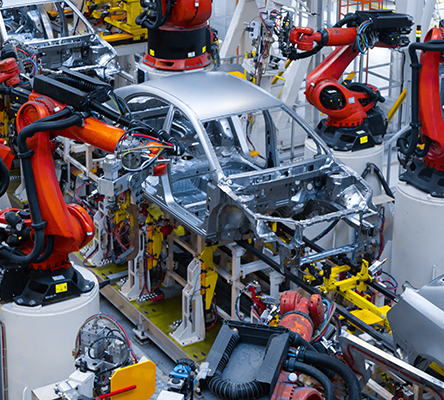
How to Implement
Ensure Process Standards and Reduce Defect Rates
By utilizing monitoring systems to accumulate large volumes of production data, companies can analyze and identify bottlenecks or areas for optimization within the production process, enabling continuous improvement. With data-driven decision-making, businesses can allocate resources more effectively, enhance production flexibility and responsiveness, and quickly adapt to market changes.
Automated Welding Line Process Monitoring
Reason for Implementation
Welding Abnormalities Compromise Structural Integrity
Many factors affect welding quality. If the welding speed is too fast, the metal may not fully melt and bond, while a speed that is too slow can cause excessive heating and deformation. Incorrect current and voltage settings may result in uneven welding, increasing the risk of weak welds or defects. These defects affect welding quality and part assembly accuracy, requiring rework or adjustments. In severe cases, they can reduce the strength and durability of welded joints, leading to part failures during operation and compromising vehicle safety and reliability.
Common Issues in the Welding Process:
・Undercut: Improper welding torch angle or position.
・Torch Collision: Assembly misalignment or inaccurate TCP (Tool Center Point) of the welding torch.
・Incomplete Welding: Discontinuity in weld seams.
・Misaligned Weld: Incorrect welding position or issues during weld path tracking.
・Lack of Fusion: Incomplete fusion between weld metal and base material or between layers.
・Burn-Through: Excessive heating during welding causes holes in the base material.
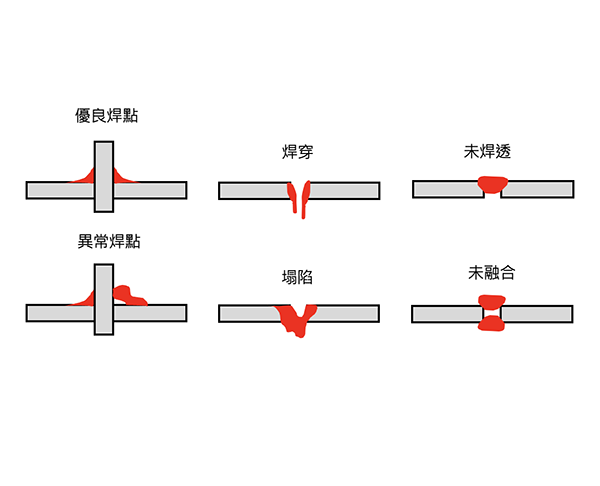
Implementation Challenges
Poor Working Conditions Causing Labor Shortages?
In addition to requiring skilled expertise, welding work is often repetitive, with monotonous manual material feeding tasks. Furthermore, the working environment typically involves high temperatures, loud noise, fumes, and harmful gases, making it difficult to attract and retain workers.
How to Implement
Implement Automated Processes to Reduce Labor Costs
Utilizing VMS®-ML Machine Learning Smart Monitoring System, automated monitoring enables process management. By analyzing signals from equipment operations, welding quality can be assessed, and standardized processes and product quality can be established. This effectively reduces labor costs and factory operational expenses, achieving scientific management in industrial component manufacturing.
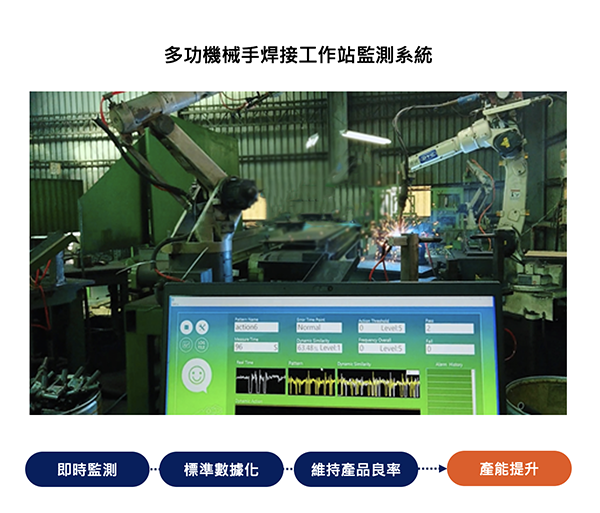
Implementation Challenges
Manual Inspection Causing Quality Inconsistencies?
In large-scale production, manual inspection can reduce overall production efficiency. Additionally, inspectors performing high-intensity observation and operations over extended periods are prone to fatigue and loss of concentration, affecting the accuracy of inspections. Some welding defects, such as internal cracks or tiny pores, may not be detected through visual inspection, impacting the final product's quality and reliability.
How to Implement
Data-Driven Automation to Ensure Product Consistency
By leveraging VMS®-ML Machine Learning Smart Monitoring System, data is recorded and tracked to overcome the limitations of manual inspection. This improves inspection consistency and traceability, ensuring the quality and reliability of the final product.
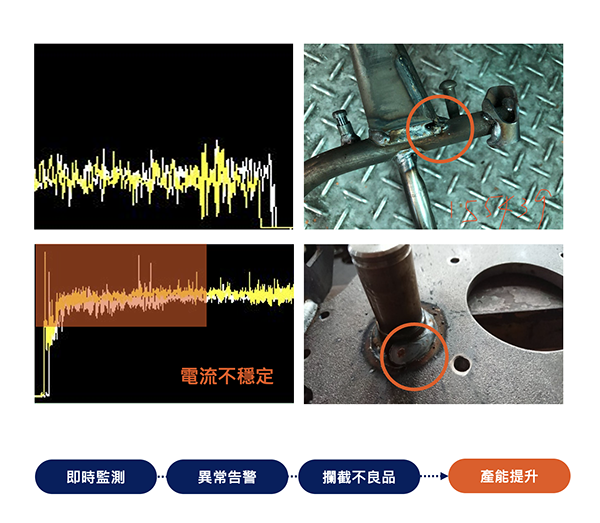
Implementation Challenges
Complex Robotic Arm Movements Making Monitoring Difficult?
Welding robotic arms have complex structures and diverse motion patterns, making sensor installation challenging during monitoring deployment. Additionally, different manufacturers produce various robotic arms, with machine data managed by third-party vendors, leading to difficulties in system integration and data exchange.
How to Implement
No System Integration Required – Ready-to-Use Monitoring
With VMS®-ML Machine Learning Smart Monitoring System,
monitoring can be performed without system integration or invasive installation, truly achieving PLUG & IN.
A single sensor based on key process monitoring parameters is all that’s needed.
For example, an electrical clamp meter on a welding robot arm can be used to calibrate current reference points,
enabling real-time monitoring of current and voltage to manage critical welding process variables.
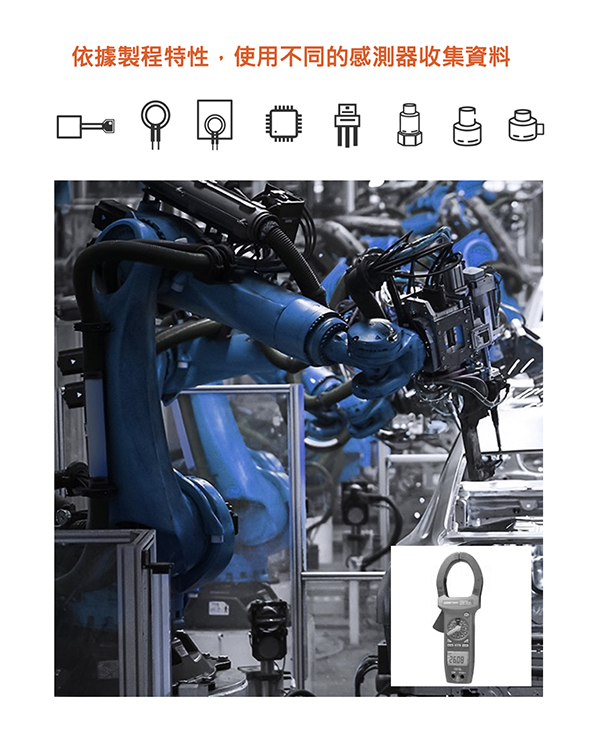
VMS®-ML Machine Learning Smart Monitoring System
Designed for real-time dynamic monitoring of various mechanical equipment, users can easily define operational benchmarks, while the system learns from accumulated data to perform statistical analysis and anomaly detection. This enables predictive maintenance planning and helps designers optimize production line workflows.
VMS®-ML Machine Learning Smart Monitoring System
Implementation Case
Automotive Sheet Metal Welding Quality Control
Issue: Insufficient or defective welding can cause joints to break or deform under stress, compromising structural stability and durability.
Solution: Compare Current Signals to Automatically Determine Welding Quality
Automated welding robots assemble various components into a vehicle body.
In this project, the VMS-ML system was installed at the workstation,
where a clamp meter was used to monitor current levels based on the welding robot arm's characteristics.
The system quickly learns the correct process standards and automatically recognizes and tracks signals.
By comparing current signals, the system automatically determines welding quality.
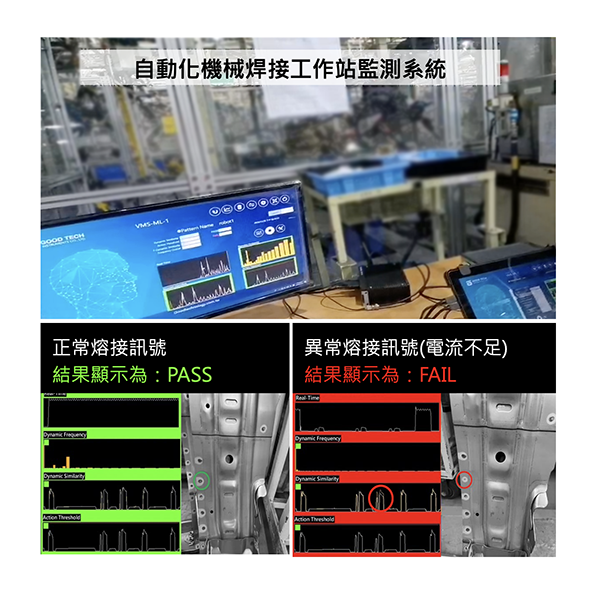
Benefits & Results:
The system detects abnormal signals in real time and issues immediate alerts,
preventing human judgment errors.
This helps users monitor the production line status and take prompt action,
ultimately improving product quality on the production line.
Electrodeposition Coating Line Process Monitoring
Reason for Implementation
Pump Malfunctions Leading to Workpiece Contamination
Electrodeposition coating consists of four main steps: pre-treatment, electrophoretic coating, rinsing, and baking. This process applies anti-rust coatings and smooth finishes to automotive sheet metal. It relies on extensive pump systems to extract water-based coatings or distilled water for pre-cleaning, degreasing, washing, rust removal, neutralization, and phosphating in a water circulation filtration process.
When a Pump Malfunctions:
Issues such as internal bearing or impeller damage, filter clogging due to impurities in the liquid, or motor coil burnout can prevent proper filtration of impurities and result in uneven liquid concentration and temperature distribution. This may lead to workpiece contamination, affecting production efficiency and the final coating quality.
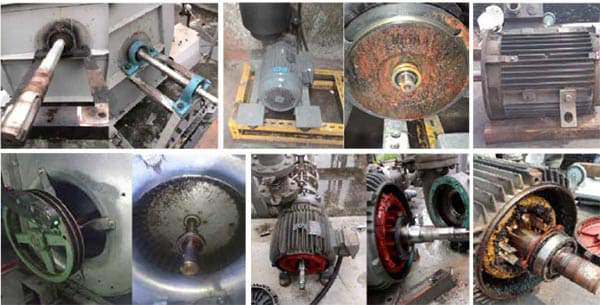
Implementation Challenges
Large Number of Pumps Making Inspection Difficult?
The large number of pumps and their widespread locations pose significant challenges for inspections. Simply measuring these systems—such as exhaust fans, compressors, high-pressure motors, and vacuum pumps—already consumes a great deal of time, making routine inspections even more labor-intensive.
How to Implement
Online Monitoring Replacing Manual Inspections with Flexible Expansion
RM-IoT Online Monitoring System can replace manual inspections,
allowing the system to send instant alerts when equipment anomalies occur.
Continuous data collection enables maintenance engineers to focus on higher-value tasks.
Its flexible expansion architecture allows users to gradually add monitoring points based on budget.
Users can also categorize and manage different areas and equipment based on their priority and importance.
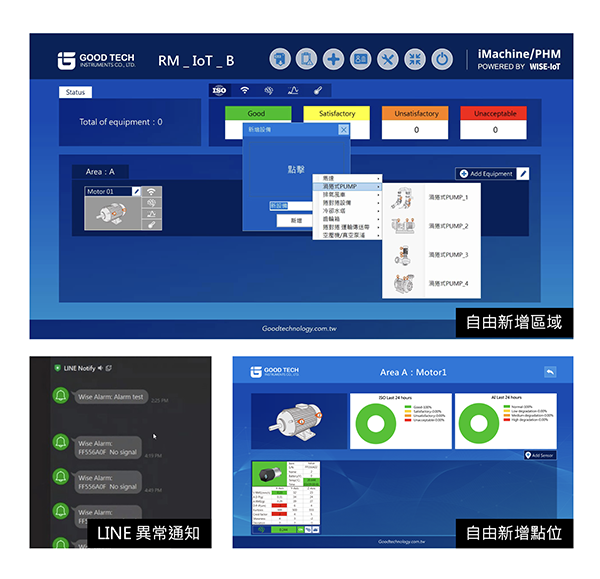
Implementation Challenges
Unclear Equipment Status Leading to Unexpected Downtime?
Unexpected pump shutdowns can result in uneven distribution of pre-treatment liquid concentration and temperature, affecting degreasing, acid pickling, neutralization, and phosphating effectiveness. This may compromise coating adhesion and corrosion resistance, causing interruptions in pre-treatment liquid supply and forcing production lines to halt, ultimately reducing operational efficiency.
How to Implement
Apply Standards for Rapid Equipment Status Assessment
The RM-IoT Online Monitoring System is preloaded with ISO standards,
eliminating the need for users to memorize threshold values.
Simply apply the appropriate standard based on motor output range.
The system categorizes equipment status with color-coded indicators:
"Excellent," "Normal," "Warning," and "Danger."
This helps implement predictive maintenance and prevents unexpected equipment failures.
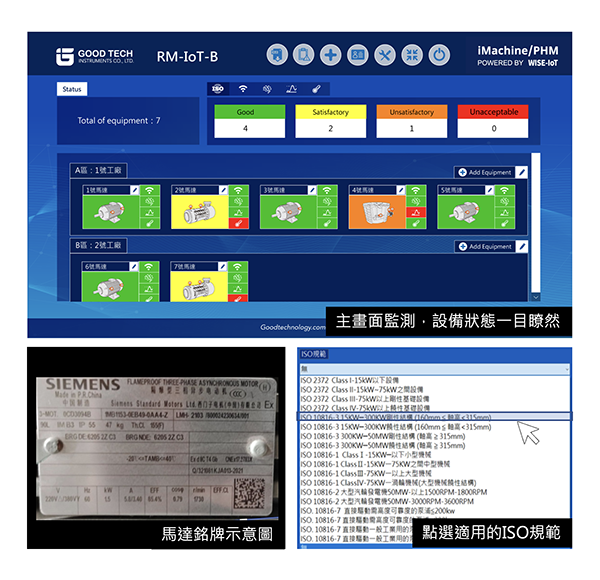
Implementation Challenges
ISO Standards Not Applicable?
While ISO standards cover most rotary equipment in industrial facilities, if they do not meet specific requirements, users can define their own threshold management system or adjust parameters according to manufacturer specifications. This enables effective hierarchical management and more precise equipment monitoring.
How to Implement
Custom Thresholds & AI-Based Degradation Prediction
RM-IoT Online Monitoring System accumulates characteristic data such as VRMS vibration signals, performing AI-based cross-analysis for early fault diagnostics. Over a 7-day period, the AI predicts equipment aging and degradation, eliminating the need for complex frequency spectrum analysis. Users can schedule maintenance based on equipment conditions, ensuring early preparation of spare parts and avoiding unnecessary downtime.
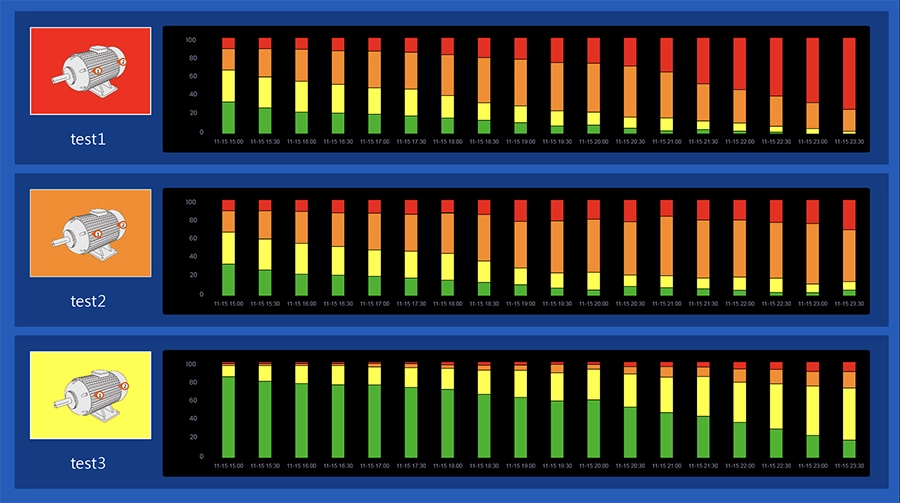
RM-IoT Online Monitoring System
Most equipment contains a motor, which drives mechanical operations. As a result, factories are filled with numerous motors, pumps, compressors, and air conditioning systems. By monitoring the rotor’s condition, it is possible to identify 60-70% of critical equipment issues.
RM-IoT Online Monitoring System
Implementation Case
Cooling Tower & Chiller Monitoring
Issue: Chillers are critical equipment for industrial sites, but their elevated installation locations make inspections difficult. Additionally, equipment failures pose potential workplace safety risks.
Solution: Ensure Safety & Reduce Wiring Costs
The RM-IoT system installs sensors near the bearing positions to record XYZ-axis directions.
Utilizing LoRa low-power transmission, LoRa covers a distance of approximately 300–800 meters,
allowing users to configure data transmission intervals as needed.
An optional mobile monitoring feature enables integration with smartphones and tablets,
supporting unlimited logins from any location.
This allows for 24/7 real-time asset performance monitoring and status analysis.
When equipment anomalies occur, the system sends alerts immediately,
ensuring timely corrective actions.
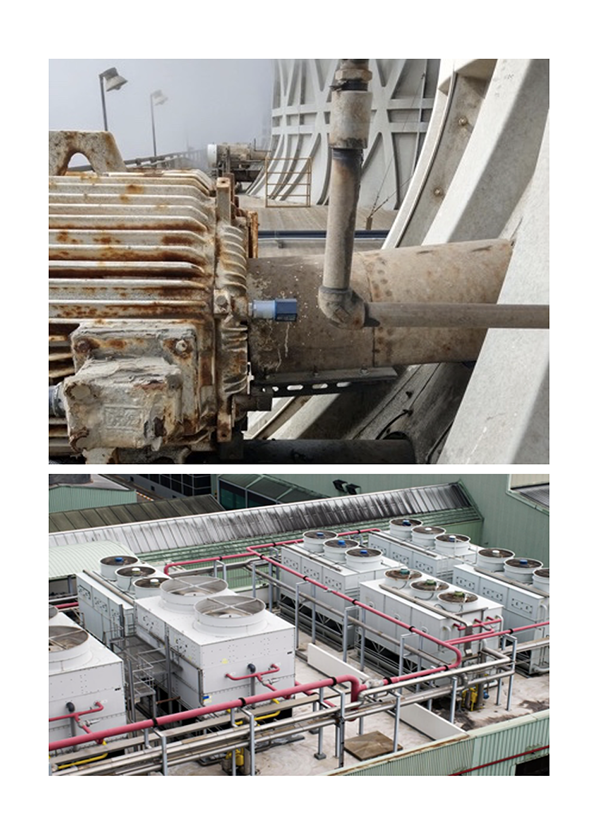
Benefits & Results:
Replaces manual inspections to enhance worker safety.
RM-IoT's flexible design allows gradual expansion of monitoring points.
The wireless system significantly reduces wiring and piping installation costs,
optimizing space utilization within the facility.
Final Assembly Line Process Monitoring
Reason for Implementation
Robot Arm Malfunctions Cause Losses
Currently, over 70% of automotive manufacturing lines worldwide use automated robotic arms. These large robotic arms perform tasks such as transportation, assembly, cleaning, and welding with high speed, safety, and precision, enabling repetitive heavy-duty tasks that would be difficult for human workers to handle.
Problems Caused by Robot Arm Failures:
However, machines cannot communicate their own issues. If robotic arm quality is not assured, failures such as collisions, mechanical damage, and unstable power supply may occur. If the arm collides with other equipment or workpieces, it may become damaged or jammed. Similarly, unstable power supply or sudden power loss can disrupt normal arm operation. These issues increase repair and replacement costs, cause production downtime, and lead to economic losses, while also posing potential workplace safety risks.

Implementation Challenges
Large Vibration During Start & Stop Causes False Alarms?
The operation of large robotic arms is highly complex. In addition to experiencing significant vibrations during start and stop phases, normal and abnormal signals often overlap during operation. If abnormal signals are detected solely based on numerical thresholds, this may lead to frequent false alarms.
How to Implement
Establish Standards & Automate Tracking, Recognition, and Scoring
Using VMS®-ML Machine Learning Smart Monitoring System,
automated tracking and recognition technology applies tailored learning models for different manufacturing processes,
enabling customized threshold monitoring.
The system automatically detects calibrated target signals in real-time monitoring data.
Even if mechanical anomalies or external disturbances occur during manufacturing,
the system accurately identifies whether the data signals belong to the same cyclical motion,
providing scores and results.
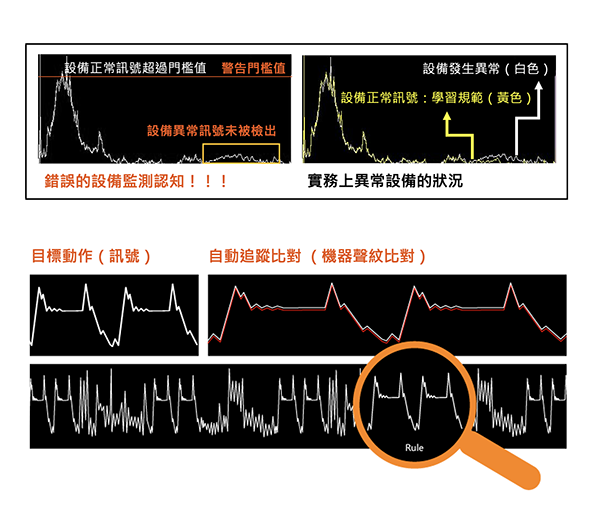
Implementation Challenges
Large Variety of Robotic Arms Making Monitoring Difficult?
Large robotic arms perform various tasks in automotive manufacturing, each requiring different monitoring criteria. Additionally, multiple types of robotic arms may exist within the same production line, requiring maintenance engineers to be proficient in multiple monitoring software systems.
How to Implement
Adapt as Needed – One System for Multiple Machines
The VMS®-ML Machine Learning Smart Monitoring System
is designed specifically for periodic production equipment monitoring.
A multi-channel version can be configured to monitor multiple machines simultaneously.
Using algorithms, the system simplifies results into red, yellow, and green indicators along with scores.
Internal layers retain detailed data scores and feature graphs,
allowing users to apply multiple monitoring standards as needed.
The interface is intuitive, and after basic training, engineers can immediately start monitoring.
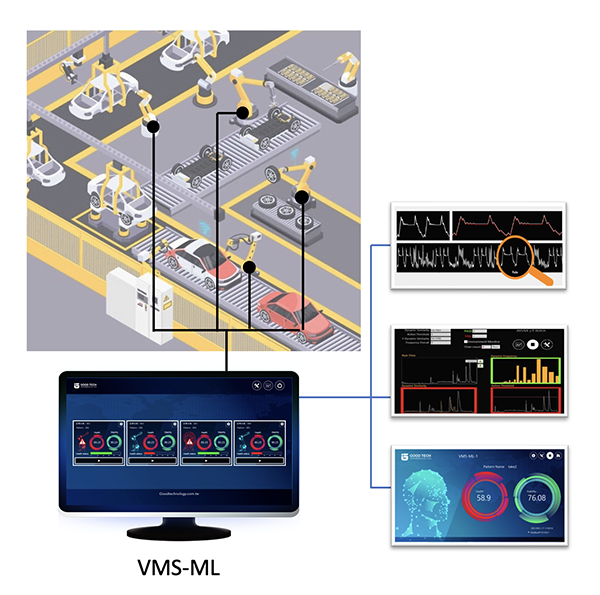
Implementation Challenges
How to Identify When a Robotic Arm Malfunctions?
Large robotic arms perform complex movements and are often tasked with multiple operations. Ensuring quality at each step is essential, as malfunctions may lead to misalignment in assembly, poor weld quality, or defective products, affecting subsequent processes.
How to Implement
Identify Abnormalities & Ensure Smooth Operations
The VMS®-ML Machine Learning Smart Monitoring System
learns correct movement behaviors to establish benchmarks,
monitoring and diagnosing each action to detect any abnormalities
or instability in equipment operation, enabling early predictive maintenance.
By collecting historical health trends,
the system provides data-driven maintenance planning insights.
It also allows stability testing before and after maintenance
to verify repair quality and effectiveness.
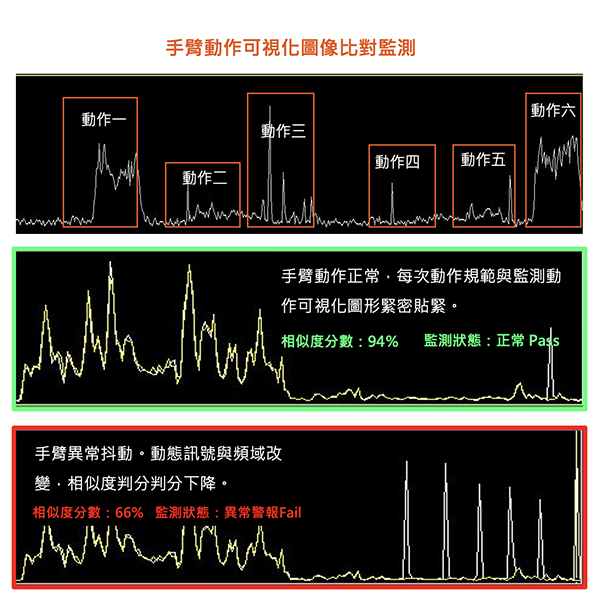
Implementation Challenges
How to Determine the Optimal Timing for Predictive Maintenance?
Large robotic arms must operate continuously and stably over extended periods, avoiding frequent failures or shutdowns. Their operation should not pose risks to operators or other equipment, requiring appropriate safety mechanisms and emergency stop functions. Properly executing predictive maintenance is crucial to ensuring equipment reliability and stability, while determining the right maintenance timing and handling anomalies is key to maintaining production efficiency and quality.
How to Implement
Make the Most Accurate Decisions & Optimize Workforce Allocation
The VMS®-ML Machine Learning Smart Monitoring System
monitors various dynamic signals and performs feature learning.
By continuously comparing accumulated data and characteristics,
the system generates maintenance guidance,
providing users with a reference for repair scheduling.
Additionally, AI predicts remaining equipment lifespan,
allowing users ample time to plan and prepare for maintenance in advance.
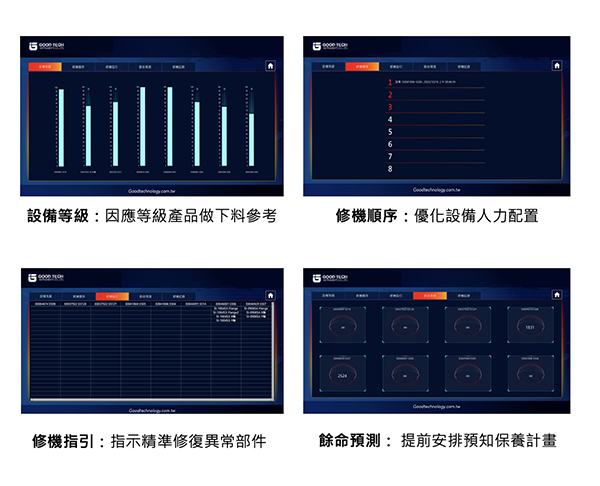
VMS®-ML Machine Learning Smart Monitoring System
Designed for dynamic monitoring of various mechanical equipment, users can easily establish health benchmarks. The system learns from accumulated data, enabling predictive maintenance planning and assisting designers in optimizing production line workflows.
VMS®-ML Machine Learning Smart Monitoring System
Implementation Case
Real-Time Monitoring & Result Analysis of Robotic Arm Status

Factory Environment Monitoring
Reason for Implementation
Impact on Manufacturing Quality & Safety Concerns
In automotive manufacturing, it is essential to minimize environmental impacts such as
CO₂ emissions and airborne particles during production.
Additionally, providing a safe working environment for employees,
ensuring product safety, and promoting sustainability are key factors.
Reducing exhaust emissions and increasing the use of renewable energy contribute to environmental conservation.
Ensuring High-Quality Work Environment
Environmental Quality Impacts:
Temperature Impact:
In metalworking processes such as welding and stamping,
temperature affects the strength and ductility of metals.
Additionally, precise temperature control is crucial for curing and coating drying processes.
Humidity Impact:
High humidity can lead to rust and oxidation of metal parts,
as well as moisture damage to electronic components,
affecting product performance and longevity.
Particle Impact:
During coating processes, airborne particles can adhere to painted surfaces,
affecting the final product quality.
Furthermore, prolonged exposure to high particle concentrations poses health risks for workers.
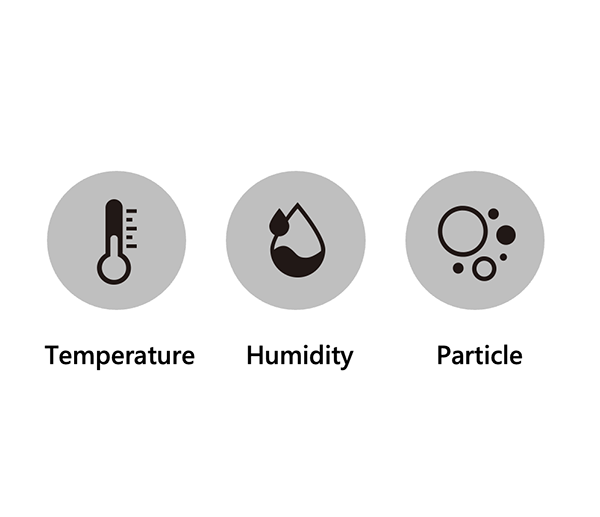
How to Implement
Real-Time Monitoring for Instant Status Overview
Designed for continuous monitoring of temperature, humidity, and particle concentration across industries, the system categorizes data status using signal colors, displaying them on the main screen: Green = Normal / Orange = Warning (First Threshold) / Red = Critical (Second Threshold) / Gray = Not Monitored. Users can switch tabs for quick status review at any time.
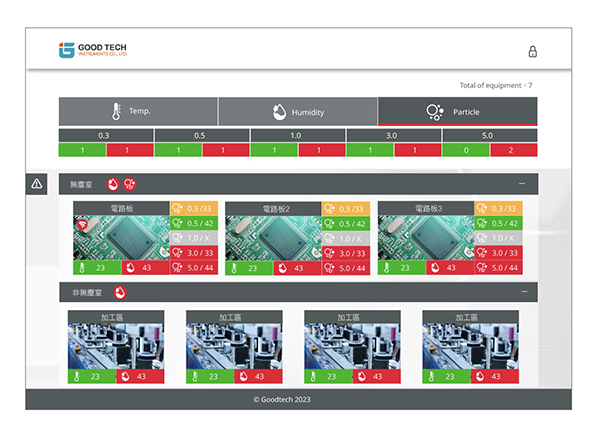
Envir-IoT Environmental IoT
The Environmental IoT system is designed to monitor key environmental parameters, preventing quality degradation and equipment failures due to extreme environmental conditions.
Envir-IoT Environmental IoT
Reason for Implementation
Global Trend: Carbon Reduction & Energy Efficiency
Cost Control:
Energy is a significant operational cost.
By implementing energy management, companies can reduce energy expenses
and lower carbon tax liabilities.
Environmental Protection:
Energy consumption has a major environmental impact,
particularly in terms of CO₂ emissions.
Effective energy management helps reduce consumption and carbon footprint.
Efficiency Improvement:
Energy management ensures high operational efficiency of facilities and equipment.
Optimizing energy use reduces failures and maintenance costs.
Stable Supply:
Proper energy management helps maintain a stable power supply,
preventing blackouts and production interruptions.
This is especially crucial for critical facilities.
Regulatory Compliance:
Many countries and regions have regulations regarding energy efficiency
and environmental protection.
Proper energy management ensures compliance and avoids penalties.
Technological Innovation:
Modern technologies such as smart meters, data analytics, automation,
and AI enhance energy management, helping companies stay competitive.
Execution Challenges
Too Many Settings, Difficult to Operate?
Automotive manufacturing is a highly automated process, and factories rely on multiple monitoring systems. Each system has its own interface and settings, making data integration difficult and increasing the burden on operators during shift changes. Due to the complexity, operators may struggle to ensure proper monitoring.
How to Implement
Simple Interface with Only Essential Information
Gudetech’s IoT systems remove unnecessary information,
converting raw data into practical,
user-friendly monitoring parameters through edge computing.
With minimal settings required,
users can easily manage the system without extensive training.
No programming skills are needed,
and most users can operate the system within an hour.
Once installed, it is ready to use,
and data can also be integrated into a centralized control center.
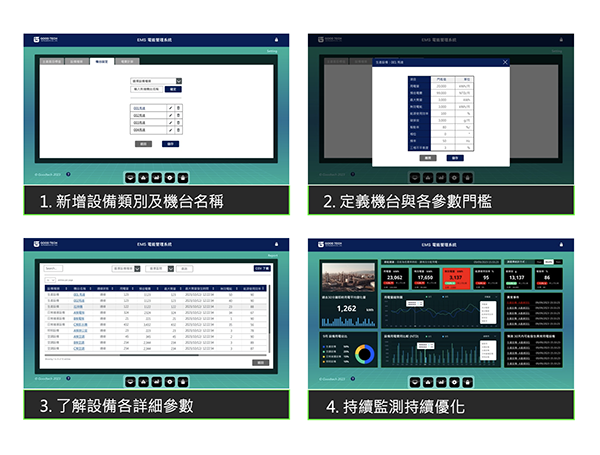
Execution Challenges
Need to Add More Monitoring Points in the Factory or Production Line?
Automotive factories must constantly innovate to keep up with industry trends and regulatory requirements. As monitoring needs evolve, new monitoring points must be added, making a one-time setup impractical.
How to Implement
Flexible Architecture for Gradual Expansion
Goodtech’s IoT monitoring systems adopt a non-invasive measurement approach
and feature a highly flexible architecture.
Users can categorize monitoring areas,
easily rename them, and add new points with minimal effort.
Each monitoring point can be named individually and assigned an image,
making the system intuitive and easy to operate.
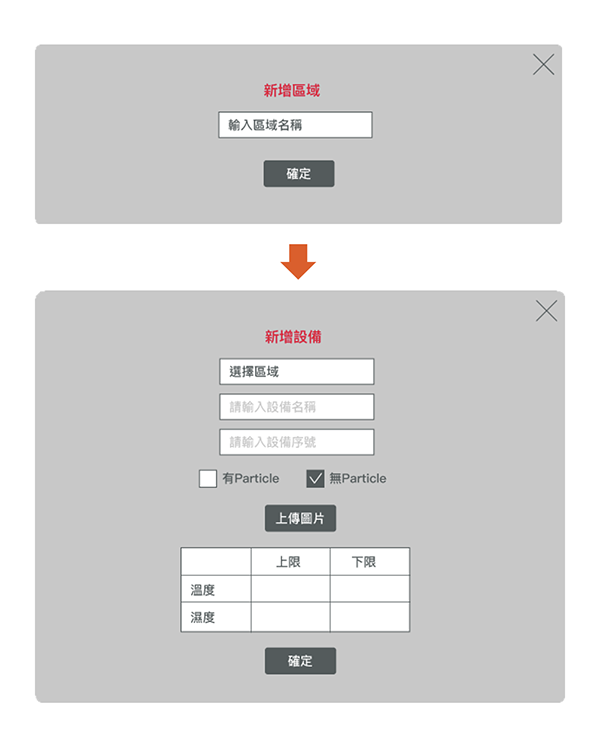
Execution Challenges
Limited by Monitoring Devices, Making Real-Time Monitoring Difficult?
Managers need to access data graphs and reports anytime to improve decision-making transparency and accuracy. Even when off-site, being able to monitor conditions via mobile devices enhances management flexibility and adaptability to market demands.
How to Implement
Enhance Flexibility, Monitor Anytime, Anywhere
Gudetech's monitoring IoT system enables real-time visualization
of production and environmental data.
The system includes a responsive web interface,
allowing users to monitor devices via a local network.
No login restrictions—simply connect to a fixed IP and
access the browser to check equipment status.
Supports iOS, Android, and Windows, adapting to various screen sizes.
Mobile compatibility enhances usability,
allowing real-time monitoring via smartphones.
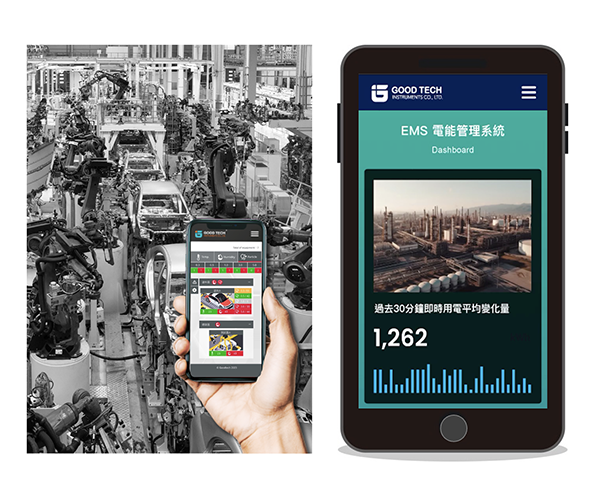
Execution Challenges
Too Many Monitoring Systems, Hard to Integrate?
Factories contain a wide range of equipment,
each with different monitoring systems.
Gudetech’s IoT solutions support integration with
third-party management platforms such as ERP, MES, and CRM.
Alternatively, data can be consolidated into Gudetech’s IIoT Dashboard.
In case of machine issues, users can instantly review the problem,
ensuring quick responses and streamlined factory management.
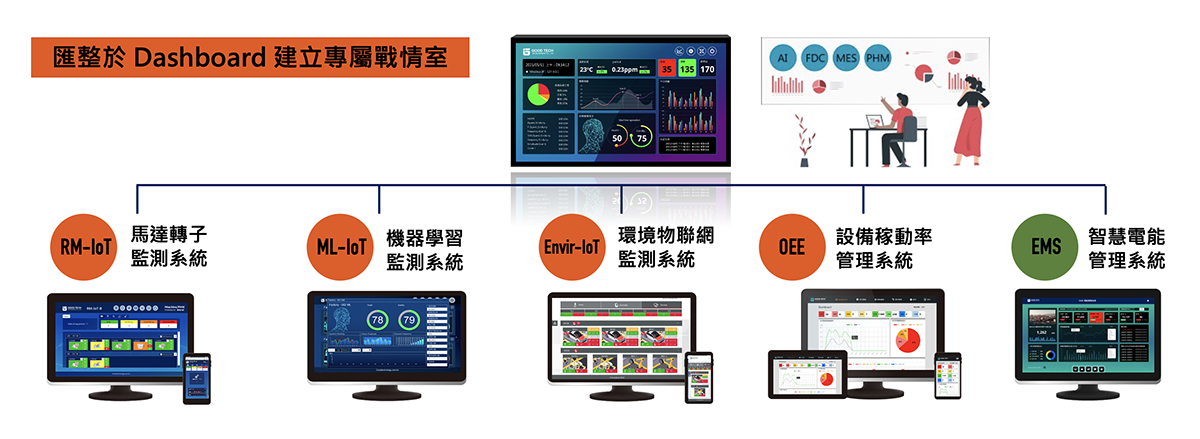
EMS Smart Energy Management System
The EMS system collects and analyzes real-time energy usage data, providing a comprehensive overview of energy consumption. This allows managers to identify energy waste sources and implement targeted energy-saving measures.
EMS Smart Energy Management System
Implementation Case
Precision Component Manufacturing Environmental Monitoring
Problem: During manufacturing, dust particles can interfere with the operation of electronic components. Rapid temperature changes may cause uneven thermal expansion, affecting equipment dimensional stability. High humidity may lead to surface condensation on products, impacting performance.
Solution: Ensuring a Safe Manufacturing Environment
Utilizing non-invasive, high-sensitivity dust particle sensors and temperature-humidity sensors,
the system allows customized monitoring zones based on factory requirements.
Additionally, the system features a dual-threshold function—
when the first threshold is exceeded, an early warning is issued,
allowing users to plan inspections in advance, preventing critical failures (red alerts).
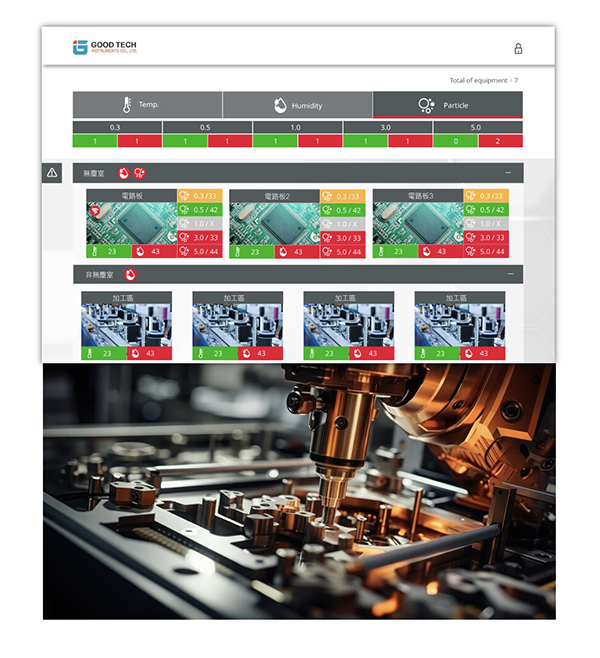
Results:
The system can promptly detect abnormal signals and issue alerts,
ensuring regulatory compliance and maintaining a controlled manufacturing environment.