Common Issues in Quality Control?
Application Field |Quality ControlIn quality control, it is essential to understand shipment quality, finished product quality, and component quality. Quality inspections include dynamic equipment such as no-load rotors, screw sliders, collaborative robot arms, and more.
Implementation Motivation
What issues arise in quality control?
In the era of smart manufacturing, relying solely on intuition is no longer sufficient. To ensure product quality, reduce manufacturing costs, and increase production efficiency, companies must establish a strong reputation and enhance their market competitiveness.
The quality control department plays a crucial role in supervising the production process and maintaining quality standards. By utilizing measurement equipment, they can assess the condition of manufacturing machinery and combine this data with human expertise for effective management.
Quality control requires evaluating shipment quality, finished product quality, and component quality. This includes inspecting dynamic equipment such as no-load rotors, screw sliders, gearboxes, robots, collaborative robotic arms, and industrial robotic arms. Additionally, the structural stability of assembled machines, resonance during operation, and component conditions must be thoroughly diagnosed.
Product quality directly impacts brand reputation
The quality control department is responsible for overseeing production and ensuring compliance with quality standards. Poor product quality can negatively affect corporate reputation and may lead to financial losses due to compensation claims.
For example, a manufacturer discovered during a quality inspection that a blower fan plug had deteriorated over time, leading to overheating, short circuits, and melting, ultimately causing the device to malfunction. Since this defect was identified by the manufacturer rather than reported by consumers, it had minimal impact on the brand's reputation. This highlights the importance of conducting thorough inspections and maintaining accurate records before shipment.
Implementation Process
How should the quality control department plan monitoring for various manufacturing machines?
Quality inspections cover dynamic equipment such as no-load rotors, screw sliders, gearboxes, robots, collaborative robotic arms, and industrial robotic arms. By implementing predictive diagnostics in advance, manufacturers can significantly reduce the occurrence of defective products.
Dynamic Equipment for Shipment
Includes complete machine operation inspection, complex motion equipment, machine structural stability, and interactions between vibrations and components.
No-Load Rotors & Motors
Covers quality inspection of essential products in the quality control field, such as no-load rotors, motors, screws, sliders, and gearboxes.
Robotic Arms
Includes quality inspection of robotic arms required in quality control, such as industrial robotic arms and collaborative robotic arms.
Challenges
How to ensure quality control for various types of equipment?
Diverse Equipment Types
In the era of smart manufacturing, Taiwanese equipment manufacturers are focusing on customized machinery to carve out their own market niches.
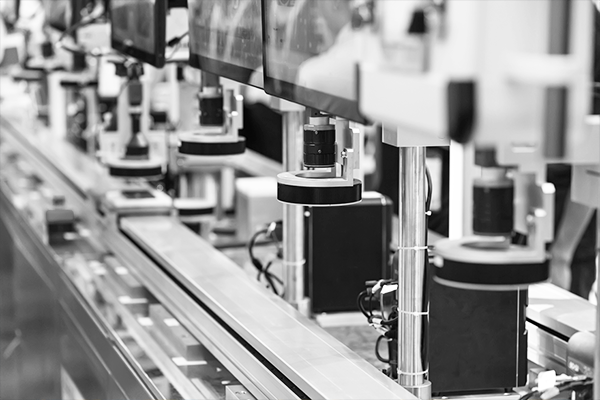
Many manufacturers are designing and producing multifunctional manufacturing machines that integrate various technologies to enhance production efficiency and improve product yield rates in smart production lines.
As a result, the quality control sector must keep up with the changing types of machinery by improving inspection efficiency. Introducing smart inspection technology into production lines enhances product consistency and reliability. In the quality control field, it is essential to inspect in-house manufactured dynamic equipment, ensuring that different models and functional standards meet the required specifications and that components are in optimal condition.
Objectives
Managing Various Equipment in Quality Control
#Machine Learning for Data Accumulation and Comparison
The quality control sector accumulates diverse test data and establishes benchmarks. Machine learning enables quicker identification of subtle differences between machines.
#Detecting Product Quality Issues and Identifying Abnormalities
Before shipment, quality inspection is conducted on various dynamic equipment to measure product quality. Threshold-based inspections are implemented to prevent post-shipment defects or safety issues.
#Fast Analysis of Equipment Issues to Reduce Maintenance Time
Complex machinery with multiple components can be time-consuming to repair. Utilizing equipment monitoring tools can significantly reduce maintenance time, lighten the workload for maintenance personnel, and ensure faster machine delivery.
#Rapid Response to Issues to Uphold Brand Commitment
When a major product defect occurs, immediate recall and root cause analysis are necessary. This response process affects user perception of the company, making preventive measures and contingency plans essential.
Comparison and Analysis
Identifying Issues
Reducing Inspection Time
Quick Problem Resolution
Implementation
Quality Control for Various Equipment
Production lines consist of various types of equipment, each with different operational modes. By monitoring machine vibration quality, we can assess the health of equipment operations. VMS-PM Dynamic Machine Analyzer, developed by Goodtech, quickly identifies issues in machine components and supports intelligent upgrades. Users can optimize equipment using data parameters while ensuring machine quality.
VMS-PM Dynamic Machine AnalyzerBy ensuring the condition of various manufacturing, transportation, and welding robots used on production lines, we can help maintain consistent product quality and prevent mass production of defective items.
VMS-ML Machine Learning Monitoring SystemSupport
Other Equipment-Related Topics