半導体 CoWoS 2.5D パッケージング監視
解決策|半導体 CoWoS 2.5D パッケージング監視ムーアの法則の影響が弱まり、HPC、AI、ビッグデータ処理の需要が増加する中、2.5D パッケージング技術はこれらの分野において最適な選択肢となっている。
導入理由
業界トレンド
半導体の CoWoS 2.5D パッケージング技術は、現在急速に発展しており、高性能コンピューティング(HPC)、人工知能(AI)、データセンターの需要拡大、ならびに回路設計の複雑化により、その市場は成長を続けている。ムーアの法則の限界が見えてきたことで、半導体メーカーは異種集積を活用し、従来技術の制約を克服しようとしている。
2.5D パッケージング技術では、異なるプロセスノードや機能を持つ回路(プロセッサやメモリなど)を同一パッケージ内に集積することができる。この技術により、システム設計の柔軟性が向上し、性能向上や消費電力の低減が実現可能となる。単一パッケージ内でプロセッサと大容量メモリを統合し、高速なデータ転送を可能にすることで、さまざまな先端技術分野で重要な役割を果たしている。
T社の CoWoS 2.5D 技術は、世界の先端パッケージング技術のリーダーとして、すでに多くの高性能アプリケーションに採用されている。他の半導体ファウンドリも同様の技術開発を進めており、市場の 2.5D パッケージング需要は今後も継続的に増加することが予測される。
2.5D パッケージング技術が成熟するにつれ、次の段階として 3D パッケージング技術(例:T社の SoIC 技術)への移行が進むと考えられる。3D パッケージングでは、チップ密度の向上、消費電力の削減、性能向上がさらに期待され、将来的には 2.5D 技術に代わる最先端のソリューションとなる可能性がある。
2020-2027 先端パッケージング市場規模予測 *出典:Yole, 中郵証券研究所
実装方法
製造プロセス異常のリスクを低減し、生産歩留まりを確保
2.5D パッケージング技術は、異なる技術ノードの回路を一つのパッケージ内に統合できるため、機能ごとに最適な設計が可能となる。そのため、設計の柔軟性が向上し、より高度なシステム構築が実現できる。
しかし、高密度化と微細加工技術の発展に伴い、製造装置の精度維持と安定稼働が求められ、プロセス異常や欠陥の発生を最小限に抑えることが重要となる。そのため、設備の状態監視を徹底し、異常を早期に発見して対処することで、設備の復旧プロセスを最適化し、生産計画への影響を最小限に抑えることが不可欠となる。
ウェハーダイシング工程管理
課題
注意!ミクロン単位の精度が工程の成功を左右する
ウェハーは、原材料から最終的なウェハーレベルパッケージ製品になるまで、材料処理、フォトリソグラフィー、エッチング、ドーピング、洗浄、メタライゼーションなど、数百に及ぶ工程を経ます。その後、CoWoS技術を用いた積層によって、高度に集積された多層構造と密集したインターコネクトが実現されます。このため、ウェハー1枚の価値が非常に高くなります。したがって、精度要件がますます厳しくなり、わずかな偏差でも工程の成功に大きな影響を与えます。
ブレードの傾斜切断が引き起こす影響
ダイシングブレードの角度や状態は、正確な切断に影響を与える最も重要な要素の一つです。
ブレードの角度がわずかにずれたり、摩耗・破損がある場合、ウェハーダイのエッジが不均一になったり、
切断幅が一貫しなくなったりします。これにより、マイクロクラック、ダイのチッピング、ダイの破損、斜め切断などのリスクが増大します。
さらに、切断面が不均一な場合、次の切断工程でブレードの摩耗が加速し、破損のリスクが高まります。
その結果、工具交換の頻度が増え、最悪の場合はチップそのものが損傷する可能性もあります。

解決策
データ管理により、ブレード交換時の品質を標準化!
ブレード交換時の品質管理が困難?
切断工程においてブレードの安定性を確保するためには、取り付け時の誤差を最小限に抑えることが重要です。
そこで、VMS-CKシステムを活用し、データ管理によるブレード交換作業の標準化を実現します。
ブレード交換時には最大4回の角度調整を行い、最適なダイナミックバランスを確保します。
これにより、取り付け時の標準化を徹底し、ブレード交換後も安定した振動品質で精密な切断が可能になります。
VMS-CK 切断ブレード品質監視システム
長期間の使用による部品の摩耗、構造共振、駆動モーターの異常などが発生すると、異常振動を引き起こす可能性があります。
そのため、主軸および移動軸の品質を監視し、振動異常がブレードに伝わるのを防ぐことが重要です。
VMS-CK 切断ブレード品質監視システム を活用することで、ブレード品質の状態をリアルタイムで把握できます。
システムはしきい値管理を使用して変動を事前に検出し、不良品を引き起こすブレードの傾きや取り付けミスを未然に防ぎます。
ダイ位置合わせ・貼り付け工程監視
課題点
些細な問題が全体の品質に影響を及ぼす
ダイボンディング工程において、ダイ貼り付け機 はウェハからダイを個別に分離し、パッケージ基板上に配置する役割を担います。 そのため、ミクロン単位の高精度な位置制御と安定性が求められます。 ダイ貼り付け機の各軸は連続して高負荷運転を行うため、モーターが不安定になったり故障すると、位置決めの精度が低下し、バッチ全体の品質に影響を及ぼし、不良品の発生や生産ラインの停止を引き起こす可能性があります。
ノズル圧力異常によるダイ欠陥
ダイ貼り付け機の ピック&プレース工程 では、ノズルが 真空圧 を利用してダイやウェハを移動させます。 真空圧の強さはノズルの吸着能力に直接影響を与えます。 ノズルがウェハの表面に接触する際、適切な圧力をかけることで安定した吸着を実現します。 圧力が低すぎると、吸着不良を引き起こし、逆に圧力が高すぎるとダイが破損し、不良品の発生や材料の損失を招きます。
空圧シリンダーの品質が位置決め精度に影響
貼り付け工程では、空圧シリンダーが均一な圧力を供給することで、はんだの均一な分布と確実な接合を実現します。 しかし、空圧シリンダーには 油や異物の混入によるバルブ詰まり、軸ずれによる作動不良、異物混入による引っかかり現象 などの異常が発生する可能性があります。 空圧シリンダーが不安定になると、ダイの位置決め精度が低下し、電気的接続不良を引き起こし、最終的に製品の機能不良を引き起こす可能性があります。
解決策
モーター電流の変化を監視し、異常を早期発見!
ダイ貼り付け機の移動軸品質をどう確保するか? 貼り付け機の移動軸はボンドヘッドを駆動し、モーターの安定した動作がスムーズな移動を実現します。 しかし、潤滑不足・摩耗・詰まりなどが発生すると、機械的抵抗が増加し、モーターが通常よりも高い電流を必要とするため、電流の急激な変動や振動が発生します。 そこで、IoTベースの品質監視システムを活用し、移動軸の電流変動をリアルタイムで監視することで、異常を早期発見し、ダイ貼り付け機の安定稼働を確保します。
DB-IoT ダイボンダー品質監視システム
吸着と搬送動作を一貫して行い、生産ラインの高効率な運用を維持するために、ダイボンダーの異常動作を即座に特定する必要があります。
動作エラーや失敗率を削減し、生産効率を向上させるには、詳細なデータ分析が不可欠です。
DB-IoT品質監視システム を活用することで、動作データや頻度の履歴を詳細に記録し分析できます。
これにより、故障の根本原因を迅速に特定し、トラブルシューティング時間を短縮し、オペレーターの適切な意思決定を支援します。
ダイ・ウエハーのリフローはんだ付け・固化工程の監視
実行時の課題
工程の中断は失敗につながる!
リフロー工程中の異常振動?
リフロー工程では、装置の安定した動作が工程の信頼性と製品品質にとって重要です。
装置の不安定な動作や異常振動が発生すると、溶融したはんだがずれ、
はんだブリッジやダイの位置ずれを引き起こす可能性があります。
工程中に異常が発生すると、はんだ付けが中断し、
バッチ単位での不良や工程の再スタートが必要になることがあります。
そのため、スムーズで安定した工程の維持が不可欠です。
実行方法
ダイのずれを防ぎ、歩留まりを向上!
材料のずれを防ぐには?
リフロー工程では、加熱によりはんだを溶融させ、
再凝固することでダイと基板の強固な接合を実現します。
空圧シリンダーや電動シリンダーが加熱盤を上下に動かしながらはんだ付けを行う際、
シリンダーの動作が不安定だと、接合部分の材料がずれる可能性があります。
VMS-M14 監視システムを活用することで、
空圧シリンダーや電動シリンダーの加熱盤駆動時に発生する振動特性を監視し、
機構の劣化や故障による異常振動が原因で材料が接合時にずれる現象を防ぐことが可能です。
VMS-M14 動的監視システム
信号をどの条件で遮断するかを決定するために、円筒駆動の主軸にセンサーを設置し、
上昇・下降時に発生する振動値を測定します。
測定した振動特性は数値データとしてデジタル化され、大規模データベースに蓄積されます。
ユーザーがしきい値を定義することで、円筒の状態品質をリアルタイムで管理できます。
メイン画面では信号機のような色分け表示で状態がリアルタイムに可視化されます。
振動値がしきい値を超えた場合、装置は即座に信号を遮断し、
その後のウエハー処理による貼り合わせのずれや材料破損を防ぐことができます。
硬化後の樹脂切断工程管理
実行上の課題
樹脂切断工程の異常によるダイ割れ・欠けの発生?
樹脂切断工程において、前工程でダイが斜めにカットされていた場合、 ダイシングブレードが目標位置に達する前にダイに接触する可能性があります。 これにより、ダイの割れや欠けが発生し、品質異常を引き起こします。 このような問題を防ぐために、VMS-CKシステムを活用し、 切断サイクル中の振動特性を監視し、変動の兆候を早期に把握します。 このリアルタイム監視により、連続的な製品損傷を防ぎ、 実際の使用状況に応じた最適なプロセス管理を実現できます。
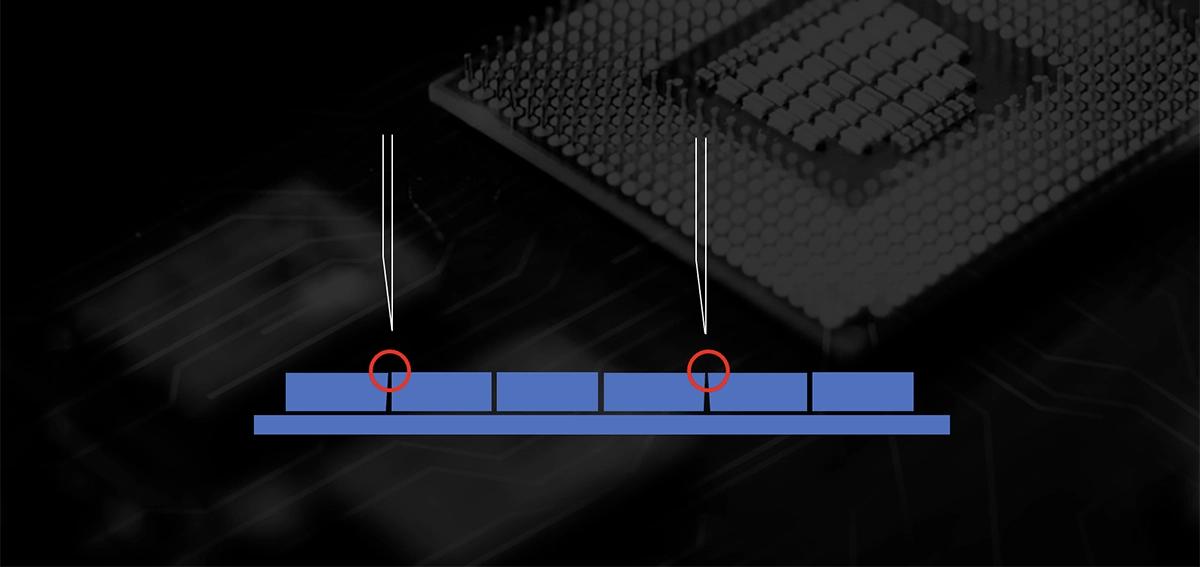
実施方法
リアルタイムデータ分析による製品保護!
前工程でダイが斜めにカットされていた場合、 ダイシングブレードが目標位置に達する前にダイへ接触することがあり、 ダイ割れ・欠けなどの品質異常が発生する可能性があります。
VMS-CK 刃物品質監視システム
この問題を防ぐために、VMS-CKを活用し、 切断サイクル中の振動特性を監視し、変動の兆候を早期に把握します。 このリアルタイム監視により、連続的な製品損傷を防ぎ、 実際の使用状況に応じた最適なプロセス管理を実現できます。
VMS-CK 刃物品質監視システム実施効果
性能向上、納期短縮!
製品歩留まりの向上:
装置の品質管理を徹底し、切断やダイ搭載工程におけるずれや欠陥を減少させる。
設備の寿命延長:
適切な予知保全を実施し、交換頻度とコストを削減し、設備の使用寿命を延ばす。
生産効率の向上:
各ウエハーの切断品質を一定に保ち、品質問題による手直しや廃棄を削減する。
稼働停止時間の削減:
定期的な設備と刃物の保守を行い、故障や損傷によるダウンタイムを最小限に抑える。
競争力の強化:
厳格な品質管理により、すべての製品の一貫性と高品質を確保し、顧客満足度を向上させる。
納期短縮:
効率的な生産プロセスと低い手直し率により、生産サイクルを短縮し、市場の需要に素早く対応。
Support
その他の半導体関連分野