Common Issues in Fab Operations?
Application Field |FabThe wafer manufacturing process in Fab operations is highly complex. Each stage can be affected by anomalies in equipment operation. Start predictive diagnostics for your equipment today.
Execution Motivation
Common Issues in Fab Operations?
The semiconductor Fab (Fabrication) industry includes crystal growth plants, wafer foundries, IC manufacturing, packaging factories, and panel manufacturing. During wafer production, silicon wafers are purified, grown, sliced, and polished before IC chips are manufactured. The IC manufacturing process involves multiple steps, including metal sputtering, photoresist coating, etching, and photoresist removal. Once the wafers are complete, they are cut into IC chips and sent to packaging plants.
Wafers are the most commonly used semiconductor material, typically available in 6-inch, 8-inch, and 12-inch diameters. Currently, 8-inch wafers dominate the market, widely used in electronics such as televisions, computer peripherals, mobile devices, and consumer electronics. Additionally, the growth of automotive electronics, AI, IoT, and edge computing has further expanded wafer applications.
Key Factors Affecting Production Line Yield
The wafer manufacturing process is intricate and highly challenging, especially with nanometer-scale fabrication. Even minor defects or contaminants can significantly impact yield. Several factors contribute to defects in Fab processes, including poor vibration isolation of floors, mechanical looseness, abnormal machine operations, machine-to-machine interactions, abnormal rotation vibrations in crystal growth furnaces, rail wear affecting wafer transport vibrations, poor cutting performance of crystal rods, uneven grinding surfaces, chamfering issues, and vibration anomalies. These issues can lead to defective wafers, mass chip breakage, and even production downtime, resulting in severe losses.
How to Execute
Various Equipment Affecting Fab Process Yield?
As mentioned earlier, Fab production processes are extremely complex, requiring high-precision equipment that is highly sensitive to micro-vibrations. Besides considering equipment placement for specific machine models, it is also crucial to assess whether vibrations from different machines interact with each other.
Impact of Micro-Vibrations in the Environment
Factors such as elevated floors in the factory, vibration isolation platforms for specific machines, robotic arms for transport and storage, and chemical storage handling arms can all impact micro-vibrations in the environment.
End-Stage Rotating Equipment
Rotating equipment at the final production stage, such as various motors, pumps, fans, and key components like screws and rails that drive machine movement, can impact overall stability.
Impact of Equipment Quality
Various coating techniques such as spin coating, slit coating, spray coating, and wafer grinding machines all play a critical role in the fabrication process.
Execution Challenges
How to Diagnose Micro-Vibrations in Fab Environments?
Micro-Vibrations Affecting Equipment
Fab production processes are highly complex, and the required equipment is extremely precise. These machines are highly sensitive to micro-vibrations. Besides considering placement when installing specific models, it is also crucial to assess whether vibrations from different machines interact with each other.
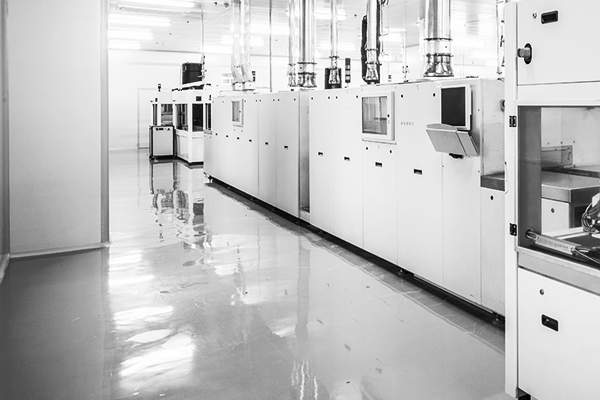
When installing elevated floors, do you understand their vibration isolation efficiency? Additionally, can the minor shaking of robotic arms transporting wafers be detected early to prevent severe damage to wafers or IC chips? How do you find the best placement for newly purchased precision instruments? How can long-term environmental micro-vibration measurements be conducted while ensuring real-time monitoring?
Execution Goals
Mastering Micro-Vibrations in Fab Environments
# Understanding Vibration Isolation Efficiency and Reinforcement
Precision equipment in Fab environments requires high accuracy and is often installed with vibration isolation platforms. However, these platforms degrade over time, reducing their effectiveness. Understanding and evaluating their efficiency allows for timely reinforcement or replacement.
# Identical Equipment, Different Vibration Structures
Even when using the same model of precision equipment, variations in assembly and component conditions lead to different vibration structures. Factors such as belt tension and component wear influence the vibration frequency during operation.
# Natural Frequency and Machine-to-Machine Interactions
How can Fab precision instruments maintain stability while avoiding interference with other machines? Structural vibrations are inevitable. When vibration sources and frequencies align, can resonance be prevented? How does resonance impact processing precision?
# Vibration Detection for New Equipment Installation
When purchasing new precision instruments, it is crucial to consider whether their placement will be affected by vibrations from other machines. Is the newly installed vibration isolation floor suitable for the machine? What is the optimal spacing between machines?
Vibration Isolation Efficiency
Machine Vibration Structure
Machine-to-Machine Interaction
Machine Installation Environment
How to Execute
Diagnosing Environmental Micro-Vibrations
Environmental micro-vibrations affect Fab manufacturing processes and equipment performance. Through long-term environmental micro-vibration monitoring, it is possible to assess machine-to-machine interactions, internal interference sources, vibration origins, and error detection. This allows for vibration level testing, evaluation of vibration isolation capabilities, and assessment of vibration control system efficiency.
Environmental Micro-Vibration Levels
Using GoodTech’s **VMS-EM Environmental Micro-Vibration Monitoring System**, users can analyze how environmental resonance impacts equipment, evaluate the vibration levels of elevated floors and specific machine locations, and generate real-time monitoring and trend analysis.
VMS-EM Environmental Micro-Vibration Monitoring SystemExecution Challenges
How to Monitor Fab End-Stage Rotating Equipment?
Various Motors, Pumps, and Fans
Motors, pumps, and fans are widely used in Fab environments and significantly impact equipment costs and power consumption. They must operate under high-temperature or high-voltage conditions, and their speed and torque influence precision and equipment quality.
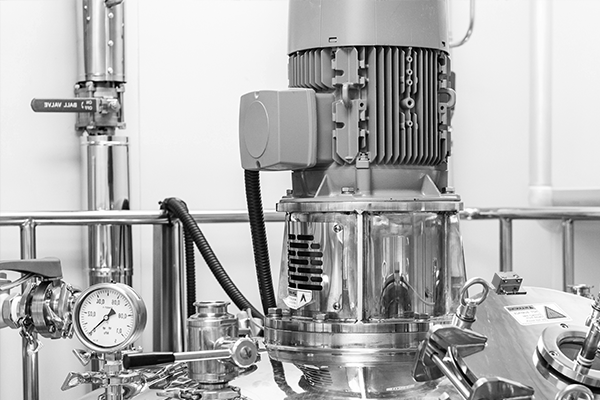
By collecting and analyzing key data such as power consumption, current, vibration, and rotational speed, it is possible to predict anomalies, identify abnormal operation sources, and implement preventive maintenance, reducing downtime caused by failures.
Execution Goals
Mastering Various End-Stage Rotating Equipment in Fab
# Prevent Unexpected Failures and Ensure Consistent Product Quality
Motors, pumps, and fans in Fab processes critically impact manufacturing quality. Abnormal vibrations during operation can reduce yield rates. Continuous monitoring of equipment performance helps minimize variations, maintaining consistent product quality and wafer integrity.
# Extend Equipment Lifespan with Clear Maintenance Schedules
These Fab machines are expensive, have long procurement lead times, and involve high material costs. Unexpected downtime for maintenance can significantly reduce production efficiency. By accurately assessing equipment conditions, preventive maintenance can be scheduled outside production hours, extending lifespan and optimizing efficiency.
# Built-in ISO Standards for Real-Time Quality Monitoring
The software system integrates ISO standards for rotating equipment, enabling Fab personnel, even without technical expertise, to easily assess the quality of motors, pumps, and fans. Automatic vibration analysis based on ISO guidelines helps manage these devices, store measurement history, and generate reports.
# Real-Time Monitoring and Automated Alerts
If anomalies occur in Fab motors, pumps, or fans, immediate action is required to prevent production losses. Customizable alert workflows ensure timely responses, while the user-friendly interface provides real-time quality monitoring for easier interpretation.
Prevent Unexpected Failures
Clear Maintenance Scheduling
Built-in ISO Standards
Automated Alerts
How to
Execute
Monitoring Fab End-Stage Rotating Equipment
The wafer manufacturing process is highly complex, with every step influencing wafer quality. The **RM-IoT-NET Rotating Equipment Health Monitoring System** enables remote management, long-term online monitoring, and trend analysis. This system helps evaluate the health of rotating equipment, allowing for predictive maintenance and preventing unexpected downtime.
RM-IoT-NET Rotating Equipment Health Monitoring SystemFor critical equipment, the **VMS®-M Series Custom Monitoring System** offers tailored monitoring workflows and full control over essential machinery based on user needs.
VMS-M Series Custom Monitoring SystemExecution Challenges
How to Monitor Equipment Quality in Fab?
Precision and Complex Manufacturing Equipment
In Fab manufacturing processes, whether it’s wafer production, wafer cutting, IC fabrication, or packaging, the equipment used is highly precise.
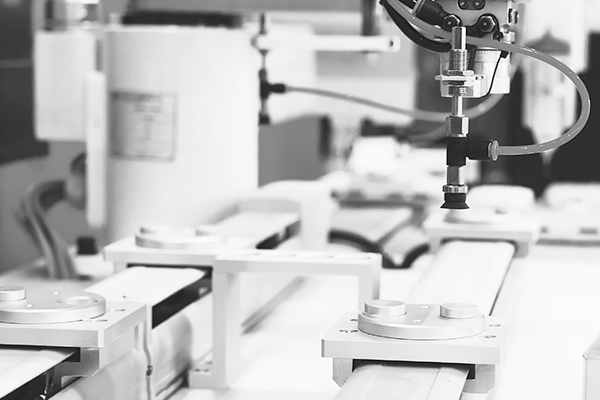
Due to the intricate and complex nature of these processes, defects or errors cannot be tolerated, including in the machines themselves. Fab equipment includes Spin Coating, Slit Coating, Spray Coating, Wafer Grinding Machines, Die Saw, Laser Cutting, AOI Machines, and Wafer Bonders.
Execution Goals
Mastering the Status of Various Fab Equipment
# Prevent Unexpected Failures and Avoid Defective Production
Fab equipment operates with high automation, involving various complex machine types with long processing times. A sudden shutdown or abnormal vibration can waste all prior production efforts and significantly increase costs. Therefore, precise monitoring of machine status is necessary to prevent unexpected failures.
# Extend Equipment Lifespan with Clear Maintenance Scheduling
Fab equipment plays a crucial role in production capacity. Unexpected maintenance can lower yield rates, increase product loss, and raise defect rates. By accurately assessing equipment quality, maintenance can be scheduled during non-operational hours to extend equipment lifespan and efficiency.
# ISO Standards and Custom Thresholds for Quality Assessment
The monitoring system accumulates long-term data and establishes measurement workflows based on ISO standards and user-defined criteria. Users can set custom threshold values, review trend analysis, and monitor real-time dynamics.
# Real-Time Monitoring to Identify Root Causes
Fab machinery is highly precise with complex components, requiring strict process control. By using sensors for continuous measurement, users can set alert thresholds based on accumulated data. If anomalies occur, warning messages can be triggered for timely intervention.
Prevent Defective Production
Clear Maintenance Scheduling
Real-Time Equipment Quality Assessment
Identify Root Causes
How to Execute
Equipment Quality Monitoring
Fab environments involve a variety of complex equipment types that are difficult to maintain. Many processes are intricate and highly precise, making it challenging to detect component failures. Installing monitoring systems can help users accurately assess equipment status.
Machines with Repetitive Motion
High-performance monitoring is essential for repetitive motion machinery. The **VMS®-ML Machine Learning Intelligent Monitoring System** can be applied to various repetitive motion equipment, detecting real-time mechanical signals. Even the slightest abnormality can be identified, allowing preventive maintenance to address potential faults before they escalate.
VMS-ML Machine Learning Intelligent Monitoring SystemDynamic Machinery Issues
For various dynamic machinery issues, the **VMS®-PH Portable Dynamic Equipment Analyzer** enables fast identification of root causes.
VMS-PH Portable Dynamic Equipment AnalyzerSupport
Other Fab-Related Equipment